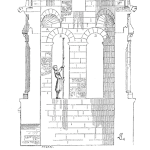
This article outlines key concepts that an organization needs to be aware of to bring about optimal asset health by removing risks and managing their causes. The Plant Wellness Way EAM methodology focuses on the relationship between asset health and business performance. It contains the processes and analysis tools to develop a system-of-reliability that fully supports operating asset health for the greatest ROI from each asset throughout its life cycle.Risk is the total losses suffered when any asset’s components may fail. The causes of failure are the environmental and operating stresses that affect a component’s microstructure. This means that world class reliability is the effective, complete remove of the causes of failure, also known as risks, from your operations.
Figure 1 contains all you need to know in order to bring any operation world class reliability and improved operating profits. It shows the direct connections between the causes of business and operational risks and the reliability of your assets. When you make your assets reliable, and develop systems that support their component health, they will take your company and operations to the heights of operating success and profits.

Source: Thanks to Paul Price, a UK condition monitoring consultant, for use of this concept.
Risk Hierarchy
Every asset failure can be traced back to what was done to its components’ during their lifetime. As shown in Figure 1, there are dependency links between the initial Physics of Failure mechanisms and an organization’s performance. These links run up the hierarchy of risk, with each level relying on multiple links from below. This means that organizations can have countless causes of failure (risks) in their systems and yet still operate and be somewhat profitable. However, the state of health at each level of the hierarchy adds risk and can become a larger problem for the levels above it.
Ultimately, the reliability of every physical asset and the subsequent risks they bring to a business depends on how well you eliminate and prevent the causes of Physics of Failure mechanisms throughout its parts’ life cycles.
Common standard maintenance strategies look only at assets and assembly levels of the dependency hierarchy. As a result, failures are never, truly, prevented. The causes of failure are allowed to continue to affect the microstructure of the component until the damage is so server that is can be detected by the behavior of the asset. If failure mechanisms are present in equipment, they will generate the risk of failure.
Physics of Failure events are the operating stresses and local environment affecting a component’s microstructure. Thing such as healthy lubricant, correct lubricant film thickness, proper interference fit between mating parts, trueness of component shape, fineness of surface finish, subsurface stress levels, adequate load distribution, and so on, all impact the health of a component and it’s reliability.
What makes Plant Wellness Way such an effective system, is the focus is on the removing the causes of failure from occurring to begin with. When there is no risk at the Physics of Failure mechanism level, then you can be sure an asset has the greatest chance of exceptional reliability and the least risk of operating failure.
Removing Physics of Failure Mechanisms
High equipment reliability is within the reach of every business. Reliability is malleable by choosing policies and quality practices at each level of the dependency hierarchy.
At mechanism level, set demanding quality standards for equipment parts so you get outstanding reliability during operation.
At component level, use precision that delivers long service lives to parts and apply only the highest-quality operating and maintenance practices.
At assembly level, use more robust, durable materials for components so that they take greater stresses and don’t degrade.
At the asset level, replace assets early with the newest models rather than wait too long and get numerous failures and lower productivity. Be willing to pay for higher quality equipment so your company can make fortunes from fewer failures.
For the process level, have right knowledge everywhere and only used the right practices, insuring they are done rightly.
At the business level, these requirements need to be incorporated into corporate thinking when you make engineering, asset management, operational or maintenance decisions.
The most beneficial maintenance strategies eliminate Physics of Failure mechanisms and reduce the total risk that a part carries during operation. The lower down the dependency hierarchy that good decisions are made, and precision quality controls installed, the more comprehensive is the risk control strategy.
In PWW the Physics of Failure Reliability Strategy (PoFRS) Analysis is used to select the right engineering design, suppliers, maintenance and operating requirements to most effectively remove causes of failure throughout the dependency hierarchy. It is used for all risks considered unacceptable (Figure 2) to determine what actions should be done to reduce operating risk. PoFRS follows the Stress-to-Process Asset Management Model. Starting with risks to component microstructure and working up the hierarchy, the analysis specifies the strategy, knowledge, skills and practices required in the business and asset life cycle processes to achieve component reliability.
Each mechanism cause of a critical part’s failure is identified and addressed one by one until the part’s lifetime risk control plan is complete. The risk control plan covers all that will be done during the life cycle to remove or significantly reduce operating risk. It lists the mix of design, manufacture, supply chain, operations, and maintenance activities to lower the risk of microstructure destruction and deliver high equipment reliability.

Risk Removal Choices
Plant and equipment reliability are only improved if parts do not fail. By doing Physics of Failure Reliability Strategy Analysis at the component and mechanism levels, you identify the engineering, manufacturing, operational, and maintenance issues that must be addressed at each level of the dependency hierarchy for maximum asset reliability.
The choices available to prevent component failure and subsequent equipment breakdown are –
- Keep total stress well inside the elastic zone everywhere in the microstructure
- Minimize intended fluctuating and cyclic microstructure stresses
- Eliminate unintended fluctuating and cyclic microstructure stresses
- Establish and permanently sustain healthy microstructure contact environments
- Remove microstructure failure causes from throughout the life cycle
- Monitor for the causes of microstructure failure and remove the causes
- Monitor for the onset of microstructure damage and correct the issues
- Replace microstructures before failure
- Change the part’s design to prevent microstructure overstress or degradation
Outstanding reliability is not achieved by maintaining and repairing plants and machinery. It is achieved by creating systems and processes where equipment parts do not fail. This means forming and adhering to asset designs, manufacturing methods, installation techniques, operating practices, and maintenance tasks that remove microstructure failure causes and support ongoing asset component health.
With PWW you have access to an enterprise asset management system methodology that is focused on creating reliability rather than repairing failures. Developed specifically to remove failure causes, the full PWW methodology contains multiple processes and analysis tools to ensure that your operations are optimizing component health, maximizing the chance for assets to function with exceptional reliability, and the slightest risk of failure.
Failure-Focused Maintenance vs Reliability-Creation Paradigm
A failure-focused maintenance paradigm is that of most maintenance strategies. Find the issues and fix them as they develop to a noticeable level. Often, this approach results in assets and their components failing before actions are taken to remedy the issue. Some failure-focused maintenance strategies employ monitoring of key problematic assets or components and performing maintenance on them at a point just before failure.
On the other hand, a reliability-creation paradigm, such as the Plant Wellness Way, is where the focus is on maintaining asset component health. Processes, methods, and systems within the organization act to ensure that each component is operated in an environment that does not damage or distort their materials of construction microstructure. The difference in asset availability and reliability between these two approaches is shown in Figure 3.

Failure-focused maintenance strategies produce assets with poor reliability, under perform, have variability in their failure occurrences, leave defects in assets, and require more frequent planned asset downtime to perform maintenance activities. Comparatively, a reliability-creation approach produces outstanding asset performance, exceptional reliability, and requires downtimes only at the end of a component’s material of construction lifetime.
What is not shown in Figure 3 is the financial implications of the differences between these two approaches. With a reliability-creation approach your operational costs no longer include unscheduled downtime due to failures, replacement component stocks can be reduced. All the while, operational performance of the asset has never been higher, and quality of production is also improved.
Leave a Reply