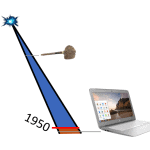
If you had to section the history of reliability into only two periods I believe the dividing point would be around 1950. The first section, stone age to 1950, the “Robust” era; 1950 to today, the “Margin” era. In the robust, era reliability concerns were addressed by creating a design that was orders of magnitude stronger than required, “over-engineered”. This protected against the variability of fabrication, use, and environment. If it was made sloppily with low tolerances, it still worked; Used for an unintended purpose, still worked; Left out in the snow, dropped in the river, run over by a horse, buried in the sand; still worked.
The “over engineering” in the “Robust” era didn’t come at much of an expense to the manufacturer or user. Not many things flew in the air, went fast, or were shipped long distance in bulk. So weight was not much of a design factor. Technology advancement also progressed very slowly compared to today. A simple hand tool could be handed down two or three generations and still be relatively equivalent to what was sold new on the shelf. So, more importantly, it’s need to last, be repairable, and easy to maintain far outweighed any benefits of light weight or inexpensive to manufacture. I have many of my grandfather’s tools. He bought most pre WWII. I was fortunate to receive them because I remember playing with them at his workbench when I was a kid. I would sit there and make up projects that I am sure used (read: ruined) materials he needed and required much cleanup when I decided the sprinklers looked like more fun. If you look at his shears compared to the pair I have in my tool box it is very evident that his were meant to only be replaced if they were lost in the ocean or loaned out to an untrustworthy neighbor. The blades on his are two chunks of steel. All that meat means they can be sharpened thousands of times. They easily come apart for cleaning and removing grit, use them in the sand, who cares. If someone used them to pry two nailed beams together they would do it and then just go back to cutting whatever you wanted.
The blades on my new pair are very thin by comparison. It looks like only the cutting edge is hardened, so sharpening is not something that should be done. No one sharpens stuff today anyway. If you tried to pry apart a nailed piece of wood the tip would probably break off and the hollow handles would bend. There would be little point in me handing down my shears to my kids. They won’t perform well even 10 years from now with light use and a much better design will also be available at that time; power assist with ambient light charging and carbon diamond cutting edge, cost $4. They will still break if you use them to pry wood apart.
Reliability in the “Margin” era is defined by creating very specific strength margins (force, chemical, electrical), then designing and manufacturing exactly to that margin. For the product to be light weight, cheap to manufacture, and efficient, robustness must be minimized. Manufacturing consistency must be very high, there is little margin for variability. Use cases have to be very specifically defined and communicated to the customer. Environmental conditions are to be specifically defined as well with varying life projections based on set cases. This all makes a lot of sense when you consider the product is likely to be thrown away while still in perfectly fine condition. Designing a laptop computer screen that can last 20 years doesn’t make a lot of sense when most people replace their laptop every 5 years.
So the discipline of reliability went from being a simple strategy that did not require much effort to one that is now at the center of the design and manufacturing process. Reliability engineering requires effort and resource that is equivalent to the process of invention and prototyping. The tools available and required are extensive. They include analytical methods that are used before the concept is flushed out to evaluate areas of risk and leverage previous technology/design knowledge. Investigations that result in documented parameters of use, environment, and manufacturing tolerances. Testing programs that measure performance and discover opportunities for improvement. Statistical analysis of data sets to predict trends in field performance and root cause methods to understand the physics of failure so improvements can be made with minimal iterations.
As the rate of advancement of technology continues to increase these methods become even more critical in a standard design process. Development cycles have to be short which means doing it right the first time. Next Gen products to improve existing issues is no longer tolerated. Cost margins are razor thin and heavy R&D investment has to be offset. This means that manufacturing and materials have to be as efficient as possible to ensure the businesses return on investment justifies the endeavor. How ever important you think reliability is to your industry today it’s reasonable to expect it to be twice as critical a factor for product success in the next decade, or less.
How fast is technology moving now?
I recently saw 32Gig thumb drives for $5 at a store. Those plastic hooks you can stick to the wall were down the isle and also $5. How could this be? The process to create that thumb drive is an unbelievable feat of science. The hook was one injected piece of plastic and a piece of double stick tape. More work went into the packaging. The Thumb Drive had almost no value because the design (storage capacity) was over a year old. Sticky hooks will have the same value (about $5) for many years. Any one of those thumb drives not sold in the next month will go in the trash because they need the shelf space. The “Sticky Hook” people have a little more time to improve their process to keep up with technology change. Most of us are not in the “Sticky Hook” business.
-Adam
Leave a Reply