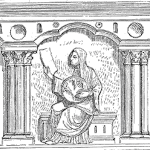
as reliability professionals anymore?
During a normal day, we unconsciously tie our shoes, brush our teeth and drive to work, mostly by routine and without too much conscious thinking about the tasks. Occasionally we answer the phone and have to think a little about the conversation. Or we design an experiment for the next project, thinking we can save time by using the same test as last time. Then we slip comfortably into a routine. Do we not think anymore?
Reliability engineering is thinking.
Think situationally
We have to fit the right tasks and tools to the specific and current situation. Materials, designs, processes, customer environments and reliability expectations all change over time. We know more about failure modes and mechanisms over time. Our experience continues to grow. Being reliability engineers, we consider the situation and recommend a course of action based on our knowledge. We recommend studies or experiments, we advise on design practices and process controls. We are knowledge workers. We are paid to think.
So, do some refuse to think? Slipping into a routine, running the same studies and tests, preparing the same plans, implementing the same techniques, is comfortable and saves time. And, generally doesn’t work very well. When we step out of the role of a thinking reliability engineer, we pass opportunities without noticing. We move blindly to the next task. We believe that having a lot of activity is doing our job. No. Doing our job is thinking and doing the right activities.
The other day a friend told me about an online conversation where someone said, “MTBF and Reliability are not related and should not be confused.” or something to that effect. My friend, being aware of my campaign to eradicate the use of MTBF, thought this was a new and troubling argument to continue using MTBF. I agree. It is troubling. How many of us, reliability professionals, have stopped thinking? How many do not take the time or exert the effort to learn the basic concepts of reliability engineering? How many have been training and believe there is one set of tools to apply to every project? How many are just moving through the day in a routine?
As you start your day, going through the routines that bring to your place of work, set a daily reminder to stop and think. Why are you doing the specific tasks you are doing today? Do you know why something has to be done with a specific technique? Ask ‘why’ all day along. Make yourself see the world around you and ask yourself, ‘Am I seeing what I expect or not? Why?’. Each task should have a purpose and value.
Doing a component life study may have the purpose of finding failure modes and mechanisms. Does the work lead to that goal? Are we using the right technique? Could we do this better? Are there better ways to get this done? If you’re running a time terminated demonstration test and do not expect any failures, you might not be thinking. If you expect to pass your HALT, you probably fell into an unconscious routine. If you use MTBF to estimate your maintenance schedule, you certainly are not thinking.
Stop it – wake up, and think.
I really like reliability engineering and would say I’m a campion of the profession. It is because every day I have to think. New designs, new materials, new components, new challenges, and every project is different with different constraints and objectives. We are expected to learn something every day. We get to work across the entire product life-cycle and with nearly every function in the organization. We move from a vendor meeting exploring the process stability of a painted finish to briefing the project team on the status of remaining reliability risks. We have the opportunity to apply our skills, knowledge and thinking prowess every day. It is up to us to do so.
So what do you think? (or do you?)
Leave a Reply