Tolerance specification communicates the allowance for part variation. Variation happens, and when it is within what we expect, great.
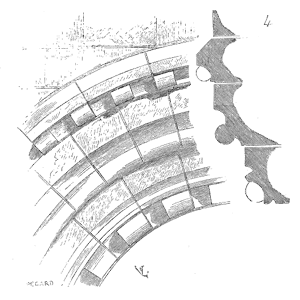
If your product is stronger than the applied stress, it should work. The stress/strength relationship concept is well known, but did you know stress and strength change over time? Let's use the best information and tools for this analysis.
The key idea of stress/strength or derating for electrical engineers is to design a product using materials and components with the suitable strength to withstand the stress condition experienced over the expected duration of use. The term margin refers to the distance between the minimum strength and expected maximum stress. We know failures are more likely to occur when little or no margin exists.
Let's discuss the information necessary to understand the expected stress and the strength and how both will change over time. There are several ways to estimate failure rates depending on your available data. The better your data, the better your estimates.
The engineers doing the design work select the materials and components and need the best available understanding of stress and strength and how they change over time to design in reliability right from the start. While desirable to get data for every material type and component and every possible applied stress, that just isn't feasible. So, let's also talk about a few strategies to narrow the focus to the critical few that require the best possible data for a stress/strength analysis.
As always, this webinar will be very interactive, with plenty of prompts for your comments and questions. So, bring your questions and problems around applying stress/strength concepts. Let's discuss how you can improve your product's design with a better analysis.
This Accendo Reliability webinar originally broadcast on 25 September 2018.
To view the recorded video/audio of the event visit the webinar page.
Strength-Stress with Limited Information episode
How to Set Environmental Specifications for Testing episode
Improving Fatigue Resistance article
Test Reliability Targets and Expected Field Reliability article
Tolerance specification communicates the allowance for part variation. Variation happens, and when it is within what we expect, great.
Early and often during product development, the team needs to know the expected and meaningful reliability prediction of the current design.
One of the challenges for reliability engineering in product development is reliability integration into the product development process.
How a focus on variability with process control, process capability and tolerances helps to improve reliability.
How a focus on variability with process control, process capability and tolerances helps to improve reliability.
If a person is not able to interact with your product, with or without the manual, they may consider your product a failure.
How to find and analyze temperature readings over a 10 year period, create histogram and determine how many hours below freezing may exist.
There are three approaches to set tolerance limits. Each has ramifications for the eventual manufacturability and reliability performance.
Warranty returns are a great start for setting targets for new products. But how do you translate that to specific numbers to design to?
DFR is more than a set of tools or activities, let's explore the building of a reliability culture that support reliability thinking
Fault tolerant design principles are the best approach to reliability. Or not. It depends on your design challenges.
Besides building your product inside your customer's facility, your product requires transportation to move your product.