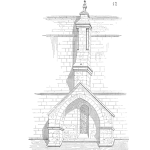
HALT (Highly Accelerated Life Testing) is the foundation for the definition of HASS (Highly Accelerated Stress Screening) and HASA (Highly Accelerated Stress Audit).
HALT is primarily used to expose weaknesses in the design of a product by subjecting it to extreme environmental conditions such as temperature, vibration, and humidity, in order to identify and eliminate design flaws and weak points before the product is released to the market.
HASS, on the other hand, is performed during the manufacturing stage and prior to shipment and sale. It is a stress testing methodology aimed at improving the reliability of the finished product. HASS guarantees ongoing reliability of the product and adheres to the design changes built during HALT. It is performed on completed assemblies to verify that no additional weaknesses are found during the manufacturing process.
HASA, or Highly Accelerated Stress Audit, is a step-by-step process that induces vulnerability in a product, causing eventual failure, which is then analyzed and corrected. It is aimed at maximizing the operating and destruct margins of a product. HASA is performed to ensure that no new weaknesses are found during the manufacturing process after the design has been improved based on the results of HALT.
ALT (Accelerated Life Test), on the other hand, is used to reduce Design Validation (DV) time by identifying the critical sub-component life. It involves testing a product under accelerated conditions to predict its life expectancy and to uncover potential failures that may occur over time in a shorter test period.
Accelerated Life Testing (ALT) works by subjecting a product to conditions such as stress, strain, temperature, voltage, vibration, and pressure that exceed its normal service parameters. This process is aimed at uncovering faults and potential modes of failure in a short amount of time. By analyzing the product’s response to these tests, engineers can make predictions about the product’s service life and maintenance intervals. ALT can be used to simulate the extreme circumstances a device may experience in a real-world environment, leading to improved product performance, faster time to market, and reduced warranty costs.
The data obtained from ALT is analyzed using specialized techniques, including mathematical models, to translate the over-stress data into meaningful predictions about the product’s behaviour under normal operating conditions.
Ultimately, ALT allows for the rapid assessment of product reliability, identification of potential failures, and improvement of product performance.
The main differences between Highly Accelerated Life Testing (HALT) and Accelerated Life Testing (ALT) are as follows:
- Purpose:
HALT is a qualitative test used to highlight areas for improvement, while ALT is a quantitative test used for estimating the real-use reliability of a product.
- Duration:
HALT is relatively quickly accomplished, taking a day to a week, depending on the size and complexity of the product, while ALT may take a day to months to accomplish, depending on the ability to accelerate the failure mechanism in a meaningful manner.
- Analysis:
ALT is a quantitative analysis, while HALT is a qualitative analysis.
In summary, HALT is focused on qualitative analysis to identify areas for improvement, is relatively quick, and is not used to estimate real-use reliability. On the other hand, ALT is a quantitative test used to estimate real-use reliability and may take longer to accomplish.
Leave a Reply