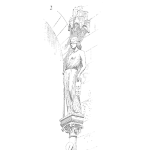
By Guest Blogger Wesley Suplit, product manager, SDMyers
After my first year in college, I discovered my favorite curriculum – economics. This surprises my friends and family because that discipline is known for its dry content and difficult math concepts. However, I had a completely different and inspiring experience. The course, and, really, my professor, opened my eyes to the beauty of observing how people make decisions.
What rocked my world was how simple economics could be. Conclusions could be inferred simply by observing phenomena and then performing thought experiments related to the observations. The goal of a thought experiment is to explore the potential consequences of the principle in question. Surprisingly, no mathematical formulas or complex equations were needed.
In the same way, we can understand a simple approach to online monitoring applied to our electrical equipment by asking relatively simple questions. It can be helpful to use formulas and industry-standard references, but often this hinders us by making the simple more complex; so, let’s walk through a simplified approach:
1. Transformer Monitoring Project Purpose: Determine the purpose of the project and the connection to the organizational aim. What is the purpose of transformer monitoring, and how does it connect to our organizational aim? This question will be answered in a different way for each organization, but it begins with an understanding that transformers are complex pieces of equipment with multiple and varied failure modes and that every organization needs reliable electric power. An answer to this question will provide the “why” behind the project and fuel motivation to work through the challenges.
2. Transformer Fleet Assessment: After answering “Why?” we can move to understanding our unique transformer needs. The fleet assessment can act more as an asset description repository, or it can be an asset management tool used to answer operational questions and influence capital requests. Below are a few questions to ask yourself:
- What transformers are in our fleet, and what are the transformers responsible for operating?
- If the transformer unexpectedly fails, what are the direct and downstream impacts?
- Cost of a replacement unit
- Lead time on manufacturing, shipping and installation
- Environmental impact of failure
- Based on the questions above, what are the highest/lowest criticality transformers in our organization? Or, in other words, which electrical equipment is so important that without it our organization ceases to fulfill its mission and aim?
The outcome of the fleet assessment is an up-to-date list of all the transformers, as well as a ranking of their criticality. At SDMyers, we keep it simple by using three categories: Mission Critical, Systems Critical and Non-Critical. But for the purposes of implementing an online monitoring program, it is important to rank each transformer sequentially, starting with the number one most critical transformer and ending with the nth most critical transformer. This will help with resource allocation in the future.
3. Organizational Transformer Knowledge Assessment: Organizations have a wide variety of organizational knowledge related to the electric power system, which includes the transformer. Rarely is there both deep understanding of the transformer from building materials to end of life. There may be a few SMEs within your organization, however, who could offer valuable insight on design, operations, monitoring, and maintenance of these assets. Include these SMEs on your project and determine what level of support they will offer on an ongoing basis.
Once you understand the organizational knowledge and the level of the SME’s ongoing involvement for your project, you can better plan for the support you will need from a contractor or industry professional. This support can range from complete turn-key service to help with equipment selection and logistics.
After this step, you should have a list of your trusted experts. Who is on speed dial in your phone if you have a transformer question? Who do you call when you have an alarm condition for rate of change (ROC) for
methane?
4. Monitoring Technology Assessment: There are multiple technologies to consider in your transformer monitoring project. For brevity, I will not list the technologies nor the pros and cons, however, each monitor does have benefits and limitations. This is okay. In fact, this can be beneficial to you, as you want to procure the best-fit solution, not necessarily the equipment with the most features.
Consider the following questions as you complete your monitoring technology assessment:
• Does this monitor measure parameters that directly correlate to failure modes I wish to decrease?
• Does this monitor have a proven track record in the industry? Is its prevalence increasing or decreasing?
• Does this monitor require regular maintenance? What are the costs associated with maintenance?
• What are the operating conditions, and will there be limitations in my environment?
• What are the supported communications and how does data get stored and analyzed?
• Will the monitor allow for future upgrades?
There are, of course, more questions to ask when selecting a monitor, but this will get you well on your way toward reliability. Transformer monitoring is complex, but it does not need to be confusing. By asking simple questions (sometimes in the presence of SMEs) you can arrive at a long-term solution that can add to the reliability of your electric power system and overall value to your organization. Transformer monitoring should be directly related to realizing the mission and aim of your organization and improving the reliable life of the transformer.
If you need more assistance, don’t hesitate to reach out to a transformer specialist at SDMyers.
Leave a Reply