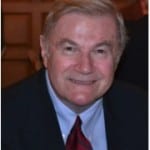
Guest Post by John Ayers (first posted on CERM ® RISK INSIGHTS – reposted here with permission)
This story is about risk at the enterprise program/project level. Design is based on primarily requirements and assumptions. Meeting requirements is usually achievable if they are complete and clear. Soft or poorly written requirements are the source of cost and schedule growth for many projects. Assumptions made during the analysis or design phase if wrong are also a source of poor project performance. This story is one example of a bad assumption.
Background
I was the project manager for a chilled water system designed to cool a shipborne radar. The unit was required to provide 350 gallons/minute at a specified chilled water temperature range. Pump selection was made to meet these requirements based on the pump curve. The curve showed the flow rate that would be achieved at a specific head pressure. Each pump has a performance curve determined by tests performed by the manufacturer. Typically, each pump comes with 2-3 impeller sizes to provide some flexibility in determining the correct flow rate after installation on the ship (in this case).
Pressure Drop
The pressure drop for the chilled water unit was primarily due to the piping and flow components in the system that connect the chilled water unit to the heat source. The pressure drop was calculated based on the physical routing of the piping to the drawings as well as the flow component sections. The assumption made for the calculations was the piping system would be installed per the drawings. If this was not the case, the pressure drop (hence the pump flow rate) could be less than requirements resulting in a potential serious problem.
Risk Assessment
Based on an informal meeting, the biggest risk seen by engineering and leadership team was finding out the performance requirements were not met after installation of the system on the ship. It would be much more expensive and cause potential significant schedule delay if modifications to the system had to be done on the ship. The mitigation plan for this risk was determined to be an engineering performance test conducted in the factory to verify performance before installation on the ship. The test included: chilled water unit; piping and flow devices; heat source provided by a custom furnace; PLC (programmable logic controller) for the chilled water unit; and instrumentation. The piping and flow component selection was based on meeting the same pressure drop as calculated and expected on the ship. The test results showed the chilled water system performance met the requirements. No modifications were needed. The unit was disassembled and shipped to the shipyard for installation. It shipped with the medium impeller installed.
Installation on The Ship
The chilled water unit was installed without incident. However, the piping run to the heater was not installed per print due to unexpected interferences resulting in a much longer piping routes with many more bends than assumed. Hence, a greater pressure drop than calculated. Once the unit was up and running, a performance test showed the flow rate was considerably below the required performance. After a brief assessment, it became clear the actual pressure drop was significantly higher than calculated. Fortunately, the solution to the problem was solved by swapping out the medium sized impeller with the large one. With this modification, the chilled water system performed to specification.
Lesson Learned
- Conduct a formal risk assessment-not an informal one. If a formal risk assessment was done in this case, the pressure drop assumption may have been identified and mitigated.
- When performing a risk assessment on a project, it is very important to assess the design (and other) assumptions made. Many times, bad assumptions go undetected causing havoc later on.
- Make sure your design assumptions can be realized in the field. In this case, it is a little naive to think piping on a ship will be accomplished per drawings. In real life, unexpected interferences or obstacles change the piping route shown on the drawings resulting in higher pressure drop. Always had margin to account for the unknown.
Leave a Reply