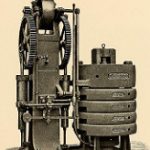
MTBF use and thinking is still rampant. It affects how our peers and colleagues approach solving problems.
There is a full range of problems that come from using MTBF, yet how do you spot the signs of MTBF thinking even when MTBF is not mentioned? Let’s explore the approaches that you can use to ferret out MTBF thinking and move your organization toward making informed decisions concerning reliability.
Ask, ‘What do you really want?’
Really, it is just that simple: Ask what it is about durability or how long the item should work or something similar. If someone asks for MTBF, they are often interested in the probability of failure over some duration within some set of conditions.
Asking for MTBF provides an inverse of the average failure rate – not at all what they may really have wanted to know.
If they really want the average inverse failure rate, ask them why? What decision are they going to make using that information? Is knowing MTBF the right information to inform the pending decision? If not, and MTBF, as you know, is not generally informative at all, suggest using reliability (probability of failure over a time period).
Suppose the person insists that MTBF is reliability and that is what they want. In that case, that is a sure sign they don’t know the difference between reliability and MTBF and how it may impact their ability to make informed decisions.
Analyze the Data Two Ways
For those customers who insist on using MTBF, show them MTBF and reliability data (maybe a life data distribution curve such as a Weibull cumulative density function (CDF)). Show how, using the better information, they can make better decisions.
Show how the conclusion of a simple question, like the results of a life test using MTBF, differs from a time-to-failure analysis using Weibull (or the appropriate distribution). Show how analyzing the data using a two-parameter model permits including the information about the changing failure over time.
I have found that long-time MTBF users realize the benefits of using a Weibull CDF plot.
Focus on Failure Mechanisms
My favorite situation concerning a request for MTBF is for something like a fan or bearings. Simply ask how they expect the fan to fail. The common and often correct response is ‘wear out.’ Wearout is not well described by MTBF.
By shifting the focus from MTBF to the failure mechanism, we naturally shift the discussion to the nature of the failure rate change over time. MTBF masks or obscures such information. By shifting the focus we prompt the MTBF fan to ask and expect better answers.
Early life failures are defined as those that only a failure rate decline in time. They don’t have to, wear out can occur in short order for poorly designed and/or assembled products.
Wear-out failures are characterized by an increasing failure rate over time. The onset of increased failure, an unwanted noticeable increase, may occur at any point. We often want to know that the marked increase in the failure rate occurs at some point in time well beyond when most customers will still be using the product.
Summary
When you hear someone request, talk about, or use MTBF; lash out, ask questions, prod them to think. Shake their language and understanding so they get the information they actually need to make better decisions.
If someone is using the ‘constant failure rate’ assumptions, likewise ask a few questions and provide comparative analysis using and not using the assumption.
I suggest that we simply do not accept the use of MTBF and related thinking by those around us. Oh, and don’t use it ourselves despite how ‘easy.’
Leave a Reply