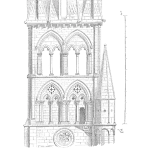
The boiler is the heart of a refinery or power plant. Boiler failures cause forced shutdowns and put the health of the plant at risk.
Some boiler designs run the risk of thermal fatigue failure. During service, the internal waterside surfaces of the tubes form a thin, protective oxide layer. Yet if the strains caused by the combination of (1) thermal expansion and (2) restraint during temperature fluctuations exceed the oxide strain capacity, the oxide cracks. Each thermal cycle will repeatedly crack the oxide, expose fresh metal when then oxidizes, eventually forming a crack. Technically this mode of cracking is corrosion fatigue-driven by thermal cycling. Yet since the boiler water will always be mildly corrosive, for boiler applications this mode of cracking is simply called “thermal fatigue”.

Above is the site of a power plant boiler tube that had failed by thermal fatigue. You can see that the filled boiler tube is welded into a wall plate. The water filled tube and wall plate which change temperatures and expand/contract at different rates during starts/stops/thermal fluctuations. These differences apply thermal strains on the boiler tube. In this example, the thermal straining on the tube had been so great that the tube had stretched and deformed.
Note that the mirrored tube appeared to have been replaced at some point in the past, suggesting a history of failures at this site.

Not all thermal cycles would have been so aggressive as to deform the tube. Tube deformation may have been associated with a TRIP or a particularly rough start/stop. Still, this example makes it easy to visualize that this tube had sustained high thermal strains well above that required to break the brittle, protective oxide layer. Thermal cycling (starts/stops/load changes) and the repeated breaking of the oxide layer had eventually resulted in thermal fatigue cracks. Sites that experienced the highest strains, including restrained sites, formed the biggest thermal fatigue cracks.

The definitive identifier of thermal fatigue cracks is their classic wedge, oxide-filled morphology seen by optical microscopy. Thermal fatigue cracks look like what you’d expect, relatively wide cracks filled with oxide. Each loading cycle would break the oxide at the crack tip, exposing fresh metal which corroded until the next thermal cycle. This forms the wide crack base and the tip, which hasn’t had as long to oxidize, is sharper.

In summary, this forty-year old boiler design was susceptible to high thermal strains. The combination of (1) dissimilar thermal expansion between the tube/wall plate and (2) restraint of the wall plate caused the internal oxide layer to crack during thermal cycling. It provides a good example of how some boiler designs are at risk of thermal fatigue cracks.
For boilers with design risks of thermal fatigue, care during operation can help reduce the formation of thermal cracks. Slowly ramping up and down may help increase the life of the boilers. Inspection at such highly strained sites or sites that have suffered thermal fatigue in the past would also help prevent surprises during operation.
Read the full report, link below. Like the article, share with friends. Want to read more, follow.
Leave a Reply