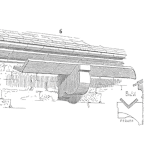
What if you knew all the possible outcomes for your product’s reliability performance due to component variations, for example? What if you knew the future with enough certainty to make a difference?
Building on brainstorming, what-if analysis involved using models or prototypes that allow you to change something and see how it alters the output or performance. What if we change this support bracket from iron to aluminum? What if we swap out this 100 ohm resistor for a 200 ohm one?
As a curious engineer you could spend many, many hours conducting what-if based experiments, so there is a bit more to this idea then just a random walk of changes.
The Basic What-if Process
The fundamental element of this type of analysis is to consider what will happen if an input, material, component, or some aspect of the system or design is different. This is setting up an experimental hypothesis.
What will happen if we change x to the output y? Right it down. Be clear about what you are changing and what you expect to happen.
Then do it. Observe the change. What the change in the output as you expected? Or did you learn something by a surprising result?
That’s it.
You can use simulations, formulas, early prototypes, etc. What you change is really only limited by your imagination. Which is a problem if you have an active imagination.
To focus the analysis, consider the prior work such as FMEAs to identify the areas that have the highest risk, are not well understood, or may lead to significant consequences. Conduct the what-if analysis on those areas that require exploration or verification.
These are one variable at a time experiments. As such they are not very efficient when there are many factors or interactions between factors that impact the results. For more complex issues use the set of design of experiments (DOE) tools.
Where is this useful?
The use of what-if analysis is useful over a range of situations. For me, when examining an equation or formula I often ‘play with’ the various variables to see what the effect on the resulting calculations. While some folks can quickly grasp how an exponent within an equation affects the results, I often need to set up a few experiments and run out the calculations to see it for myself.
When making assumptions for use in an equation, sample size calculation, within a regression model, or nearly any situation with the need for assumptions, this analysis allows us to quickly determine how important the assumed value is to the results. Input a range of assumed values, determine how it affects the results. I learned early on that assuming an activation energy within the Arrhenius equation has a dramatic affect on the calculations and it’s best to work a bit extra to determine and use an accurate activation energy instead of just making an assumption.
When setting a model or simulation of a complex system, does the model behave as expected when inputs are altered compared to your prior experience or engineering judgement. A quick test allows you to either adjust your model or expectations (if the model is an accurate reflection of reality.)
Early prototypes lend themselves to what-if analysis. In some cases, the prototype becomes a test bed to check tolerances, vendor differences for select materials or parts, etc. Early in my career the development team custom ordered integrated circuits with high and low clock rates as a means to determine the impact of the expected variation on system performance reliant on circuit timing.
For processes such as manufacturing lines, maintenance practices, supplier audits, etc. A what-if analysis approach may lead to ongoing experiments that may lead to process improvements or the identification of critical elements of the process to keep in place.
As much as anything, the what-if process is a way to view the world. How can we make our design, system, process, etc. just a bit better with a change? Structuring your ideas or insights allows you to put into motion a simple method to explore, learn, and improve.
Leave a Reply