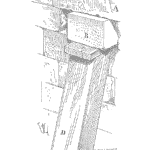
Abstract
Flow meters – don’t believe what they tell you. A flow meter is an instrument that measures the amount of fluid (liquid or gas) that passes through it. The meter in the pipe is the detecting device and increases the count when a specific quantity of fluid passes by. There are several types of flow meters in common use. They include magnetic flow meters, vortex flow meters, mass flow meters, turbine flow meters, rotor blade meters, paddle flow meters, and ultrasonic flow meters. Usual the quoted accuracy on the flow meter specification sheet is for water at 20oC. However when the meter is installed in a process application it is unlikely that the meter will meet the quoted accuracy without site-specific calibration. Keywords: calibration, certified test equipment, flow meter accuracy.
The manufacturer performs laboratory trials of its equipment to insure the flow meter meets their claims for accuracy. Since the manufacturer does not know where their meter will be used they standardise the tests by using water at known conditions. Unless the meter is used in a situation identical to the laboratory conditions the given accuracy is unlikely to be achieved.
Problems that Produce False Readings
Below are listed problems that have occurred with flow meter installations that produced false results.
- PLC scan rate is less than meter pulse rate and meter pulses are not counted.
- Sediment wears away the meter’s internal clearances on the impeller, rotors or paddles and the fluid slips past.
- Solid items, like bits of plastic bag, gloves, rags, parts from other equipment in the process and polystyrene coffee cups, get jammed in the meter. Always install a strainer up-stream of meters with mechanical parts or protrusions into the flow, such as vortex flow meters.
Product density is substantially different to water. Examples are 50% sodium hydroxide (s.g. 1.5), 98% sulphuric acid (s.g. 1.8).
- Software adjustment factors added in to make the meter produce the required results are lost or changed.
- Product temperature varies and alters the product density. In this case it is necessary to factor in temperature effects on the density.
- Temperature changes in the meter electronics or associated electronic equipment in the control loop caused by the process fluid or local environment conditions. Electronic items change behaviour with temperature changes.
- Broken turbine wheel, rotor blades or paddles.
- Leaks under magnetic flow meter linings at liner joints
destroy internal circuitry - The meter accuracy varies as the flow rate varies.
- Meter position or orientation allows bubble inclusion in the
liquid (two-phase flow). When measuring liquid the meter must only see liquid and absolutely no gas. Good practice is to place the meter 10 pipe diameters downstream and 5 pipe diameters upstream of turbulence creators. E.g. valves and elbows.
Calibrate to Prove Accuracy
To prove a flow meter is accurate it is necessary to measure that what is counted through it has actually come out of it. For liquid this requires the use of either accurate scales to measure the weight of the volume put through the meter, or an accurate volume to prove that a given amount has actually passed through the meter.
The calibration will need to be done at several different flow rates across the range of flows experienced in the process. This is necessary to confirm the extent of the error at low process flows through to high process flows.
To insure accurate in-field calibration it is necessary that the calibrating equipment is of even higher accuracy. If using a scale to measure weight insure the scale has been calibrated accurately and the scale’s divisions will give you the resolution you require. If measuring into a known volume, such as a tank, insure the tank has been accurately calibrated by appropriate methods and the error on the measured calibration is within the tolerance of the meter. Beware that dipping a tank to measure its level has a plus or minus 1-mm error even for highly experienced persons.
When it is absolutely critical to have certainty in a flow meter’s reading it is necessary to instigate regular checks of the meter using recognised industry standards and practices. Typically they include the following:
- Use of governing body registered procedures.
- Use of an independent, qualified and certified third party to
conduct the tests. - Tested and certified highly accurate test equipment, test
meters and gauges. - Certified, experienced, competent testing personnel.
If you are paying to receive product from others through their flow meter it is advisable that you get quarterly calibration checks done on it. Install your own flow meter to confirm their results and to insure they maintain its accuracy. Keep copies of flow meter calibration records from commissioning and all subsequent tests and trend them on a graph to observe if the meter remains accurate throughout its operating life.
Leave a Reply