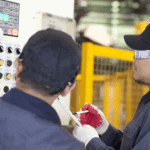
20 years ago, I began my first assignment as a Reliability Engineer at Eastman Kodak’s Photo Chemical facility in Rochester, New York. Now, I understand that I just lost several people who began reading this article by using the words “photo” and “chemical” in the same sentence, but 20 years ago, most photography was still a chemical process.
When I started in this job, the position of Reliability Engineer was a new thing to our company. As a result, I got little direction regarding what a Reliability Engineer should or could do to improve reliability in the area I was assigned. 20 years later, I would like to share a list of the 10 things any Reliability Engineer can do to improve reliability at their site.
- Learn and Begin Facilitating Root Cause Analysis (RCA) – RCA is the go-to tool for any company dealing with a high level of emergency or demand maintenance. The first problem you will encounter when getting the process started is that people will want to do an RCA on everything! Take a step back and remember all the different ways you have learned to solve problems. Each tool requires a different amount of effort and each is designed to solve specific types of problems. Remember, no one tool will work for everything, but it’s a good idea to select a few that work; one for critical/high consequence failures, one for less critical failures, and one for incidents and accidents. Once you have identified your tools, work with your Managers to set triggers for performing RCA. Remember, we can’t spend all day every day working on RCA, so be sure to set realistic triggers. When you’re just starting, one RCA a week is a good target; any more than that and you risk overwhelming the process. A quick tip: you can’t, and may not even be the best person to, facilitate every RCA. People who are good at troubleshooting, who have proven they can lead a meeting, and who enjoy working in teams make great facilitators. Get to know your area’s top Maintenance Technicians and Operators and draw from this group to train facilitators.
- Collect Data to Calculate OEE on Critical Assets – Identifying Speed, Quality, and Operational Losses – It’s getting so that Overall Equipment Effectiveness (OEE) has earned a bad name with some companies in the last 5 years. The problem is that they wanted to measure OEE for an entire plant site and the tool was never intended to do that. As a result, Managers were looking at one number and wondering what on earth they could do to impact that number. The reality is that Seiichi Nakajima designed OEE to measure the reliability of a specific asset or piece of equipment, and as time went on others made the decision to use it to measure for entire departments and even plant sites. The fact is that OEE can be a very useful tool. When used in the correct way, the measure will help you identify and eliminate key manufacturing losses. The best read and uses for OEE and Total Effective Equipment Performance (TEEP) is Robert Hansen’s book, Overall Equipment Effectiveness
By the way, should you ever have the desire to measure the reliability of your plant or a specific site, the correct tool to use would be Reliability Process Plots – a technique that uses Weibull statistics to determine the opportunity available that results from your equipment or process not being reliable.
- Assess and Understand the Maturity of the Company’s Reliability Effort – I think today you will find more pretenders in the world of maintenance and reliability than ever before and one of your first major challenges will be to determine who understands what needs to be done, and who would like you to believe they understand. Start with a simple internal self-assessment using our Reliability Maturity Matrix; this should give you a good idea of two or three things you can hit the ground running with. Use the same assessment as a communications tool with your Managers, showing them that this is where we currently are and here are the things we are going to work on in the first quarter, second quarter, and so on. Some sound advice, if the average OEE for your critical assets is below 80% and one of your Managers thinks you need to be doing more Weibull analysis, you found your first pretender. Start simple by working with the maintenance and operations folks to identify and eliminate losses.
- Become a Certified RCM Blitz™ Facilitator – A little bit of self-promotion here, but if you are looking for a quick win where you can show sustained progress, there is nothing more effective than RCM Blitz™. The trick to Reliability Centered Maintenance (RCM) is to know where to apply the tool, and if you have completed an asset criticality analysis and have been tracking the OEE of the top 20% of your critical assets, then this decision will be easy. Perform an RCM analysis on any critical asset that is suffering from equipment-based, operational, speed, or quality losses. When you have completed the analysis, begin implementing the mitigating tasks immediately and within 3 months you should see a marked difference in the reliability of that critical asset!
- Develop a Bad Actors List from CMMS Data – This is a great way to feed your RCA program and it will help you to build a sound relationship with your maintenance and operations people. Don’t be surprised if a handful of Maintenance Technicians make the statement that this is the first time they have ever seen anyone use the CMMS for something other than entering time and ordering parts. Work to set up small 2 or 3-people teams, consisting of an Operator and a couple of Maintenance Technicians, to tackle the first handful of items on the list. Charge them with using a formal RCA tool that defines the problem, identifies potential causes, and then uses evidence to prove or disprove each potential cause. The best thing you can do as a Reliability Engineer is to help transform the Maintenance Technicians and Operators into proactive problem solvers. Don’t spend every working hour attending their meetings, but instead have them communicate their work as they meet to resolve these problems. Once they have knocked the first five off of the list, make a new list and start all over again. You will be amazed at how quickly this process builds pride and confidence and how what they learn in resolving these problems will begin to apply to other aspects of their work!
