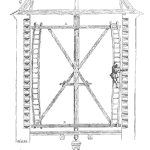
Continuing the series that started with maintenance supervisor and reliability engineers, if you are new to the position of Operations Supervisor, what are some of the things you can begin working on immediately to improve reliability within the area you work?
1. Learn Your Process
The first thing someone is going to tell you on the day someone touches you on the forehead and appoints you an Operations Supervisor is: “you don’t need to learn how the equipment works or how the product is made, you just need to learn how to manage people.” Take it from someone who has been there, that is a bunch of bull crap. Something tells me that Steve Jobs and Bill Gates have a very good idea what it takes to make a computer and write software, and in the early days of their respective companies, they both had to supervise people. In this new job, you will be expected to make decisions that will impact the products you make and the customers they are sold to, so your first priority should be to learn the process and learn it well. Lean on your most experienced operators to show you the ropes and start going through production data as well as failure history.
2. Follow Procedures
Having cut my teeth in the chemical business, our equipment operators had a procedure or checklist for nearly everything they did. We had procedures on how to start the equipment up, how to shut it down, and how to change products. I was surprised when I went into the consulting business to find out that most companies have very few Standard Operating Procedures (SOP). They instead rely on each operator to start equipment and run products based on memory or experience. If something goes wrong in the process, they eat the loss and then identify it as a training opportunity or learning experience. The reality is that as an Operations Supervisor you need the equipment to run consistently each and every shift and the only way to deliver consistent operations is for two things to be true and consistent. The first is to have SOPs and Operator Checklists. If your department does not have these procedures and checklists in place, now is the time to get it done. The second thing is that your equipment must be reliable. Follow the steps in this blog and you will be on your way to having reliable equipment.
3. Review/Audit Procedures
Now that you have procedures in place, you and your operators need to review and audit them. Reviewing procedures gets people who have experience involved using a continuous improvement model to develop the best procedures. Audits are necessary to ensure the operators are in fact using the SOPs and checklists on a daily basis. Reinforce the people who are using the procedures and those who are actively involved in improving procedures.
4. Know Process Performance Standards
Being new to this job, you may not even know what this means. Process performance standards are things like line rate for a given product, the quality standards you need to maintain for the product (including how it’s packaged), and the health, safety, and environmental standards you are held to in manufacturing that product. Why is this important? As our equipment is in the process of failing, it typically fails to deliver on one or more performance standards before it completely stops. This is known as functional failure. If your packaging machine is supposed to produce 325 packages of good quality product per minute and it is making any amount less than this, it has functionally failed. In understanding your performance standards, you can begin looking for what has failed, or what is in the process of failing before the equipment actually stops. Once the equipment stops, if you have no idea what caused the rate to drop off, you will be left to guess on what needs to be repaired. Performance standards when properly maintained allow us to effectively plan and schedule both production and maintenance activities.
5. Understand Equipment Criticality (Logic-Based Decisions)
As I stated earlier, you will be making decisions that will impact the product you make and the customers who use that product. As a result, you need to make sound, logic-based decisions and these decisions become much easier if you understand the criticality of your assets. While this exercise is often driven and seen as a maintenance tool, it is in fact a tool everyone at your company can use to help make sound decisions if done properly. Two pieces of advice here: if your company has not performed an asset criticality assessment, you need to get that started right away; if they have performed one in the past, take a random sample of 100 assets, chart the criticality ranking of each, and make sure the distribution is also random. If the data is normal, left or right skewed, the assessment was flawed and needs to be done again.
6. Be Customer/Product Focused
Reliability is a broad subject, but when it comes down to it, our customers help us to define reliability. Customers set product demand and product demand sets our desired performance standards for both rate and quality. Your job, simply put, is to make high quality products and meet customer demand. But, using thirty years of experience, I can tell you that you will be insulated from your customer and the feedback you get from them will be second or third hand. If you want your process to run in a smooth and reliable fashion, YOU need to know your customers. Just one example I can share comes from a site I visited last year. They had just finished a 6-day, 100,000 piece order of good quality product; however, the problem was that the product was not packaged correctly on the pallets and it all had to be taken apart and restacked. This took 5 full days to complete and the customer’s order was late. Had the Operations Supervisors known the customer, they would have also known how the customer wanted the order stacked.
7. Reinforce the Right Behaviors
This is where learning how to lead people comes into play. I can also tell you that in your very first week, you will be confronted with some problems you’ll have no idea how to resolve. Do yourself a favor and read Performance Management: Changing Behavior that Drives Organizational Effectiveness, by Aubrey C. Daniels and James E. Daniels, and start using their methods of leadership. Positive Reinforcement, Punishment, Extinction, and Negative Reinforcement all have their place; your job is to know which consequence to use and when. At first glance, this may seem like a huge undertaking. In reality, it’s like any other learned behavior; it takes time and practice, but I can tell you with confidence that it works!
8. Learn/Understand PdM
Yes, as an Operations Supervisor you need to learn and understand a handful of predictive technologies, including Airborne Ultrasound, Infrared Thermography, Vibration Analysis, and Lubrication Analysis. If you fail to understand the technologies and how they are applied to detect potential failures, you will make emotional decisions instead of fact-based decisions. While this might be the most difficult undertaking of the items on this list, have faith that having this skill set on your resume will go a long way regardless of the career path you decide to take.
9. RCA – Learn It, Set Triggers, and Implement
Root Cause Analysis (RCA) should be the Operations Supervisor’s best friend. A good RCA process is going to help you eliminate failures in every aspect of your business. When I say learn Root Cause Analysis, what I mean is that you need to learn what works for you and use it. There are a variety of problem solving tools out there, from Ishikawa Diagrams to Cause Mapping; the trick here is to have a group of people who have learned each and specialize in at least one. Once you and your people have been trained, it’s time to set triggers for when you need to perform an RCA, and once you have begun performing them, you need to implement the mitigating tasks. An important thing to remember, rarely is there one “Root Cause”; realistically, there are often several. As a result, remember to save your information just in case the problem comes back. As someone who has made a living at helping people and companies solve problems, the best facilitators don’t tell you what they think your problems are, they instead teach you how to identify and eliminate them. When you find a great instructor or facilitator, insist that they instruct and facilitate all critical RCAs.
10. Keep It Clean
If I can make a general statement, clean equipment is more reliable than dirty equipment. I see it every day and have countless examples of how dirt, dust, and clutter have a detrimental impact on the reliability of manufacturing equipment. As an Operations Supervisor, you will set the bar for what clean means. If you set it too low, you should expect a greater number of random and wear-based failures. Set it too high and you may sacrifice some time where the equipment could have been making product. The trick here is to do as much as you can in about 20 minutes, and write an SOP for the cleanup required in each area. There are some great tools out there for developing good cleaning practices, including Operator Care, Total Productive Maintenance (TPM), 5S, and Kaizen. Take your pick and get it done!
So there you have it! Congratulations on becoming an Operations Supervisor. Some of the best CEOs in the world started their career with this critical step, and well, some of the worst CEOs must have skipped it all together because this position, regardless of what others might say, impacts company performance more than any other. Time to step up and lead!
Leave a Reply