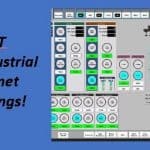
In continuing this year’s theme regarding common questions on relevant topics, today I have the 5 most common questions people have been asking me about the Industrial Internet of Things. Like every other article or Blog I have posted in the past I encourage you to all to jump into the conversation by asking questions or providing comments to my questions and answers.
1. What is the Industrial Internet of Things?
People have been asking me this question at least once a week for the last year or two. Simply put, the IIoT is the inter-networking of physical devices that allows for the collection of data and exchange of information from connected field devices (Valves, Drives, Flowmeters, Instruments, Sensors, Actuators) to a platform designed to analyze data and make sound decisions based on that data.
2. Is this the IIoT something new?
I wouldn’t say this is new, I think a more accurate answer would be to say it is a growing movement that is getting a lot of attention. The ability to make sound decisions based on data from field devices has been around for as long as we have had the ability to control our equipment with PLC’s (Programable Logic Controllers) and DCS’s (Distributed Control System). Those who took the time to understand their equipment have been using data from field devices to build things like trends or comparison trend alarms for years. As an example, one could build a comparison trend for pump pressure and pump flow to determine the condition of a pump impeller. Take that thought process a step further and we could add the position of the flow control valve to the equation and make decisions based on the valve position, flow rate and pressure. Thirty years ago, those who took the time to build this type of logic into their controls called this Process Verification.
3. If this isn’t new, they why are people so excited about IIoT?
Years ago the PLC’s were much more limited in terms of speed and memory. Today this is no longer an issue. In fact, in many cases a plant will have multiple machines each being controlled by a separate PLC’s that feed information/data to other systems for accounting, inventory control, or quality. Add to this we may be collecting data for Vibration Analysis, Airborne Ultrasound or Lubrication Analysis, could this information be combined with information/data from other field instruments or process data? (run time, equipment cycles, ambient temperature) Now take into consideration the information in your CMMS. How often does a component fail? How many cycles were achieved between failures? What was the pressure, temperature, or flow at the time of each failure? If the information in our CMMS is good and we can compare that information to process information, what motors, valves or gearboxes have the best reliability at our site? Today, we have the ability to look at an unlimited number of data from multiple systems and components. With this information the possibilities are nearly endless when it comes to using data to make better decisions to improve our processes.
4. Is there any downside to IIot?
Yes, of course. Like anything else that has come along in the field of Asset Management/Equipment Reliability/Manufacturing Reliability, if you don’t have the right people, structure and discipline in place, one could spend an enormous amount of money investing in what many are touting as the greatest thing ever and end up with little or no improvement.
5. How could that happen?
It starts with the basics, if you’re engineers didn’t design a system to pump liquid properly all the maintenance in the world won’t make it run properly. I could collect data from 10 devices for years and all that information will tell me is the pump is about to fail again. Now, let’s say the engineer designs the system properly and the trades people don’t install it properly. You’re right back in the same boat! If we don’t operate it properly, if the environment we are trying to operate in changes, if we take vibration reading from different locations… While we have all this equipment and technology to help us make better decisions to get more from our equipment, humans are still ultimately in control! For years we have been able to take vibration readings on rotating equipment and with a very high degree of certainty detect a bearing is in the process of failing yet someone can and often will make the decision to continue to run. A number of disciplines must be in place in order for this to be effective. Educating ourselves, and committing to working in that direction comes first.
Doug Plucknette, World-Wide RCM Discipline Leader at Allied Reliability Group is a Reliability Engineering Consultant and Published Author of “Reliability Centered Maintenance using RCM Blitz™ and Clean, Green and Reliable. Having created the RCM Blitz™ Methodology he has been an RCM Practitioner and Trainer for over 20 years. Doug resides in Spencerport, NY and can be reached at plucknetted@alliedreliability.com
Leave a Reply