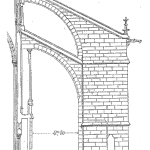
When engineers design a machinery part, they begin by defining the operating load range it will experience during its service life. This range will include the loads when the machine part is not working through to the maximum stress that it will operate under. Examples of high stress situations include operating overload events, or when starting up under a large load. How great the imposed stress reaches and how often those events occur changes a part’s reliability.
The term used to categorize the impact on material-of-construction health and in-service reliability is called the Physics of Failure. It is the science of what leads to having equipment failures and breakdowns.
Using this information, the engineer will select a material-of-construction for the part that will withstand the predicted range of operating stress and provide a ‘factor-of-safety’. A factor-of-safety is the planned separation between the maximum designed service load and strength of the material-of-construction, which is known more commonly as material strength. Material strengths vary based on multiple factors. They include the raw materials used, the manufacturing process, and the quality control and quality assurances applied in making the item.
Even though equipment design engineers are literally designing to prevent failure by including a factor-of-safety into their parts material selection, it is common to find when in operation that what was intended to happen in theory is not what occurs during the component’s life. This is because variations in processes during the fabrication, supply chain, installation, operation, or maintenance phases of an asset’s life cycle introduce defects that reduce the reliability of the material-of-construction.
The risk of introducing defects that become operating equipment failures can be identified, mitigated, and even eliminated through use of Plant Wellness Way EAM methodology. Insights from Physics-of-Failure science are used to re-engineer business processes, change procedures throughout the asset life cycle phases, and ensure the best operating and maintenance practices are used when in-service to minimize material microstructure loads and stresses.
If your operating plant and equipment are unreliable and you want sure answers to maximize reliability, then ask us how Plant Wellness Way EAM methodology can be used to remove the stresses and risks being suffered by your operating assets.
Leave a Reply