Understanding The Difference Between Condition Based Maintenance (CBM) & Predictive Maintenance (PdM)
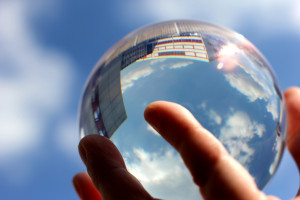
PdM & CBM are in almost every discussion that involves improving plant performance and reducing costs. But what is the difference between the two and when should one be used over the other? This post will address those two questions and a few cautions when using these techniques.
What is CBM?
According the Professional’s Guide to Maintenance & Reliability Terminology, “CBM is the direction of maintenance actions based on indications of asset health as determined from non-invasive measurement of operation and condition indicators. CBM allows preventative and correction actions to be optimized by avoiding traditional calendar or run based maintenance.”
What is PdM?
PdM is an equipment maintenance strategy based on measuring the condition of the equipment to assess whether it will fail during some future period, and then taking appropriate action to avoid the consequence of that failure. The condition of equipment could be measured using condition monitoring, statistical process control, equipment performance, or through the use of the human senses.
Differences Between the CBM & PdM
The two appear similar, but there are differences between the two. I see CBM as corrective activities that are driven by the condition of the equipment. This is a methodology like FTM (fixed time maintenance), or RTF (run to failure).
PdM is the act of gathering indicators and determining when the equipment is expected to fail. These indicators can be vibration signatures, temperature changes, or even process parameters. Once the indicators are gather, analyzed and the failure predicted, then the work management process can trigger a corrective activity. This corrective activity is CBM as the maintenance activity is being driven by the condition of the equipment.
When to Use Which One?
Based on the definitions you would assume that predictive maintenance comes before condition based maintenance. But that is not always the case. Condition based maintenance can be implementing by monitoring simple parameters such as the pressure differential across filters using gauges for filters. Changing filters based on the pressure drop is a simple example of condition based maintenance.
So which one should be used and implemented first? It is simple, what can the maintenance department implement and prove results with quickly. This will create buy in of the program and unlock funding for more CBM & PdM activities.
When Not to Use CBM or PdM
There are times when CBM and PdM will not be effective and will waste valuable time and resources. Although CBM & PdM will improve equipment availability, it will only be effective once certain foundations are in place. The most important foundations are;
- Maintenance Planning & Scheduling will ensure that the work identified with PdM can be scheduled and completed before the equipment fails.
- Spare Parts Management will ensure the right parts are on site in the right quantity at the right time to support the CBM & PdM activities.
- Technician Skills are critical to the success of PdM. If you sent out a technician with a thermography camera, what results will you get? It depends completely on if they have had training. Same goes with vibration, ultrasonic, etc.
- Equipment Strategy must be in place to ensure that the PdM, and CBM are performed on the right equipment and will help to mitigate the consequences of the failure. There is no point in doing PdM and CBM on equipment that will not impact the business in the event of the failure.
Without these foundational elements, it is not possible or cost effective to have a CBM and PdM program. So I must ask, are you attempting to implement or sustain a CBM and PdM program without the foundational elements? Or do you have the foundational elements in place and are successful in CBM and PdM?
Remember, to find success, you must first solve the problem, then achieve the implementation of the solution, and finally sustain winning results.
I’m James Kovacevic
HP RELIABILITY
Solve, Achieve, Sustain
Follow @HPReliability
Leave a Reply