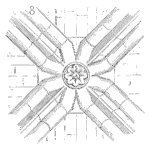
Welcome to my latest 10-part series of blogs called “Uptime Insights”, where we explore a journey of excellence in maintenance. To stay on top, managers must implement strategies that keep operations performing at high levels. In these articles, I will show you how to achieve excellence in maintenance – a critical business process in any capital-intensive industry.
Uptime Insights Part One:
Developing A Strategy To Achieve Excellence In Maintenance
Leadership is all about making change and taking your organization in new directions. Leaders rock the boat, managers keep it stable. In choosing excellence you’ll be choosing a path of constant change and improvement – leadership is essential. Leadership is about strategy, effective execution and your people – without them you accomplish very little. If you want excellence you need leadership.
Maintenance is an important business function. It sustains your productive capacity. It is a part of your fixed and variable costs. Reducing maintenance costs through efficiency gains (doing maintenance the right way) and effectiveness (doing the right things) increases operating margins. Just as it contributes substantially to the company’s safety and environmental performance, it also impacts on how financially “risky” the business is.
Productive assets that are well maintained can meet production commitments more easily and risk is reduced, something that lenders and insurers like to see. If you are building a new plant consider the importance of maintenance and reliability considerations at the design stage when you have the greatest opportunity to reduce life cycle operating and maintenance costs. All of these are factors to consider in developing maintenance strategy.
Strategy can be as simple or as complex as you like, but simple works best. Your business objectives, the asset environment, its present state and the state of maintenance management practices are your starting points. Understand what it means to be a high performer and using successful practices.
What’s best for your company is what works best for your company – there are no absolute “best” practices. Decide what you’d like to achieve – that’s your “vision”. Compare what you do today with that vision and consider using successful practices, such as those described in Uptime, to close any gaps. Plan the improvement activities and manage them like any other improvement project. Execution is what matters – that’s choosing.
Some companies choose to outsource maintenance. Do it for the right reasons. Transferring your problem to someone else may not be the answer and it can even be harmful. If maintenance is of strategic importance or it’s unique to your business you are probably best to keep it in house.
Once you’ve embarked on making improvements it’s important to sustain them. Excellence as described is a journey, not a destination. Never let up. You’ll know if it’s working when you find yourself dealing with new problems every year and not repeating the same mistakes.
In our next blog we’ll explore part two of our 10 part series “Uptime Insights: People are your most important asset. Or you can download the entire series in our eBook “Uptime: A Journey Of Excellence
Leave a Reply