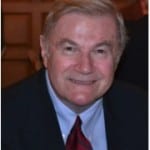
Guest Post by John Ayers (first posted on CERM ® RISK INSIGHTS – reposted here with permission)
Most companies have policies and procedures for concurrent engineering but many are ineffective for various reasons resulting in poor implementation of improved producibilty in their products. I have made this observation based on working for a variety of companies in different industries. Three examples of different approaches I encountered are presented below for your consideration. Two of the examples were used by defense companies, one of which I consider excellent and the other poor. One method was used by a commercial company is one I consider to be very good.
Example 1: Defense Company Poor Approach
A large defense company I worked for had an extensive concurrent engineering program. It worked as follows:
When a contract was awarded, one or two manufacturing engineers (depending on the size and complexity of the project) were assigned to the project to provide producibility support during the design phase. They attended design review meetings typically starting with the PDR (preliminary design review). As a member of the team, they were required to review design documents and make comments. They had no approval authority. There were a few problems with this approach.
First problem: Getting the manufacturing engineers involved at the PDR level was too late because by that time the concept and the basic manufacturing approach had been cast in stone by virtue of the proposed design, concept approach, and the budget and schedule time incurred in developing the preliminary design. As a result, most of the major producibilty suggested changes were rejected by the team leader because “we are too far down the track to make the recommended changes”. The only suggested changes accepted by the team leader were small. For example, increase a tolerance. The manufacturing engineers need to be involved during the early stages of the project starting with the proposal and if not certainly during the concept definition phase.
Second problem: The lack of authority and sign off approval of the concept, PDR, and Critical Design Review (CDR) resulted in giving lip service to the manufacturing engineers recommendations and not serious consideration. The recommendations were taken most of the time as comments and not mandatory changes to the design. Manufacturing sign off authority for the design is essential to establishment of a good effective concurrent engineering program.
Third problem: Assigned manufacturing engineers many times were not qualified or experienced in incorporating producibility changes into a design. The level of qualification and experience is to a large extent is a reflection of the company’s’ commitment to improved producibility. A top down commitment from management is essential to establish an effective concurrent engineering program.
Example 2-The Defense Company Excellent Approach
This defense company was smaller than the one in Example 1. Their approach corrected all of the problems noted in noted above. We won a large Navy contract for designing, fabricating, testing and delivering hundreds of low cost expendable acoustic training targets. A qualified and experienced manufacturing engineer was assigned to the proposal team which included sign off authority on the proposed design. As part of the proposal team, he created a preliminary assembly flow diagram showing assembly stations, inspection stations and testing points. This was very helpful in generating the proposed cost and price. He was assigned to the project after the contract award providing very important continuity. The manufacturing engineer sat in all of the design review meetings and his comments were taken seriously because the team leader knew he needed his signature approval. Execution of the contract went very well in large part due to the concurrent engineering effort invested into the project starting with the proposal.
Example 3- Commercial Company Very Good Approach
I worked for a large lift truck and material handling company that designed and built inventory based on marketing input. The sales force was responsible to sell the inventory. As a design engineer, I was responsible for generating the design concept, the preliminary top assembly layout, and sizing the components to take the loads. At this point engineering turned the design over to manufacturing who owned it for the remainder of the design development and detail design. In other words, engineering took a back seat to manufacturing. The assigned manufacturing engineer dictated the method of manufacturer for each component including review of each drawing to ensure the tolerancing and design was best one suited for the company’s manufacturing processes. One example of a drawing alteration they may have insisted on was changing a corner radius on a plate to a 45 degree chamfer because it is cheaper to shear the corner than mill a radius. Another example of a change they would ask for was establishment of datum planes from which dimensions were taken to be from a machined surface in lieu of a point in space that would require an expensive fixture to measure. This approach worked very well for this type of commercial product manufacturing company.
SUMMARY
Three different concurrent engineering approaches are presented above. Each one tailored to the company’s manufacturing process and the industry best practices. As noted above, some are very good and effective while others may leave a lot to be desired. The lessons learned I took away from my experiences are:
- Involve manufacturing in the design process starting with the proposal and continuing through concept development, PDR and CDR.
- Provide manufacturing sign off authority at all phases of the design to ensure their recommendations are incorporated and not left in the minutes of the design review as just comments.
- Assign qualified and experience manufacturing engineer(s) to a project starting at the proposal phase to ensure continuity and meaningful and effective producibilty features are incorporated into the design as opposed to minor comments just to check the box.
- Establish a company sponsored concurrent engineering training program to create a team of manufacturing engineer specialists that understand producibilty methods resulting in real product improvement in lieu of just lip service contribution to the team.
Bio:
John earned a BS in Mechanical Engineering and MS in Engineering Management from Northeastern University. He has a total of 44 years’ experience, 30 years with DOD Companies. He is a member of PMI (project Management Institute). John has managed numerous firm fixed price and cost plus large high technical development programs worth in excessive of $100M. He has extensive subcontract management experience domestically and foreign. John has held a number of positions over his career including: Director of Programs; Director of Operations; Program Manager; Project Engineer; Engineering Manager; and Design Engineer.His technical design areas of experience include: radar; mobile tactical communication systems; cryogenics; electronic packaging; material handling; antennas; x-ray technology; underwater vehicles; welding; structural analysis; and thermal analysis. He has experience in the following areas: design; manufacturing; test; integration; selloff; subcontract management; contracts; risk and opportunity management; and quality control. John is a certified six sigma specialist, certified level 2 EVM (earned value management) specialist; certified CAM (cost control manager).
Leave a Reply