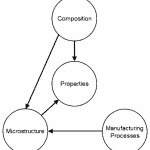
In the previous article I discussed product design in general and the importance of leveraging materials engineering to design components that meet performance and reliability requirements at low cost. Both component form and materials can and should be engineered to optimize a component’s design.
In this article I discuss a component design process that explicitly includes materials engineering considerations. This process involves consideration of all design requirements and cost. Not just designing for reliability. That’s where selecting materials gets tricky – having to consider different sets of requirements and design for ease of component fabrication and joining.
In future articles I’ll focus on reliability. In these first few articles I’ll discuss all considerations, so people understand that reliability is one aspect of selecting and engineering materials for components. Most of you probably already know this, but I just wanted to be sure.
In addition to improving the chances of meeting performance and reliability requirements at low cost, the design process helps reduce unpleasant surprises that cause delays and extra work.
From the reliability perspective, one unpleasant surprise is product failures during testing. Testing failures occur when the materials in a component degrade to the point that the component stops functioning as required. For example, when an electronic housing component corrodes too much during salt spray testing and a leak occurs. Or when a component fractures due to fatigue during vibration testing. If a failure is due to a poor material choice, then the component must be redesigned and the test repeated. This extra work and time can be avoided.
Component design process
The outline of the process is:
- Identify component form and design requirements
- Identify materials selection criteria
- Identify candidate materials
- Evaluate candidate materials
- Select materials
Steps 1 through 4 are often iterative, as mechanical engineers and materials engineers consider options and trade-offs to optimize a component’s design. Sometimes, design discussions to identify candidate materials take only 30 minutes. Other times, for complex components with complex design requirements, discussions might occur over a period of days, weeks, or months.
This process outline is, well, an outline. Many engineering considerations are part of each step. Still, the outline demonstrates how materials engineering fits into the product design process. The strength of the process lies in the ability to…
- Quickly determine whether viable material options exist.
- Identify the risks and benefits associated with the material options. It may be desirable or necessary to consider options that are risky because they provide a competitive advantage.
- Evaluate whether material options do meet performance and reliability requirements in parallel with other product design efforts. The information is used to select the best material from the candidates.
The last point deserves more discussion. Performing materials level reliability testing helps design in reliability and improve the likelihood of meeting or beating design deadlines. The test data provides confidence that certain materials and component designs will pass product level testing and informs design teams about problems with other options, all before product testing occurs.
The remainder of this article discusses each step of the process.
Step 1: Identify component form and design requirements
The process starts with a mechanical engineering stab at a component’s mechanical form – size, shape, and features. Based on the form it is possible to identify the design requirements, which include requirements for …
- Performance
- Reliability
- Mass (when weight is a concern)
- Cost
- Manufacturing and assembly
- Industry standards and government regulations
- Intellectual property, sustainability, …
Performance requirements describe the attributes a component must have to function as required. The attributes are described in terms of mechanical, electromagnetic, thermal, optical, physical, chemical, electrochemical, and cosmetic properties. For example, strength, electrical resistance, thermal conductivity, and luster. Performance requirements include mechanical loads that must be supported, electrical current that must be carried, and cosmetic appearance.
Reliability requirements refer to the conditions to which components are exposed that can cause their degradation and failure. The requirements describe the stressors to which a component will be exposed, the amount of exposure, and the expected response of the component’s materials. Examples of stressors are cyclic stresses, wear, high temperatures, and salt water (corrosion). A component fails if its material degrades to the point where the component no longer functions as required.
Sometimes there are requirements to use specific manufacturing or assembly processes to fabricate and join components. Perhaps a company has manufacturing capabilities that must be used or is familiar and comfortable with component or joints fabricated using certain processes. These requirements limit the materials that can be used because the materials must be compatible with the processes. For example, components to be joined by resistance welding must be made of materials that enable good joints to be formed using that process.
For many products there are industry standards and government regulations that specify component form and/or materials. Intellectual property requirements include avoiding specific physical constructions or uses of materials that are covered by other companies’ patents.
Step 2: Identify materials selection criteria
The materials selection criteria are specific materials properties derived from the component design requirements. For example, for a component that must support a specific load, the minimum yield stress required for the component’s material can be determined. This will be one of the material selection criteria.
Identifying all the materials selection criteria early in the design process is critical to prevent problems later in the design process. Sometimes, no suitable materials can be identified for a component. Redesign is not a problem if this occurs early in the design process. However, it is a problem to learn late in the design process that no materials meet all the design requirements. At this point, the costs and time required to redesign a component’s form at this point are high, and using select a sub-optimum material may be the only option.
Step 3: Identify candidate materials
Use the materials selection criteria to rule out materials that will not satisfy all the materials selection criteria. When evaluating whether a material might be appropriate for the application, be sure to consider the materials’ range of values for the properties of interest. Do not rely upon nominal properties values.
Identifying the design requirements early in the design process is critical to determine whether materials exist that meet the requirements. Trying to select materials based on a subset of requirements is risky – it’s no fun finding late in the design process that a critical component fails during testing. As the number of requirements increases, the options of materials often decreases. Conversely, as the number of requirements increases, opportunities for innovation by engineering form and materials increases.
Step 4: Evaluate candidate materials
There may be candidate materials for which there is not sufficient data available to indicate whether the materials satisfy all the materials selection criteria. These materials will have to be evaluated to determine whether they do meet the selection criteria.
Different types of evaluation are required. One is the metallurgical evaluation of metal stock (e.g. sheet, plate, tube), components, or joints to ensure they meet specifications for properties, composition, microstructure, and type and amount of manufacturing defects. For custom made components such as castings, forgings, and extrusions, obtain samples of components already in production at the supplier.
Another type of evaluation is measuring performance when data does not exist. For example, determining whether a weld joint or adhesive joint between two components will be strong enough. While joint strength can be estimated based on joint geometry and material properties, factors such as weld shape and defects, adhesive adhesion, and effects of adhesive curing process are more difficult to model, and they affect the joint strength. Therefore, it is necessary to build sample joints using the process and materials of interest and test the joint strength.
Another type of evaluation is exposure of materials to simulated use conditions to determine whether the materials can withstand the exposure without degrading to the point that components and joints fail. A method for exposing samples to simulated use conditions must be developed and samples must be fabricated. This approach enables multiple materials to be evaluated without building the entire product and testing it. For example, samples of painted steel plate with bolts in it can be exposed to salt spray tests to evaluate the corrosion resistance of the different paints and bolt metals.
Step 5: Select materials
Select the materials that satisfy all the materials selection criteria at the lowest cost. Cost includes the cost of the material and the cost to fabricate a component or form a joint between components.
Next article
In the next article I’ll provide a real-world example of how the process is applied. After that I’ll get into reliability.
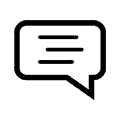
Leave a Reply