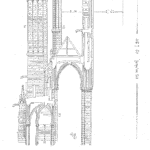
A specific reliability plan may include any number of specific tasks. To build an effective plan you need the knowledge of the individual tools and techniques, plus how they may fit together to create an overall plan to achieve your goals.
Reliability Goals
Of course, this starts with establishing complete reliability goals that include function, environment characterization, probability of success (reliability) and duration.
I recommend setting specific goals for setup/installation (early life), the warranty period and the expected customer use period.
For example, for an inkjet printer the goals may be stated as a device that prints b/w or color (reference engineering specification document for other functional details), in the home or office environment (reference environmental and use characterization documents for details), with:
- 99% probability of successfully operating without failure for the first month after purchase,
- 95% probability of successfully operating without failure for first year (warranty),
- 90% probability of successfully operating without failure for 5 years (use life).
Make the goal clear, complete and connect to your business objective and customer expectations.
Reliability Modeling
Create a reliability model (reliability block diagram will work well here) that includes the breakdown of the reliability goals to the major elements of the system. For example, for a desktop computer, including display, motherboard, power supply, etc. Consider the internal temperature for the motherboard is higher than for the ambient.
Be sure the math works out so if each element meets their reliability goal the system meets the overall goal, too.
Reliability Estimates (not parts count predictions)
Estimate reliability of each element of the model — and compare/adjust the goals to still achieve the overall goal. Compare the power supply, motherboard, and other elements reliability performance to the goal and roll up to system goal expected performance including a breakdown of what failures to expect and when. Use engineering judgment, vendor data, literature, field data, and internal life testing to create suitable estimates to populate the model.
Identify large areas os poor or uncertain estimates and take steps to get better life estimates, also identify areas that do not meet budgeted target and evaluate options that still achieve the objective.
Track Progress
Track reliability issues any defect, bug, or prototype failure, that would have caused a system failure impacting the use of the system by the customer.
Track date/time of arrival of the issue and plot using mean cumulative function or reliability growth models (plot count of failures (Y) vs time (X) – look for the rate of arrival to taper off as the design mature. This requires actually fixing the issues as testing continues.
This shows progress resolving issues and if the team is finding and solving enough issues fast enough.
Write the Reliability Case
Create a white paper or report that details the rationale for expected reliability performance. It should include the goal, model, and evidence supporting reliability estimates. It should also include what is known, unknown (or not well known) and degree of risk to reliability performance.
—
The intent of a reliability plan is to support decision making across the team and by management as you work to achieve a product that meets you customer’s reliability expectations.
Related:
How to Assess Your Reliability Program (article)
Purpose of a Reliability Program (article)
I think that of equal importance in a Reliability Plan may be:
– Who does What and When (people involved).
– Selection of components and their application (derating?).
– Reliability requirements on subcontractors, if any.
– FMEAs.
– Who, When and How is Reliability Testing performed (verification, validation, demonstration, life testing?).