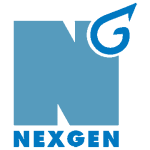
In the dynamic world of modern manufacturing and industrial processes, the reliability and performance of equipment play a crucial role in ensuring operational efficiency and product quality. Dosing pumps, essential for precise fluid control, are no exception. As industries increasingly embrace digital transformation, predictive analytics has emerged as a powerful tool to enhance the monitoring and maintenance of dosing pumps. This article delves into how predictive analytics can be used to monitor dosing pump performance, improving reliability, efficiency, and cost-effectiveness.
Understanding Dosing Pumps
Dosing pumps are specialized devices designed to deliver accurate and controlled amounts of fluid, such as chemicals, additives, or medications, into a process or system. They are widely used in industries including pharmaceuticals, food and beverage, water treatment, and chemical manufacturing. The precision and consistency of modern dosing pumps are critical to maintaining the integrity of these processes, making their reliable operation paramount.
The Role of Predictive Analytics
Predictive analytics involves using historical data, statistical algorithms, and machine learning techniques to identify patterns and predict future outcomes. When applied to the monitoring of dosing pump performance, predictive analytics can provide actionable insights that help prevent equipment failures, optimize maintenance schedules, and improve overall operational efficiency.
Key Components of Predictive Analytics for Dosing Pumps
Data Collection
The foundation of predictive analytics is data. For dosing pumps, this includes data from sensors that monitor parameters such as pressure, flow rate, temperature, and vibration. Additionally, maintenance records, operating conditions, and historical performance data are essential inputs.
Data Integration
Integrating data from various sources into a unified platform is crucial. This may involve connecting sensors, maintenance management systems, and enterprise resource planning (ERP) systems to create a comprehensive dataset for analysis.
Data Processing and Cleaning
Raw data must be processed and cleaned to ensure accuracy and reliability. This involves filtering out noise, handling missing values, and normalizing the data to create a consistent and usable dataset.
Model Development
Machine learning models are developed to analyze the data and identify patterns. These models can range from simple regression models to complex neural networks, depending on the complexity of the data and the desired outcomes.
Predictive Maintenance Algorithms
Algorithms are designed to predict when a dosing pump is likely to fail or require maintenance. These algorithms use historical data and real-time sensor inputs to generate predictive insights.
Visualization and Reporting
The results of the predictive analytics are presented through dashboards and reports. Visualizations such as graphs, charts, and heatmaps help operators and maintenance teams quickly understand the current status and future performance of dosing pumps.
Benefits of Predictive Analytics for Dosing Pumps
The application of predictive analytics to dosing pump monitoring offers numerous benefits:
- Increased Reliability: Predictive analytics helps identify potential issues before they lead to pump failures. This proactive approach reduces unplanned downtime and ensures consistent operation.
- Optimized Maintenance: Traditional maintenance schedules are often based on fixed intervals or reactive responses to failures. Predictive analytics allows for condition-based maintenance, where actions are taken based on the actual condition of the pump, reducing unnecessary maintenance and extending equipment lifespan.
- Cost Savings: By preventing unexpected breakdowns and optimizing maintenance schedules, predictive analytics reduces maintenance costs and minimizes production losses. The ability to forecast spare parts requirements also helps manage inventory more efficiently.
- Improved Performance: Continuous monitoring and analysis of dosing pump performance lead to better understanding and optimization of operating parameters. This results in enhanced precision, efficiency, and overall system performance.
- Enhanced Safety: Early detection of potential failures and anomalies contributes to safer operations, especially in industries where dosing pumps handle hazardous or critical fluids.
Practical Applications of Predictive Analytics in Dosing Pump Monitoring
To illustrate the practical applications of predictive analytics in dosing pump monitoring, let’s explore a few real-world scenarios:
Chemical Manufacturing
In chemical manufacturing, dosing pumps are used to precisely add chemicals to processes such as reactions, blending, and treatment. Predictive analytics can monitor parameters like flow rate, pressure, and temperature to identify signs of wear and potential failures. By predicting pump degradation, maintenance can be scheduled during planned downtime, avoiding costly interruptions.
Water Treatment
Water treatment plants rely on dosing pumps to add coagulants, disinfectants, and other chemicals to ensure safe and clean water. Predictive analytics can analyze data from sensors monitoring flow rates, pump vibrations, and chemical levels. Anomalies in these parameters can indicate issues such as clogging, seal wear, or cavitation, allowing for timely intervention and maintenance.
Pharmaceutical Manufacturing
Pharmaceutical manufacturing requires precise dosing of ingredients to ensure product quality and compliance with regulations. Predictive analytics can monitor dosing pumps for deviations in flow rates and pressure, which could indicate calibration drift or mechanical issues. Early detection of these anomalies helps maintain the integrity of pharmaceutical products and avoid costly recalls.
Challenges and Considerations
While the benefits of predictive analytics for dosing pump monitoring are significant, there are several challenges and considerations to keep in mind:
- Data Quality: The accuracy and reliability of predictive analytics depend on the quality of the data collected. Inaccurate or incomplete data can lead to incorrect predictions and ineffective maintenance strategies.
- Integration Complexity: Integrating data from multiple sources and ensuring compatibility with existing systems can be complex and time-consuming. A well-planned integration strategy is essential to overcome these challenges.
- Model Accuracy: Developing accurate predictive models requires expertise in data science and domain knowledge of dosing pumps. Regular updates and validation of models are necessary to ensure their reliability and effectiveness.
- Change Management: Implementing predictive analytics in an organization requires changes in workflows, processes, and culture. Training and support are essential to help staff adapt to new technologies and methodologies.
- Security and Privacy: Ensuring the security and privacy of data is critical, especially in industries handling sensitive information. Robust cybersecurity measures must be in place to protect data integrity and prevent unauthorized access.
Future Trends in Predictive Analytics for Dosing Pumps
As technology continues to evolve, several future trends are expected to shape the landscape of predictive analytics for dosing pump monitoring:
- Artificial Intelligence and Machine Learning: Advancements in AI and machine learning will enhance the accuracy and capabilities of predictive models. These technologies will enable more sophisticated analysis and real-time decision-making.
- Edge Computing: Edge computing involves processing data closer to the source, reducing latency and improving real-time monitoring. This trend will enable faster and more efficient predictive analytics for dosing pumps.
- IoT Integration: The Internet of Things (IoT) will play a crucial role in predictive analytics by providing seamless connectivity and data exchange between sensors, pumps, and analytics platforms. This integration will enhance data collection and analysis.
- Augmented Reality (AR) and Virtual Reality (VR): AR and VR technologies can provide immersive visualization of dosing pump performance and predictive insights. Maintenance teams can use AR glasses to view real-time data and receive step-by-step instructions for repairs.
- Blockchain for Data Security: Blockchain technology can enhance data security and integrity by creating tamper-proof records of dosing pump performance and maintenance activities. This will build trust and transparency in predictive analytics systems.
Conclusion
Predictive analytics is revolutionizing the way dosing pumps are monitored and maintained in various industries. By leveraging data, advanced algorithms, and machine learning, predictive analytics enables proactive maintenance, reduces downtime, and enhances the reliability and performance of dosing pumps. While there are challenges to overcome, the benefits far outweigh the risks, making predictive analytics an essential tool for modern industrial operations. As technology continues to advance, the future of predictive analytics for dosing pump monitoring looks promising, with even greater improvements and innovations on the horizon.
Insightful. I’d love to see more content on the “how to’s” implementing predictive maintenance strategies.