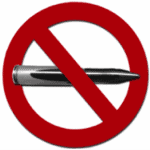
We know that there are no “quick fixes” or “silver bullet solutions” when it comes to improvements in maintenance management. In my last article I pointed out that many separate conditions and events must come together properly to achieve “schedule success” – i.e.: the high level of compliance to a schedule of planned work as produced by your planners. That list of includes:
- The scheduling itself must be realistic and achievable,
- Planning of the work must be thorough enough to allow for good scheduling,
- Work execution must be effective and more or less within the allotted time frame,
- Supervision of the workforce must be effective but not overbearing,
- Everyone involved in the processes must be motivated to achieve the same goals – effective work execution,
- Materials, parts and consumables must all be available when and where needed,
- Planning, scheduling and materials management must communicate to make the above happen,
- Work priorities must be respected by operations / production as well as maintenance,
- The right work must have been identified for planning, etc. or you’ll be doing the wrong maintenance,
- After the work is done, take advantage of the opportunity to note what worked and didn’t work well – learn from the job just completed so that future plans can be improved and
- Your proactive maintenance program must be effective at eliminating surprise failures.
In this article we will look at that last bullet point – having an effective proactive maintenance program.
Reliability Centered Maintenance (RCM)
Reliability Centered Maintenance (RCM) is without doubt the most effective method for developing a “failure management program”. I use that term because it isn’t just about maintenance work. A good RCM implementation will result in maintenance actions, operator actions, training changes, procedural or process changes, engineering changes and conscious decisions to run some assets to failure.
Each of those choices is intended to address a specific failure of the asset to perform its function to your pre-defined standards of performance. Sometimes those functions are critical to your operations and sometimes they are not. Every failure does not warrant extensive effort to prevent or predict it. E.g.: In an airplane a failed latch on an overhead luggage bin will not impact operational capability in a big way. A quick fix (lock or even tape it shut) can quickly eliminate the worse consequences – a loaded bin opening up and dropping items on passengers. Running to failure, even though it is a failure on an airplane is entirely acceptable.
RCM is an excellent methodology for identifying the failures you are likely to encounter and determining how best to deal with them, all with an aim to reduce the consequences of the failures – not necessarily eliminating the failures themselves. After all, it is what the assets do for us that matters. Loss of that capability is a consequence that we may or may not be willing to live with. Eliminating or minimizing the consequences is not always the same as eliminating the failures.
But will RCM deliver an effective proactive maintenance program?
The answer is two-fold – and the short version is both “yes” and “no”.
Yes – RCM, if properly executed, will deliver an excellent output comprising tasks at specified frequencies identifying who should do the work, design changes, training changes, process and procedure changes, etc.
No – RCM will not deliver results if you don’t follow the program. That statement is fairly self-evident – there is no point putting the effort into RCM if you are unwilling to follow its output decisions and do exactly what it recommends. Yet sadly, this is precisely where most RCM programs fail. Good decisions are made as a result of thorough and extensive analysis work, but those decisions are not put into action.
Why not?
Some users of RCM don’t quite get the message that it is only an analytical methodology. Its outputs must be followed, turned into action, or you’ve done nothing more than gone through an interesting intellectual exercise. The RCM “project” doesn’t end with the analysis reports and presentations of those outputs to management.
Let’s go back to the “yes” answer above. Note the words, “if properly executed”. RCM is a fairly straight-forward method with seven steps. On the surface it looks easy to follow and for anyone who has attended RCM training, they probably get the impression that it is easy. The instructors are always experienced practitioners who know it so well that they make it seem easy.
This past weekend, I attended an advanced motorcycle skills course. The instructors made “hanging off” the bikes (like a racer) look easy and they broke it down into 10 easy to follow steps. Then we practiced. Imagine how it feels on your big street bike trying to remember 10 steps that you just learned about for the first time, while fast approaching a tight turn. What looked easy with an instructor doing it was suddenly much more difficult to put into practice. Once I could remember the steps and execute them properly, then hanging off the bike in a turn became much easier. More practice will be needed to make it look smooth.
RCM is much the same. There are seven steps and a lot of background knowledge that sits just behind them. Each of those steps must be executed properly because they build on each other. Make a mistake in the earlier steps and the rest of the analysis is at risk. Get them all right and the analysis goes smoothly.
Reading about those steps in a text book isn’t enough to really learn them. That will create a degree of familiarity but it won’t create the deep understanding needed for execution. To get that you need training and practice. The training digs deep into each of the seven steps and allows time to practice so that you gain a degree of knowing. It’s a bit like muscle memory – during the training you are just getting a feel for it. Once you do your first analyses with a skilled facilitator you will gain that muscle memory and it won’t fail you from then onwards.
Hopefully you can see that the training is an essential part of the learning process towards success. Skilled facilitation is the next essential part. Someone who knows how to carry out analysis is unlikely to be a good facilitator without some sort of training in “how to” facilitate. Facilitation is a skill set that is drawn largely from behavioral sciences and knowing how to manage a small group people to get a desired result. These are not skills that most technical people possess without some training.
Just like the analysis, facilitation requires training. In the courses we offer there are over 40 different skills that are needed and each requires practice. It begins to come together when doing classroom case studies but the first time any facilitator really puts it all into use is when he / she facilitates his / her first real analysis with a team of your own analysts in your own operational environment.
Imagine yourself in the position of leading for first RCM analysis. You’ve had the analyst training and some practice doing case studies. You’ve then taken a facilitator course and practiced those skills. You were sharing the facilitation responsibilities with your classmates so you didn’t really facilitate a full analysis. Now you are back in your own plant and leading a team of your co-workers who have taken analysis training (quite possibly on the same course that you first took). Are you really ready for this?
Chances are you are nervous and worried that you’ll mess it up. Our experience with this situation tells us that you are right to be worried – without mentoring you will probably make mistakes. We all make mistakes after all, but this time, you’ll be watched by peers who may be able to spot them and those mistakes will lead to a lack of confidence in the results you produce.
Mentoring of a newly trained facilitator removes those concerns. Having an experience facilitator (likely the practitioner who taught you) in the room removes a lot of stress. The practitioner is your safety. If you make a mistake it will be observed and you’ll receive gentle correction. Your risk of going far wrong is very much reduced, your stress level will be lower and if you do make a mistake it will be corrected so the risk that you will produce a compromised analysis is all but eliminated. Not only will you feel more comfortable, but your analysis team will be more comfortable that they’ve got someone experienced in the room to make sure it all goes well. Mentoring doesn’t take long – usually no more than two (2) full analyses, depending on how well you learned your materials as a facilitator.
Finally, a word about follow-up. Once the analyses are completed there is much work to be done. Maintenance tasks must be entered into your CMMS so that they trigger work orders at the right times. Procedural or training changes, process changes and engineering changes all need to be initiated and executed. Wherever you’ve identified a failure as being tolerable and made a “run to failure” decision you need to have a way of communicating that to operations. You don’t want them creating emergency work orders for every failure of some of those can be tolerated. They need to know that a lower priority is appropriate (indeed preferred) in those cases. And even then, the work isn’t done.
The rest of the conditions listed at the start of this article must be met.
RCM isn’t a quick fix or silver bullet solution. It requires a great deal of preparation and care in execution then follow-up action.
To learn more visit Conscious Asset where you will find training, workshops, books, and resources.
Leave a Reply