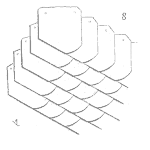
You may have heard of the 80/20 rule. The idea is that 80% of the wealth is held by 20% of the population. As an Italian economist, Vilfredo Pareto made this observation that became generalized as the
Pareto Principle: 80% of outcomes are due to 20% of causes
For field returns, for example, we may surmise that 80% of the failures are due to 20% of the components, for example. This principle helps us to focus our work to reduce field failures by address the vital few causes that lead to the most, or most expensive, failures.
Gather the data
The Pareto Principle applies to observed data. The first step is to find the data. Field return data may be found in customer service, call centers, repair centers, etc depending on your product and organization. In a factory, the CMMS or other system may include a listing of downing events by type of equipment.
What we’re looking for is a count by category. For example, let’s say we recently launched our newest desktop computer the Model X. Over the period of the first month, we received 248 returns for various reasons.
The best data for an example like this is after thorough failure analysis. Be suspect of a listing of just what has been replaced as sometimes many items are replaced in the hope that at least one fixes the problem.
So, we get a list of items within our system the caused the failure. Such as the CPU or Power supply. At this point, we just count how many failures occur for each element of our system.
In this example, we find 128 CPUs, 64 HDD, 32 Power supplies, 16 Keyboards, and 8 Displays. This simple listing of counts is easy to interpret, the CPUs are the biggest source of field failures. In many cases the highest count items is obvious. We are also interested in what makes up the 80% of failures, the vital few 20%.
Create a basic Pareto Chart
The easiest way to create a basic Pareto chart is to simply order the counts from highest to lowest and create a bar chart. Instead of a list or table of numbers, we now have a graphical representation of the data.
From this chart, we can ascertain the relative frequencies of the various field problems. The CPU and HDD appear to be the bulk of the issues.
Enhance your Pareto Chart
There are many ways to prepare a Pareto Chart. A common approach is to include an indication of the cumulative number of counts. One that I like is to include the count value with each bar to make reading the chart easier. Also, it is common to use a relative frequency instead of counts. for the vertical axis.
Each addition either provides a little more information or helps the viewer quickly interpret the chart.
Simple counts of field problems do not include the impact of those failures. Sure the one that occurs the most often is a candidate for improvement, yet what if the fix is quick and has little impact on the customer or your business. Whereas the second type of failure, in our example the HDD, causes the irretrievable loss of data.
An enhancement to Pareto Charts may include weighting the counts in some fashion. By cost of the repair, by severity rating, or by some other meaning factor improves the analysis of the data to focus on the most important causes to address.
Tips on Using these charts
A Pareto Chart is just a representation of your data. Thus, having good data is key.
Always label your charts, and when appropriate include a source of data and timeframe of data.
In the analysis, look for ‘low hanging fruit’, those quick and inexpensive to resolve even if not the most important.
Also, look for grouping so causes that may benefit from a similar resolution. For example, if your data is to component level on the motherboard, and one of the important component failures will entail a layout of the circuit board, then consider including improvements for all the other components that fall lower of the chart.
The last tip is to regularly use this simple tool to communicate where the opportunities lie for improvement. Creating these charts on a weekly or monthly basis, highlighting what has changed, and sparking meaningful discussion for product or system improvement brings value to your organization.
Leave a Reply