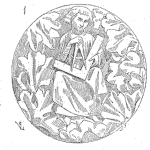
During the design phase, we make decisions that create the eventual reliability performance of a product.
It is the decisions we make that matter.
Also during the design phase, we explore numerous questions.
- Is this the right solution to provide a function?
- Does vendor A provide a robust solution?
- How will manufacturing variability impact quality?
- Will this design work for all customer situations and environments?
We run simulations, do calculations, examine each failure, explore robustness, and answer questions along the way.
We make decisions based on the data, engineering judgment, and common practices.
Collectively the decisions define the eventual actual reliability performance.
What is DOE?
Design of experiments, DOE, is a statistical tool that permits us to make informed decisions efficiently. Each design decision generally involves many variables.
The selection of a component may have a dozen or more considerations that impact the selection.
DOE provides a means to examine multiple factors at different levels.
The approach minimizes the number of prototypes or configurations required to explore the entire space of possibilities.
For example, for a simple example with three variables (factors) with two possible levels (settings or values or options) we can experiment with four prototypes instead of the eight possible arrangements.
The analysis allows us to learn about all eight combinations, thus effectively using limited experimentation to learn.
Combining design of experiments and reliability
The number of variables and decisions that impact reliability seems to never end.
The design team must consider:
- Component durability
- Vendors stability
- Assembly processes
- Transportation and storage environments
- Installation methods
- Operation use profiles
- Maintenance strategies
Within each listed above, there may be hundreds of specific variables to consider.
Teams often use engineering judgement to narrow down the list of important variables, yet often have a dozen or more factors that significantly impact the reliable performance of a product.
Limited resources prevent characterizing each variable, yet we do need to focus on creating designs that meet or exceed customer expectations.
Knowing which variables are essential to consider may begin with a screening experiment. The screening DOE quickly examines many variables to determine which have the most influence on the result.
Using accelerated testing or similar life testing approaches, we can explore the impact of different factors on expected lifetime or robustness.
The screening DOE will reduce the list to a critical few factors that may require full characterization.
Reliability optimization via DOE
Engineering solutions often seek to find the optimal balance between competing requirements.
For example to improve the strength of a beam, increasing the size and weight provides a viable solution. Yet, the space allowed requirements smaller and lighter solutions.
Nearly every decision will have competing priorities.
Finding the right balance that creates a robust and reliable solution will take some meaningful experimentation.
Understanding the relationships and degree of influence each variable has on the final results means you may find the optimal solution.
Guessing or working without data suggests you are relying on luck.
DOE provides a tool that permits the engineering teams to find and optimize solutions considering the many priorities and requirements.
Combining reliability testing and DOE enables the team to consider the information when making a decision that impacts reliability performance appropriately.
It does take some practice to master DOE, therefore, get started. Dive in and try a small DOE array considering three factors and two levels each.
You will quickly find many appropriate applications for this powerful tool.
Related:
Taguchi Design of Experiments Approach (article)
Reliability as Part of Every Decision (article)
Guiding Programs by Product Goals (article)
Leave a Reply