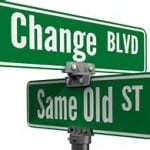
Change happens slowly
The goal of a reliability initiative is to save money, not to “install” a system.
If that is not your current goal, then how did it get changed? Change sometimes happens slowly, so slowly that we don’t notice it.
I’m reminded of a fable about a camel and a Bedouin. It is cold outside and the camel asks if he can just put his nose in the tent, then his face, then his head, and it would be just so kind if he could get his neck in there as well. You get the picture, and soon the Bedouin is outside, and the camel is inside. Suddenly, the Bedouin realizes this.
The change happened so slowly that he didn’t realize the change until he stopped and thought about it.
What is the goal?
This slow change concept applies to many things, and I think that sometimes we forget to stand back and ask ourselves – “how did we get out here in the cold?”
What is the overall goal of a reliability program?
Is it to establish an organization that installs and maintains a process that includes reliability Engineers, a CMMS, work order system, planners and schedulers, RCM process, correct maintenance strategies, etc., or is it to save money?
If we step back and think about this, we should ask, has installing a system become the goal? Are we out in the cold like the Bedouin was without realizing it? Let us not forget that the real goal is to save money, not put in a system.
The system is just tools and processes to help us save money. I believe this is what the Toyota Production System did, is it not? They fixed things and eliminated defects, then put tools in place to help them maintain their gains.
Focus on the money
Have we moved away from the actual objective and made it more about the tools?
This could account for those programs that are struggling with support. People have worked so hard at setting up the system first, with the promise that it will save money, that they forgot to “save some money” and put the systems in place to help them.
It takes 10 man-years to set up a system
Unfortunately, it takes a long time to set up a system.
I had three data points while I was at Alcoa that corroborated that it takes 10 man years to install and initiate all the standard tools in a system.
Two of the data points were from actual installations by people who had done it – one from Cargill and another from someone who was on a corporate team just prior to coming to work for Alcoa.
If you go to management and tell them “I can save you millions of dollars – just give me 10 man years of time and money,” they will say “10 man years! I need results in 3 weeks.” This makes sense doesn’t it, with today’s CEO’s coming from a financial background. It is actually very predictable.
The problem with this is that in spending all this time on working on the system, we may forget what the original goal is.
Work in Quadrant I and II
How can we fulfill both the short-term and long-term goals?
This can be accomplished by having goals that keep management happy and at the same time establish a state of the art maintenance process.
We can take a cue from Stephen Coveys Time Management Matrix, shown in figure 1.
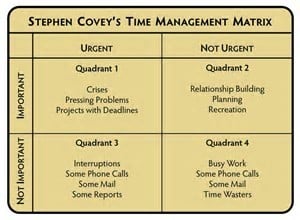
For a complete discussion, you can read his 7 Habits book. For now, I am most interested in the Quadrant I and II boxes.
Management always seems to be in the Quadrant I box, while the people establishing the overall process are in the Quadrant II box. Both have valid points and reasoning for this.
The problem for those wanting to work in Quadrant II is that whether we like it or not, “management may not always be right – but they are always the boss,” as a coworker once informed me.
So how do we deal with this dilemma? Per Stephen’s book, you have to spend time in all of the quadrants. That means that you must show value quickly by spending some time in Quadrant I, while also working on long-term processes in Quadrant II at the same time.
Get the savings quickly but work toward a long-term system
I found that the simplest way to do this was to implement a Root Cause type of process immediately and get some problems fixed quickly.
While this is going on, work on Quadrant II items, like improved maintenance strategies, work orders, CMMS implementation, planning and Scheduling, RCM implementation, etc., and generally improve the system. This way both sides get what they want.
Management will get the quick-dollar savings that allow them to continue to support the overall process. Reliability personnel get a process built on sound practices, that utilize state-of-the-art tools. Maintenance gets improved wrench time and efficiency improvements that allow the maintenance department to appropriate at a lower cost.
By establishing the root cause process and generating quick wins, it also gives operations something they can get behind because it made their life easier.
This gets the process ingrained in the way the company does business, and the process is then utilized long-term to continue to extend the MTBF which is then managed and supported by the system tools.
Leave a Reply