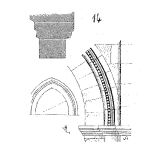
In the last Article, we learned how to work with predictive models to find solutions that solve for desired responses. We used some basic algebra to solve for solutions and looked at the use of contour plots to quickly visualize many solutions at a glance.
In this article, we further explore the use of contour plots and other tools to help us quickly find solutions to our models. We start by revisiting the battery life DOE example that was discussed in the previous article. The statistical output below shows the coded model that contains only the statistically significant (main and interaction) effects.
We can easily produce the main and interaction effect plots that helps us to interpret the significant effects.
Overall, as both wall thickness and temperature increase, the battery life decreases. However, the interaction plot shows us that temperature only affects battery life for Nickel batteries. When Lithium is used, temperature has no effect on the response. Most DOE software can generate contour plots for the responses. Below is a contour plot for this model from Minitab software.
Since there are three significant factors in the model, we must hold one fixed. We have held the material type as Lithium. This type of contour plot shows regions of responses that fall within a range. The blue area on the far right are predicted battery lives between 44 and 45. It should not be surprising that the contour regions are vertical rectangles since we already know that changes in temperature will not affect the battery life when we are using lithium as the material.
Below is a contour plot with the same factors when we hold material type as Nickel.
Now, both temperature and wall thickness affect the battery life.
To zero in on an exact solution, we can switch to showing contour lines instead of regions. Again, with Material Type = Lithium, we have:
Thus, as we found algebraically previously, we can graphically find the value of wall thickness that predicts a response of exactly 45.0, which is 1.44 mm. Not that this is the uncoded value which we can read directly from the plot (recall the coded solution was 0.6).
We can visualize the response surface with a surface plot as shown below. This has the response in the vertical direction. In this model, the response surface is a plane in space. Along the temperature axis, the heigh of the surface is constant (since temperature changes have not impact on the battery life when Lithium is used).
Contour plots are quite helpful for visualizing solutions. However, if the model contains many significant factors, it can still be tedious to hunt for solutions, especially when several factors must be fixed to view a single plot. Most DOE software programs have optimization algorithms that will explore the response surface for the desired responses and provide an “optimal solution”. This is especially useful when we are trying to jointly optimize multiple responses.
Using an optimizer involves specifying the desired (target) response value (or whether it should be maximized or minimized). Also, any specific constraints on the input factors may be specified. Often responses can be prioritized in terms of importance. Finally, it may be possible to specify a factor that quantifies the importance of the response being at a specific target exactly, or simply within a specification range. Once these inputs are specified, the algorithm will hunt for an optimal solution that best mees the criteria specified.
For the battery life DOE, here is some output when we specify a target response of 45.0 and hold material type = Lithium.
We can immediately get the solution that Wall Thickness must be 1.44.
Note that this solution predicts that the average battery life will be 45.0 if we set wall thickness at 1.44.
In the next article, we will look a bit more at the uncertainty in these predictions. We will also, talk about model validation to ensure that technical assumptions that are inherent in this process are satisfied.
Leave a Reply