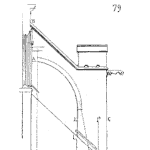
It is not enough to simply state your organization has a proactive stance concerning reliability. It more than running a few tests or thinking about reliability before the product ships or the equipment is installed.
It is a way of doing business.
A reactive stance is taking action when required since something failed.
We respond to the failure and generally do all the right things to solve the issue. We even may include steps to minimize or avoid the same failure with other products. That is not proactive.
A proactive reliability program involved reliability in many more decisions before a failure occurs. The proactive organization uses ever means possible to find and understand what could fail. This organization is not surprised by failures, they expect the failures that occur. It may or may not be ecumenical to rush to solve an issue as it’s been thought out in the customer and business context before.
Sure a proactive organization may miss something and a customer failure is a surprise which requires a reactive response. Since this is rare there are resources available I.e. Not working on many other surprises. The response not only addresses the issue, minimizes the impact on the other product, it also looks at the development process to find and correct the process.
Steps to Create a Proactive Reliability Program
First, stop waiting to find failure in due course. Aggressively and early in the program ferret out faults, weaknesses, and potential problems. Find and resolve them early. Defining clear reliability goals, completely, permits identifying how failure may appear.
Second, fully explore what could fail. This includes materials, supplied parts, assembly processes, use stresses, and customer expectations. A single prototype failure is gold — it has information the permits you and team to prevent that issue from occurring for customers. Treat it as treasure. Characterize, not qualify.
Third, include reliability in every decision. Enable the entire team to balance reliability performance alongside time to market, cost, and functionality. Everyone should know how to convert a failure rate to dollars. Everyone should know when it is worth delaying a launch to improve the reliability.
Forth, reward reliability thinking equal to rewarding meeting time to market business objectives. If the business decisions do not include reliability in a clear and rational manner, saying the organization has a proactive reliability program is little more than a banner on the wall. Expect, encourage, and celebrate those in the organization that truly consider reliability in making decisions. Considering reliability means having the ability and information to balance the long term impacts of the decision between cost, time to market, functionality, and reliability on an equal footing. This may take changing bonus, promotions, and reward systems.
Summary
A proactive reliability program means many discussions include reliability aspects — not just mention reliability is important and move on. In fact gather and use reliability information (estimates, predictions, models, studies, tests, and data) just as when considering the potential market and estimates sales, to make decisions.
You know you have a proactive reliability program when you are rarely surprised by failures reported by customers. It also means the organization’s total investment in reliability activities goes down, as your team only does the studies and tests that provide value.
If you run a program that includes many steps and endless qualification tests, and you spend a significant amount of time responding to failures, you do not have a proactive program.
Take a look at how decisions are made and the reliability information used to make those decisions. If the current process is not producing the results you desire, change something. Start today making better decisions.
Fred,
This article on proactive reliability struck a chord with me. In the power industry, a power plant engineer deals with the reliability of thousands of components bought on a ‘best evaluated bid’ basis often decades ago. Design, operation and maintenance all factor into long term reliability. I wish that every product proposal came with a list of possible failure modes and consequences of a failure. I wish the vendors instruction manuals came with care and feeding instructions on how to avoid or mitigate failures for critical components. The challenge with reliability centered maintenance is determining what you know and don’t know about an equipment component’s life cycle and being proactive under the tyranny of reactive forces such as day-ahead market pressures. It’s a real challenge to manage for the long haul when there is so much short term thinking. Thank you for the reminder to reward reliability thinking.
Thanks for the comment Gene, and yes, short term may feel urgent, and we need to focus on what is important.
Cheers,
Fred