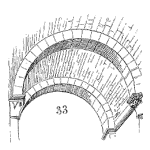
When a product or asset works as it’s expected for as long or longer than expected, we often consider it reliable.
Consumers around the world look for reliable products and services. Some will pay a premium with the desire to obtain failure free value from the purchase. When designing a product or service we often want to create the most reliable item within the constraints of time, resources, and cost. Designers and engineers may add margin or safety factors into calculations and decisions to avoid failures.
Many of us have heard that fixing a design is orders of magnitude less expensive early the product lifecycle. Product recalled or major failures can damage profits and brand image.
Here are three ways you can invest in improving product reliability.
1. Invest in a common reliability language
As Wayne Nelson said at a 2012 reliability conference, “The words we use matter.”
The goals, metrics, specifications, and any other way we write or speak about reliability should be clear. Anyone that knows me, knows I do not like MTBF or MTTF or the related ‘MTxx’ terms.
They are often misunderstood and often misused. The lack of thinking about what the term means and how and when to use MTBF type terms continues to muddle a common understanding of reliability.
Be clear, ask questions, challenge assumptions, and create a common understanding around reliability.
If the desire is to create a product that should work without failure for five years in an office environment. Say it that way and include a note on how many (or percentage) should work for the five years. If you want 999 our of every 1,000 units to operate for five years, say you want 99.9% probability of surviving (not failing) over five years of use in an office environment.
Simply being clear with your customers and your organization enables a clear conversation about reliability. Avoid the simple mistakes the lack of clarity brings.
2. Invest in making decisions considering reliability
I started my working career in industry as a shift supervisor on a manufacturing floor. I quickly realized that we in manufacturing could only make a product worse than the design.
We had variation in materials, equipment, and technique that would combine to create a product similar to the design, yet never with perfectly pure materials, ever precise equipment and flawless execution of assembly procedures.
Thus it is my contention, anything wrong with a product was the design’s fault.
Design engineers working on a product design have the functions to consider. They also know the product has to work with specific loads, stresses, and environmental conditions. They also know about time and cost limitations to complete the design.
Design engineers are reminded about recyclability, ease of manufacturing, testability, repairability, aesthetics, weight limitations, transportation and installation, customer experience, human factors, safety, and dozens of other ‘things to consider’ in the design process.
Reliability may well get lost from the decision making process.
How do we help?
We can help by quantifying the value of reliability. What is the cost of a product failure? What is the cost of warranty per product shipped? This assists the design decisions without overlooking cost considerations.
We can help by making it easy for designers to have the information they need about materials, components, assembly processes and customer expectation related to reliability.
To influence the point of decision, both awareness and information have to be present. Find what is important to the design and show how a reliable product supports that goal (if it’s not reliability). Provide the information and knowledge to understand the information about reliability.
Permit the design team to make informed decisions.
3. Invest in learning from failures
Failures happen.
We can ignore them and hope they go away or stop occuring. Or we can learn from failures. Failure analysis and root cause analysis are common terms when trying to learn what specifically lead to the failure and why the failure occured.The idea that when we understand the failure we can create a remedy to avoid future similar failures.
This learning from failures can and often does occur throughout the product lifecycle.
Failure theories
One theory about design and failures content that every design has a finite number of errors that lead to premature failure. Find and fix all of those errors and the design will be reliable.
Another theory is everything will fail and it’s race amoung the many possible failure mechanisms. The idea here is to identify the failure mechansims the lead to an unacceptablely short lifetime and design them out of the product. By finding and fixing the first to occur failures the product becomes more reliable.
In either case we need to find failures to fix them.
We can, and some organizations do, wait for customers to find the failures for us. We then can improve the product and reduce failures that occur in the hands of customers.
Or we can work to find the failure during the development of the product.
Testing to failure is unfortunately still relatively rare in my experience. We are told failure are indications of poor design. That failures beyond the specifications are irrelevant. That failures are too expensive.
Nonesense.
The best way to learn about the limits and faults of a design is to find failures. We can work to understand the failure mechanisms and design a way to avoid or mitigate the problem.
The absence of failures during the design process doesn’t mean the customer won’t have failures.
Summary
With a little investment in clear language, decision support and finding failures we can create reliability products. In some organizations this may be a major undertaking, in most it will be sublte shift in focus.
The investment will certainly pay off.
Tell me about your investments in reliability. What is working and what is making a difference?
Related:
Leave a Reply