- Work with Maintenance Technicians to Identify and Resolve Rotating Equipment Issues – Very similar to item number 5, the difference here, however, is that I hope your rotating equipment doesn’t end up at the top of your bad actors list. If it does, well, you have your work cut out for you! The reason I want my Reliability Engineer working with the Maintenance Technicians to resolve rotating equipment issues is that while they may not be on the top of a bad actors list, rotating equipment failures typically result in secondary equipment damage as well has a high level of unnecessary expense. This is also the place to begin the application and reinforcement of precision maintenance techniques. While precision alignment tools have been around for ages, you may find that the Maintenance Technicians have never been given the time to use these techniques to ensure reliability at the time the equipment failed. You job is to help ensure that they get the correct amount of time and to show them the difference in vibration between a precision-aligned asset and one that has not been aligned. While many people talk a good game here, I want you to show them real vibration data and that with our PdM tools we can tell if the equipment was properly aligned the day it was installed. I can state with a high level of confidence that every Maintenance Technician I ever worked with in this way changed how they went about doing business, and that change made a HUGE difference.
- Become at Least Level 1 Certified in 4 Major Predictive Maintenance (PdM) Technologies – Yikes! This one might scare some people away, but knowing what I do today, I would not hire a Reliability Engineer who didn’t understand the major PdM technologies. The fact here is that if you want reliable manufacturing equipment, PdM has to be a major part of your maintenance strategy, and as a Reliability Engineer, you need to know how each technology works as well as where each technology might apply.
- Lubrication, Lubrication, Lubrication! – I can just about guarantee the lubrication program you walk into will be a mess and were I starting over today in my first weeks as a Reliability Engineer, I would have started right here. The problem is that the revamp of a lubrication program is going to take some money, and it’s going to take some time to get one or two of your maintenance folks through the Maintenance Lubrication Technician (MLT) certification program and the money will come into play because you need to build a lubrication storage area that is clean and organized. So, my advice is to work on some of the quick wins first and build some “Political Capital” before requesting a large spend.
- Form a Team and Review Maintenance Procedures – Is the teamwork theme behind several of these recommendations beginning to sink in yet? Your effectiveness as a Reliability Engineer will be multiplied if you learn how to teach, delegate, lead, and reinforce. Remember, you will only sustain your gains in reliability if you become disciplined enough to develop strong maintenance procedures and job plans. To do this, the Reliability Engineer will need work hand-in-hand with the Maintenance Technicians to review and update procedures and job plans. Expect to find the words “check” and “inspect” a lot. Replace these words with measures, go-no/go limits, and clearly qualitative descriptions, such as “inspect the electrical door gasket for evidence of cracking; the door gasket should be pliable to the touch of a finger.” You can also expect the reviewing and rewriting of procedures to be an undertaking that nobody wants to be involved with, so it will take all of the leadership skills you can muster. Start with job plans and procedures for the most critical assets and work your way down the list. Begin the process by reviewing two a week and add another to the goal each month until you’re knocking off one a day and by the end of your first year, you will have completed a task that others believed would never get done!
- Attend Conferences and Become Involved in SMRP – The world of Reliability Engineering in a manufacturing environment continues to grow and evolve over time and the only way you will ever keep up on what’s new is to start attending conferences and become involved in the Society of Maintenance and Reliability Professionals (SMRP). SMRP was started by one of my old Kodak Managers back in the 1990’s with the intent of forming an organization where maintenance and reliability professionals could exchange information through a structured network. What started out as 20 original members representing 18 companies has grown to nearly 3,000 members from over 200 companies. SMRP is a great organization for learning and sharing, especially for someone new to the business. Outside of SMRP, the conference that should not be missed would be the International Maintenance Conference (IMC), usually held in early December. IMC is by far the best conference for learning and keeping up-to-date on what’s new in the field.
With this list complete, you now have some work to do. My last piece of advice is one I give to the RCM Blitz™ facilitators I train, mentor, and certify: in your career, you will meet hundreds of people who will look you in the eye and say things like “this company will never change”. It is then that you need to remember what I say. I don’t intend to change your entire company, I just want to start with this one asset or system and if we do what we said we needed to do in performing this analysis and the process works, we will move on to the next item. Change comes only when we learn, when we apply what we have learned, and when we then prove how that application was a success! Time to drive some change!
Leave a Reply