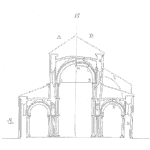
In Chapter 8 of The Basics of FMEA by Robin E. McDermott, et. al. discusses the ten steps for an FMEA. I find it to be an excellent summary for describing and conducting a failure mode and effect analysis.
Therefore based on the work of McDermott and others, plus my own experience here are the ten steps with my descriptions.
Step 1 Review the process or product
With the team, clearly define the subject of the FMEA study. What is and is not included. Discuss the basic features, assembly, materials, construction, and desired functions.
Step 2 Brainstorm potential failure modes
What could go wrong?
This can be a lot of fun. Use a variety of brainstorm techniques to get as broad a set of ideas as possible. A good technique is to individually create ideas the collate them using affinity grouping. Mix up the process with live brainstorming, anchoring, and focused concerns (i.e. high temperature, user abuse, etc).
For most products, you may want to focus on one function or feature at a time.
Step 3 List potential effects of each failure mode
What could happen if the failure occurs?
Consider the possible failures and imagine what could then happen to the surrounding environment and people.
For example, if a staircase handrail fails to provide support, it may result in the effect of a staircase falling injury. Or, it may result in the closing of the staircase for repair. Or, it may require a maintenance action to re-anchor the handrail.
Step 4 Assign a severity ranking for each effect
For each effect (consequence) provide a ranking score. Common scales include 3, 5, or 10 points. I often start with 10 point scale and adjust depending on the team and nature of the study.
Common practice is to assign 9 or 10 for those effects that cause injury or death, or major damage to its surroundings.
Document the scale actually used so others can interpret the study results properly.
Step 5 Assign an occurrence ranking for each failure mode
How often will the failure mode occur?
The worksheet includes a column of causes, which may help the team judge the relative frequency of occurrence of failure modes. Keep in mind that a failure mode may have many potential causes.
Step 6 Assign a detection ranking for each failure mode and/or effect
Detection is a bit different in ranking then severity or occurrence. A high score means the effect occurs without warning. It is not detectable.
Detection can include one or both of the following methods for alerting of potential failure.
- During product development and manufacturing can we find the defect that would lead to a failure? Can we find the problem before it is shipped?
- During normal use does the product provide some means to detect an upcoming failure?
I use the example of car brakes to illustrate. During design and manufacture, we can test the brake assembly for braking force. If insufficient, we can redesign or adjust the brake assembly before installation in a vehicle.
One failure mechanisms that leads to brake failure is the wearing away of the brake pad. Therefore, the insertion of a piece of metal that creates a warning sound before the brake pads have worn too far, alerts the vehicle operator to replace the brake pads before brake failure occurs.
Step 7 Calculate the risk priority number for each effect
Just a bit of math. Multiple the severity, occurrence, and detection scores together to find the RPN value.
Items that high dire consequences (high severity), occur often and provide no warning result in the highest RPN numbers relative to other potential failures.
Step 8 Prioritize the failure modes for action
I recommend a three-step process here.
- Address the severity 9 and 10 rankings as they are related to safety.
- Review the prioritized ranks for groups of failure modes that one ‘fix’ (redesign, evaluation, or process improvement) may address. The RPNs of the individual lines may not be the topped ranked value, yet collectively the action may provide significant risk reduction.
- Address the highest remaining RPNs as the represent the remaining risk to the product working as expected.
No team that I know of addresses every potential failure. It is a balance of safety, functionality, customer expectation, and resources.
Step 9 Take action to eliminate or reduce the high-risk failure modes
Assign action items. These may include gathering information, conducting experiments, considering design or process improvements, adding or removing functions, etc.
The idea is to do something with the study. The prioritized list provides a guidance document that the entire team can use to focus on the highest risk areas first.
Step 10 Calculate the resulting RPN as the failure modes are reduced or eliminated
Document the changes to the product. Ideally, the results of completed actions will reduce the risk.
Be sure to consider new information and function and recalculate. FMEA is a process and as the program evolves and grows so should the FMEA. It’s a tool, that helps the team address risks. Used as such it provides value.
Related:
Effective FMEA Principles (article)
Reliability Role and Safety and Liability (article)
Benefits of Fault Tree Analysis (article)
Thanks for the post! Lots of good FMEA information here in this short article. I especially like some of the examples you used (e.g. staircase handrail and brake failures) to elaborate on some of the steps.
Hi Michael,
Glad you enjoyed and thanks for the kind words.
Cheers,
Fred
Thanks Fred. I found it very helpful. Can I share this on Linkedin?
Yes, please do. cheers, Fred