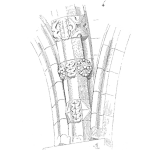
To get world class operation and profits your Asset Lifecycle Management System must prevent every opportunity for defect-creation in all life cycle phases, for all your operating equipment
Every physical asset has a lifecycle starting at conception through to its eventual disposal and site remediation. In each phase of the lifecycle errors can occur that cause defects within the asset. In operations with hundreds of assets there easily can be tens-of-thousands of defects. Each defect is a risk that eventually contributes to breakdowns, losses, wastes, safety incidents during operation, and shortens the asset’s service lifetime. Eliminating thousands of defects and risks forever is what Plant Wellness Way EAM does for its users.
As shown in the slide below, every asset begins the same way – with the Idea Creation phase. This is when the idea for an asset is first formed in someone’s mind. The next phase is Feasibility, which is when the idea is determined to be viable. This is followed by a Preliminary Design that can be used for budget estimations. Then it next goes for Financial Approval to undertake the project of creating the asset. If successful, the asset project will be developed into a Detailed Engineering Design, which informs the Procurement phase. Once the procurement arrives, the asset is then installed during Construction phase. Finally it is ready for Commissioning, and to be handed over for Operation. Once the asset is no longer viable to maintain, or the technology is outdated, it will be Decommissioned and Disposed of. There are 11 sequential phases, forming a series process for every asset life-cycle.
As you can see, the each phase is in series and makes process success dependent on the previous phase being completed well. If something is missed in the Procurement phase, then Construction will take much longer and be more expensive. Small errors in details in one phase become magnified in others. So a slightly off measurement or calculation in the Detailed Engineering Design phase can have extreme effects for the successful and smooth Operation of the asset.
Because the engineering asset lifecycle is a series arrangement, where one phase leads to the next until the entire lifecycle is complete, there are many risks across an asset’s lifecycle to its operational success. Every error made in any phase is transferred through to all future stages. The errors sit within the engineering assets as defects. In operation these errors can turn into breakdowns and safety incidents. If the defects are found and corrected before the asset enters operation, then no harm is carried into its operation. However, if the defects remain they each cause operational risks during service lifetime, and contribute to seemingly random production equipment stoppages.
An error prevented or corrected is a defect eliminated. Asset lifecycle management is a key purpose of a Plant Wellness Way EAM system-of-reliability. It ensures companies have engineering asset lifecycle management methods and practices that prevent errors and mistakes at every phase of the lifecycle. Plant Wellness Way EAM brings error-prevention and defect elimination to all stages of every engineering asset’s lifecycle so defects are eliminated and zero-failures are normal.
This slide is a companion to the new Industrial and Manufacturing Wellness book. The book has extensive information, all the necessary templates, and useful examples of how to design and build your own Plant Wellness Way enterprise asset life cycle management system-of-reliability. Links to purchase the book are provided below.
Leave a Reply