
Divide maintenance crews so a few skilled artisans do reactive jobs, and the remainder do planned and scheduled work orders
A robust Maintenance Planning and Scheduling Process uses a Scheduled Work Crew capacity planned days ahead with planned jobs. And it has a small Quick Response Crew of people capable to handle any random job.
A great Maintenance Planning and Scheduling Process design separates reactive work from jobs that can be planned and scheduled. This article explains how to re-engineer a maintenance planning and scheduling process to handle reactive and planned jobs.
A principle of work management is to segregate work into like processing so one process can be used to do all similar work. Reactive work and scheduled work are vastly different to one-another. When persons doing scheduled work are also required to do reactive work the urgent jobs always stop the planned jobs from being completed. The planned work duration blows-out, job costs increase, and the work quality is not as good as it could have been.
Each scenario needs different treatment with its planning and resourcing because their time frames for response are so unalike. If all work is handled using one maintenance planning and scheduling process in the presumption that every work order is treated the same way then maintenance crew efficiency is poor and their tool-time is low.
The image below shows a single-stream current state map of a maintenance planning and scheduling process intended to do any type of work. Its design guarantees poor tool-time and low scheduled compliance because urgent jobs must always push-out planned jobs.
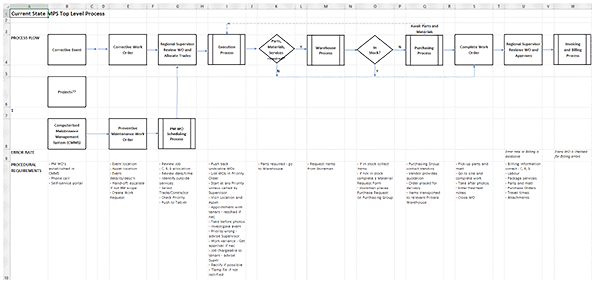
Sudden high priority work is random. A maintenance crew will get through the most work orders if it is structured to handle randomness. This requires all urgent jobs be done by a dedicated team—a Quick Response Team with the skills to do the range of expected reactive jobs. Most maintenance jobs can be planned and scheduled and sent to a crew structured to do planned and prepared work. That work needs to done by a team dedicated to completing scheduled jobs—the Scheduled Work Team. Those people are allocated all work not done by the Quick Response Team. The two teams are fluid and their compositions change to match the workload of the Quick Response Team.
With a dedicated Quick Response Team to address new, urgent work the backlog will stop growing and start falling as the Scheduled Work Team members get through their daily job lists uninterrupted.
The following image shows a two-stream future state map of a maintenance planning and scheduling process designed to handle unknown situations and scheduled work. It guarantees high tool-time and high scheduled compliance because urgent jobs are separated from planned jobs.
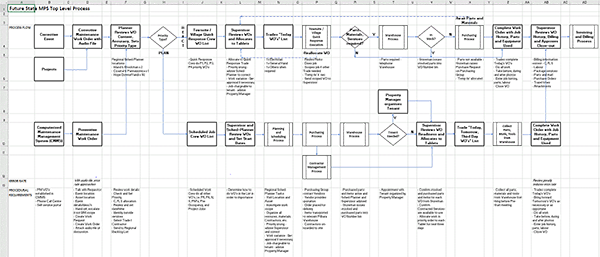
The re-engineered maintenance planning and scheduling process lets the Maintenance Planner investigate the details and build work packs for jobs that can be planned, organised, and scheduled. Work orders ready to start are allocated to the Scheduled Work Crew. Planned and scheduled work orders make a Tradesperson more organised and efficient, so more jobs and higher quality work gets done each day.
An urgent maintenance work order means no planning or scheduling can be done for the job. A tradesperson from the Quick Response team is allocated to do the work within the required response time. It is not until the tradesperson arrives at the job that they fully understand all that must be done to complete the work. The future state maintenance planning and scheduling process is arranged to handle random, urgent work in a structured way that escalates the response depending on what the first-responder finds on arrival.
Leave a Reply