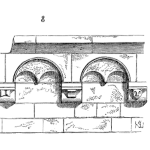
To reduce maintenance costs and production downtime it is necessary to reduce the causes of the maintenance and downtime. Both maintenance and downtime are an effect and not a cause. The causes can be traced back to defects and errors from a variety of sources. Knowing that defects eventually lead to future equipment failures, production downtime and lost profits, it is necessary put strategies into place to purposely prevent them occurring in the first place and to eliminate them if they are present.
Keywords: defect elimination, fault cause analysis, root cause failure analysis
All equipment starts life new. It comes from the original equipment manufacturer fresh. If you do nothing about controlling them, it also comes with future failures built into it by the OEM.
These future failures are the design errors, the materials selection errors, the fabrication errors, the assembly errors and any transportation damage. When installed, further causes of future failures arise from incorrect installation, incorrect site assembly, incorrect mounting practices, inadequate environmental protection and deficient foundations/supports.
Some of these errors, along with commissioning errors and operating errors, cause failures early in the equipment’s operating life and explain early-life or ‘infant mortality’ failures. Those defects and errors that do not appear during equipment infant-life will eventually surface and cause failures sometime later, during its operating life.
The preferred terminology is to call the errors ‘defects’, because that is what you get as a consequence of the mistake. But the truth is that a wrong action (or no action) was taken at some point in time and as a consequence a defect was created. Every defect has a cause, and often more than one.
Another truth is that most times equipment goes right. Stoppage due to failure is not the common situation. The problems with failures isn’t the failure itself. It is the scale of the consequences that can result from them. The same failure can be completely unimportant or it can be catastrophic, depending where it happens. When the consequences of failure are bad, you want to do everything possible to never let them happen!
Defect Elimination is the Answer
Starting from new, a part properly built and installed, without any errors, will operate at a particular level of performance. If looked after properly it should, ideally, deliver its design requirements all its operating life.
As its operating life progresses any of those previously hidden manufacturer’s and installer’s errors noted above start to make their effects shown. For some reason the equipment starts to fail. Failure causes can be introduced at anytime. They can appear during operation from management decision errors, operating errors, repair errors, abuse and even acts of Mother Nature.
If you want superbly reliable equipment you must prevent the introduction of defects and errors at all stages of the equipment life cycle, and also act to remove the defects and errors already present in it. By getting rid of the defects that generate future failures, you will greatly reduce your future maintenance requirements, and hence guarantee great production performance.
An average item of equipment has several dozen direct and consequential failure modes built into it.
The best asset life cycle strategy to adopt is to not allow the causes of failure modes into the equipment from the start. Such strategies require that you put in place management controls and quality standards that must be followed to detect, control and stop the introduction of errors and defects into your equipment. Throughout an asset’s entire life—from concept, to design, to manufacture, to installation, to operation, to decommissioning—all causes of failure are eliminated so there can be no defects.
For example a wise strategy at the design stage is to look for every failure mode possible and remove it while on the drawing board. You take each part of the equipment, assembly by assembly, component by component and list its possible defects and errors and then introduced strategies and plans to address every one of those failure paths in the design.
A spreadsheet can be developed of all component and assembly failure modes and this becomes a check sheet to assess all future equipment purchases and designs. It also identifies where you should use preventive and planned replacement maintenance strategies. Some people call this RCM (Reliability Centered Maintenance). My dislike of RCM is because RCM accepts failure as normal. If you want world class reliability you must have no failures. It’s just plain common sense to realize that maintenance does not cause reliability. You do maintenance because an asset is unreliable!
Figures 1 highlights where most failure casing defects and errors come from and explains that eventually you will have so many problems in your operation that your bucket overflows and you drown in strife! I first came across this defect creation model at a seminar delivered by a DuPont Chemicals manager touring Australia in the early 2,000’s.
Maintenance is used to address the effects of the continually growing number of defects. You will often hear people say ‘well, add another PM into the system’, hoping that maintenance will prevent the problem in future. But all they have done is add more cost and resources requirements into the production costs! More maintenance is not the answer—it only adds more expense without benefit of defect elimination.
Maintenance can only act to ‘drain away’ the impact of defects. It hides and masks their effect. But it cannot remove them because maintenance only replaces like-for-like. The original defect remains.
You now have an equipment defect model that explains why there is so much crisis and ‘fire-fighting’ by maintenance crews. Doing maintenance does not fix problems, it can only rejuvenate equipment. If the cause of the problem is not removed … it remains to reappear again in future.
Figure 2 shows how maintenance can only act to ‘keep your head above water’ by addressing the impact of defects. As you introduce more defects into the business, so must you increase the size of your maintenance crew and maintenance resources to deal with them.
A Simple Defect Elimination Process
Only by intentionally reducing the size and quantity of defects entering your operation will you be able to reduce the maintenance you now need to do to stop defects from flooding and drowning you out of business.
Each of the defect categories need to be addressed systematically. Effective mechanisms must be introduced by you to combat and defeat the cause of the defects. Unless the causes are controlled and stopped you will be continually battling failures.
Defects will never stop, unless you act to stop them! They are forever being introduced and perpetuated by poor procedures and practices, poor quality control and poor management systems. Unless you purposefully act to stop defect introduction, every new piece of equipment, every new part, every new person that joins your company bring with them defects and errors, to one day cause future failures. How catastrophic those failures will be will depend on the internal controls you have in place in your organisation to prevent and control them.
You have to intentionally, proactively, with the future well-being of your business in mind … put into place a strategy to eliminate and eradicate your defects forever!
This logic is sound and sensible – get rid of the defects causing the problems, so that you can reduce the amount of maintenance you need to do, because you now have less defects to address. That way you get both lower maintenance costs and more production!.
Figure 3 shows you that when you reduce the number of defects entering your operation you can also reduce the amount of maintenance you need to do.
Here is an easy, simple and powerful model to guide you in removing the equipment defects you have in your operation.
- Select one failure and identify where defects and errors were first introduced through the use of root cause failure analysis.
- Use resources skilled at eliminating the root cause and action a plan to engineer-out the causes forever. (I implore you not to use work procedures to control engineering failures. If you do that you will soon run out of people in the company to make responsible for controlling the causes you will find. They will also consider it an impost on their job and sub-consciously lower its importance so they do nothing about it and the failure will repeat. Use work procedures to direct people’s attention, not to compensate for equipment defects.)
- Introduce clear, written quality production and engineering standards into the appropriate levels and locations in the organisation that contain checks and tests to prevent the defects from again entering into your company.
- Train and re-train your people to meet the new standards.
- Measure their performance against the new standards.
- Repeat the above until the defects are so few that your operation is the world-class leader in your industry.
It is necessary to use a quality system because a quality system is self-improving, self-correcting and self-developing. With a quality system properly applied, your company will continuously improve because continuous improvement is built into the way you do business. Without a working quality system you require individuals to remember to do the right things every time. This approach means that you are counting on a lot of good luck for things to go right!
You can remove defects and stop failures by taking a personal stand and start introducing the right quality management practices into your operation, especially in your own personal work. Only by you adopting better systems and methods, and causing the introduction of better practices and standards at every stage of the production, engineering and maintenance process, will you ever reduce the equipment failures in your operation.
If you want to master equipment maintenance and have outstandingly reliable production, you must stop the introduction of defects and errors into your operation! If you want to seriously reduce maintenance costs then reduce the number of ways your equipment can randomly fail.
My best regards to you,
Mike Sondalini
Managing Director
Lifetime Reliability Solutions HQ
Leave a Reply