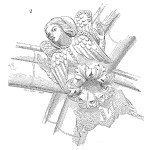
How the 3T’s of Human Error Prevention and Mistake Proofing – Target, Tolerance, Test – were Discovered
Human errors and mistakes cause 80 percent of industrial equipment failures. That humans cause most problems has long been known. It has been difficult to find reliable ways to prevent human error, but an Arab craftsman taught me the 3Ts of error prevention and mistake proofing work.
The Arab weaver in the picture below taught me the 3T’s (Target – Tolerance – Test) of error prevention and mistake proofing. What he was doing in the picture made me think about how truly great quality work is done. I have never met the man. The image is clip art from some public access source. But all the answers to get world class work quality and job task reliability are in that picture.
The weaver has done that job for a long time. He knows how grass weaving is done expertly. He knows what great weaving is. It got me thinking, “What tells him when his work is done right?” How does he know the quality is right as he does each task that creates the woven item? What are his secrets of error prevention and mistake proofing his work?
The questions I’d asked myself held the answer—he knows what quality is and can deliver it with no errors or mistakes. As he works his eyes signal his brain whether the workmanship is right. He knows perfect work when he sees it. He knows when his work is not yet good enough and corrects his actions to bring himself back into the quality workmanship zone that he knows is right.
He must be working to a tight tolerance was my first thought. But I realized from my experience as a fitter-machinist in industry that doing work within specification would not be enough to control his work quality. If he only worked to tolerance limits his results would be random and become a ‘drunkards walk’ from one tolerance limit across to the other tolerance limit and back again. Using specifications alone to control work quality could never guarantee top quality results except by luck. There was something else that the Arab weaver was looking at which let him know that he was right.
The answer came to me soon after realizing that tolerances and specifications alone were not enough to reliably produce quality results. What the Arab weaver was doing was aiming for a perfect result every time he moved his fingers. He had a target in mind and was looking to hit the target dead center every time. He was building quality into every bend and fold because he was seeking perfection in all that he did. Error prevention and mistake proofing were in-built in the way he did each activity. He only used the tolerance points as a limit on his work quality if he was not sufficiently perfect to start with.
And that is how the first two T’s of the 3T’s was arrived at—a Target is needed if one is to achieve perfect quality, and a Tolerance is used to tell when you have strayed too far off-target to still call it a high quality result.
But using a Target and a Tolerance did not prevent failure from human error. Target and Tolerance gave direction and guidance on achieving quality performance, but it did not stop mistakes happening. Still more was needed to explain how the Arab weaver was a total master of his craft.
I decided to look at the weaving from the perspective of the Arab weaver. I imagined I was seeing what he saw through his eyes. As each frond was being folded what was he looking for? What signals was his brain processing that told him that a bend or fold was in the right place, that it would fit with what was to happen next, that it would be an ideal part of a fine quality job?
Again it did not take me long to realize what must be happening. The Arab was using his eyes as measuring devices. With his eyes he was measuring how far from perfection he was working. With every fold the craftsman saw if it was perfect or not. He tested everything he did against the perfect result and made subconscious adjustments when he wandered to close to the tolerance limits. Now the third T of the 3T’s had made itself clear to me—there must be a proof Test for every single activity to confirm it is right BEFORE doing the next activity. In this way you would immediately spot an error and fix it.
A couple of years after I thought that I had discovered the 3T’s I learnt that W. Edwards Deming, the late quality guru credited with starting the Japanese quality revolution, along with others of his caliber, had already seen the same thing. On page 220 in the second edition of The New Economics is a plot that proves working to tolerance limits alone does not deliver quality results, in fact it increases wastes and costs. The first two T’s were vindicated in Deming’s last book.
The third T had already been vindicated in Deming’s other famous book, Out of the Crisis. On pages 422 Deming discusses using parallel computation by two people of different copies of the same document. By doing so you reduce document error rates by 1000 times. On page 434 he discusses component redundancy, in which duplicate parts are put in parallel. Once two things act in parallel, where each one can do the whole job should the other fail, you create a highly reliable system, far more reliable than each part alone. The third T (Test) is a redundant proof-test activity to check if the original fold of a leaf was in fact right. By doing a measuring test on the first activity you apply parallel inspection and cause error rates to fall by hundreds and thousands of times.
This YouTube video takes you into greater details about the ACE 3T error prevention and mistake proofing method and how to apply it in standard operating procedures: The Value Gained by an Accuracy Controlled Enterprise Using 3T in SOPs (19 min 16 sec)
I needed a new name for what I had stumbled onto with the unknown Arab craftsman’s help. The name had to reflect what the 3T process of Target-Tolerance-Test was about. Especially what it delivered to companies that used it. The method was a sure way to produce any degree of quality one desires because it had an in-built method to produce amazing repeatability through error prevention and mistake proofing.
In the end, the Accuracy Controlled Enterprise was the title I settled on. The acronym was ACE, which was a great word to have, as ACE could be used to distinguish great companies from the average company. ACE could also mean Accuracy Controlled Employee, and that was a great name to use to label your best people.
The whole process of discovering the 3T’s and inventing ACE error prevention and mistake proofing took about two days. But it was the Arab craftsman who first made me stop and think about what must be going on in his head. The recognition of the Target was the crux. After that it was clear what must be done to get world class quality performance in anything you do.
IN THE PAST SKILLS WERE MASTERED BY KNOWING WHAT WAS CORRECT
There were no written instructions on how to do a job right before the printing press was invented. Before it was compulsory that people go to school and learn to read you had to know and memories how do top quality work. Before there was the printed word Quality workmanship was imbedded into your mind until it was naturally expressed through your efforts and handiwork. A skilled craftsman could make a thing of great quality because they had mastered the methods and techniques. Centuries ago Quality was practiced until it became a habit that you lived by. Today we suffer from poor work quality and poor repeatability because these days quality is written into a procedure; it no longer lives within our hearts and minds as it did in the craftsmen of old.
My best regards to you,
Mike Sondalini
Leave a Reply