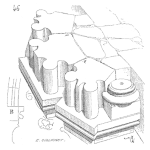
“It was supposed to work in our application. This failure is going to cost us a lot of rig time.”
Was this product checked out prior to purchase? Was it fit-for-purpose? Some due diligence was probably used, but the better question is…was the product assessed through Design Assurance? Design assurance is an engineering process that confirms the product meets performance requirements and complies with design policies and industry standards.
Let’s unpack that statement.
In practice, design assurance is an independent engineering assessment of the product’s configuration, materials, analytical results, design for reliability activities (DfR), laboratory testing, documentation, conformance with industry standards, and more. A quick look at three of these elements will help in understanding why they are of interest in Design Assurance work.
- Product reliability is largely determined by the configuration, which should be driven by the product’s Basis of Design (BoD). The BoD defines the optimal arrangement of components, materials, important interfaces, and more. Basis of Design is further discussed in the Integris article Better, Faster, and Cheaper: Basis of Design.
- Design for Reliability (DfR). An effective DfR program identifies and mitigates equipment risk during product development. Important components of a DfR program include company design policies and risk assessment tools.
- Industry standards. Many equipment risks can be mitigated using industry standards that prescribe standardized analysis and testing protocols.
In the upstream energy business, an operator will use a Design Assurance specialist to assess equipment prior to purchase. A Design Assurance assessment delivers the highest value to the purchaser when performed by an independent subject matter expert.
Truth: Design Assurance will help you make the fit-for-purpose decision.
Leave a Reply