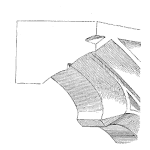
It is well known that chloride stress corrosion cracking (Cl-SCC) of stainless steel is caused by the combination of (1) aqueous chlorides, (2) stress and (3) temperature. Yet even with great awareness, Cl-SCC still manages to sneak up and cause many surprise failures. Here is a failure analysis case study to summarize the key factors causing this corrosion cracking mode.
After twenty years of service, a waste fuel line at a petrochemical facility had leaked at an elbow weld. The 316L stainless steel line had been insulated and steam traced (230°F, 110°C steam). The warm waste product was known to occasionally include hydrochloric acid.
During the postmortem failure investigation, the internal surfaces of the elbow and pipe were found to be riddled with cracks. Optical microscopy and energy dispersive spectroscopy (EDS) diagnosed the cracks as chloride stress corrosion cracks (Cl-SCC).
Although cracking had occurred all throughout the internal surfaces, the largest cracks were located at the highest stressed sites. This example neatly shows that the elevated stresses around the welds and even areas beneath the shoe clamps had increased the severity of cracking.
Although Cl-SCC of austenitic stainless steel is caused by the tirade of aqueous chlorides, temperature and stress, the most relevant factors in this case were the former two. The susceptibility of austenitic stainless steels (304, 316, etc) greatly increases at temperatures above 140°F (>60°C). Hotter than this threshold, even low levels of chloride/chlorine can introduce the risk of Cl-SCC to austenitic stainless.
Although stress is clearly a factor and is listed as a key variable needed to cause SCC, from the practical perspective it is a moot point. If the other conditions for Cl-SCC are present, there will be enough stress somewhere along a welded line to cause cracking.
In summary of this case, the 230°F (110°C) steam traced insulated line carrying warm waste had ample heat to be susceptible to Cl-SCC. The waste was known to occasionally contain hydrochloric acid which was presumed to have been the source of the chlorides. Simply, the combination of temperature and chlorides had caused Cl-SCC cracking throughout. The higher the stresses, the faster the cracking.
The diagnosis of Cl-SCC meant that the entire line was at risk and required replacement. The operator reported that they could not change the waste fuel chemistry and that steam tracing was needed. Had the operator wanted to extend the life of the replacement line, it would have required upgrading the material type. In the end, the operator chose to replace the line with 316L stainless steel again and plan to do so every couple of decades.
Learning From Failure Series – You can learn a lot from failure… but it is way better to learn from someone else’s failures! LFF uses past failure analysis cases to share lessons learned and review practical aspects of common damage modes suffered in the refining and petrochemical industries.
Leave a Reply