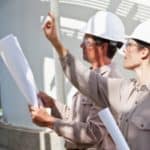
In past articles I have often referenced Dr. Aubrey Daniels and the use of Behavioral Psychology and Analysis in the workplace. In the late 1980’s I was fortunate enough to attend a 2-week course in Performance Management put on by Dr. Daniels and two of his associates where we learned the importance of measuring behaviors as opposed to results. To say that this course was enlightening would be an understatement as it was in this class I first learned why we need to measure leading indicators as opposed to results.
Dr. Daniels used several examples in the course to clearly show that it’s our behaviors that drive results yet to this day over 90% of the measures used in business today are focused on results.
To drive this point home, Dr. Daniels referred to a quote made famous by Dr. Ogden Lindsley in 1965; “If a dead man and do it, it isn’t a behavior and you shouldn’t waste your time trying to produce it.”
While this statement seemed odd at first, he went on to explain this rule by asking us about our company’s HSE (Health, Safety & Environment) program.
“How does your company measure employee safety? Are you measuring hours or days without a loss time accident? Do you measure the number of hours or days without a OSHA reportable incident? The number of days without a reportable spill?” And finally; “Do you set goals using these numbers and celebrate them when they are achieved?”
“If the answer to any of those questions was yes, you are violating the Dead Man’s Rule and have done absolutely nothing to change the behaviors that drive a safe work environment. Now I know this sounds strange, but I could bring a dead person to work and they could be there an infinite number of days or hours and not get hurt or cause a spill. If you want to improve your HSE program you have to begin measuring and reinforcing safe behaviors.”
More than thirty years later, nothing has changed. Nearly every company I visit or work with measures results when it comes to their HSE program. The ultimate irony regarding this came on April 10, 2010 when several Managers flew out to the Deepwater Horizon to celebrate 7 years on the drilling rig without a lost time incident. Several hours later the rig would explode killing 11 workers.
With this thought in mind, we should all look to change how we measure our HSE programs by focusing on behaviors (leading indicators) as opposed to results (lagging indicators).
Listed below are 10 behaviors we can measure to help improve our HSE programs.
1. Leaks Identified/Leaks Eliminated – In my 18 years working as a consultant I have visited and worked with hundreds of companies and in all that time I have yet to find a site that didn’t have leaks. I don’t care if its water, air, oil or hydrofluoric acid every leak creates a potential incident. Start identifying your leaks, open work orders to repair them and track leaks reported versus leaks repaired.
2. HSE Walk Throughs Performed – Just the behavior of having Supervision, Managers or Team leaders performing HSE walk throughs to identify potential risks or hazards helps to send the message that your company cares about its employees.
3. Safety Concerns Identified/Safety Concerns Addressed – While performing HSE walk throughs, we need to begin identifying HSE risks or concerns, documenting which concerns have been addressed and communicating to employees what has been done to address the concerns.
4. LOTO Audits Performed/Issues Noted & Corrected – Depending on the size of your organization, dozens or even hundreds of LOTO’s can be performed in a day. When it comes to changing behaviors, one of the best activities we can do as Supervisors and Managers is to begin auditing the LOTO process. In performing these audits, how many issues were noted where the LOTO could have been more thorough and how many of these were corrected. (Sometimes we lack proper valving for double block and bleed for example)
5. Confined Space Entries Audited/Issues noted & Corrected – Using the same logic in LOTO Audits, this can and should be applied to Confined Space Entries.
6. Audits performed on equipment pick/place for removal/maintenance – The rigging involved with equipment removal and replacement often requires an additional level of thought and expertise yet very few companies audit this process on a regular basis. Look to ensure all lifting devices (Chain Falls, Come-Alongs, and Slings) have been inspected and are suitable for use. Keep the area free from foot traffic. Ensure the load is properly balanced. Track and identify potential issues and issues resolved. (Have proper pick points been designed and installed?)
7. PPE Audits Performed/Issues Noted & Corrected – Nearly every site I have visited has a few jobs that require special PPE be worn to properly perform the job. Audits of these jobs should be performed on a regular basis and any issues regarding the PPE should be recorded and addressed.
8. Near Misses Identified/Near Misses Addressed – In my experience, this is one of the toughest behaviors to get started. If we truly want a safe environment for our employees, we must reinforce the behavior of coming forward with near misses. This means we need to reward employees when they come forward with close calls, safety issues, small spills that could have become huge spills. Near misses occur on a regular basis and we need to have our people feel comfortable that they will not be punished for reporting them.
9. 5S Inspections Performed/Issues Identified & Corrected – A cluttered workplace is an unsafe workplace. Set up regular 5S inspections of various parts of your plant site including operating areas, maintenance shop and office areas. Record issues identified and issues resolved.
10. Ergonomic Issues Identified/Resolved – Repetitive motion injuries can result in loss time incidents as well as long and short-term disabilities. It should be a priority to have someone knowledgeable in this field observe the routine jobs performed at your site to identify potential ergonomic issues, recommend how to mitigate these issues and then track each through resolution.
As we look to put some behavior based leading indicators in place now is the time to also set up a plan to reinforce the correct behaviors. Reinforce those who have done a thorough job to ensure their lock-out tag-out, confined space entry, or pick and place was perfect. Reinforce people for reporting near misses and remember to reinforce those who took the time to perform all of audits we have deemed necessary to drive the correct behaviors. Remember to take the time to develop good base line numbers and set goals around solid behaviors and the results your company looks to achieve regarding a sound HSE program will without a doubt, follow!
Douglas Plucknette is the creator of RCM Blitz™, the author of Reliability Centered Maintenance using RCM Blitz™ and Clean, Green and Reliable a best-selling book on how to reduce energy consumption in manufacturing plants through equipment reliability. Doug has published over 100 articles on Maintenance and Reliability, and has been a featured Speaker as well as Keynote Speaker at a countless number of conferences around the world.
Leave a Reply