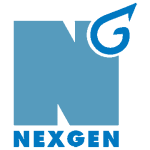
In the intricate landscape of modern manufacturing, the efficiency and quality of the production system are paramount. These two pillars underpin a company’s competitiveness, profitability, and customer satisfaction. A critical factor influencing these metrics is the maintenance strategy employed. This research delves into the profound impact of maintenance strategies on production efficiency and quality, exploring various approaches, their implications, and real-world case studies.
Maintenance Strategies: A Comparative Overview
Maintenance strategies can be broadly categorized into 4 primary types of maintenance strategy:
- Corrective Maintenance: This reactive approach involves repairing or replacing equipment only when it fails. While it reduces upfront costs, it can lead to unexpected downtime, increased operational expenses, and potential damage to other components.
- Preventive Maintenance: A proactive strategy aimed at preventing equipment failures through scheduled inspections, cleaning, and lubrication. It helps reduce unplanned downtime and extend equipment life but can be costly and time-consuming.
- Predictive Maintenance: A data-driven approach that utilizes sensors and analytics to monitor equipment health and predict potential failures. This enables timely interventions, minimizing downtime and optimizing resource allocation.
- Condition-Based Maintenance: Similar to predictive maintenance, condition-based maintenance relies on monitoring equipment performance parameters to determine the need for maintenance. However, it is often more flexible and responsive to real-time conditions.
The Impact of Maintenance Strategies on Efficiency
Efficiency, measured by factors such as overall equipment effectiveness (OEE) and production throughput, is a cornerstone of a successful manufacturing operation. The choice of maintenance strategy significantly influences efficiency:
- Corrective Maintenance: While initially cost-effective, corrective maintenance can lead to frequent unplanned downtime, disrupting production schedules and reducing overall efficiency.
- Preventive Maintenance: By preventing failures, preventive maintenance can improve efficiency and reduce downtime. However, it may result in overmaintenance, leading to unnecessary costs and resource consumption.
- Predictive and Condition-Based Maintenance: These data-driven approaches offer the greatest potential for efficiency gains. By targeting maintenance efforts only when necessary, they minimize downtime and optimize resource utilization.
Case Study: A Manufacturing Plant’s Transformation
A leading automotive manufacturer faced challenges with frequent equipment breakdowns and inconsistent product quality. By transitioning from a corrective maintenance strategy to a predictive maintenance approach, the company achieved significant improvements:
- Reduced Downtime: Predictive maintenance enabled early detection of potential failures, allowing for timely repairs and reducing unplanned downtime by 30%.
- Improved Quality: Consistent equipment performance led to a 15% reduction in product defects.
- Optimized Resource Allocation: Data-driven insights helped the company allocate maintenance resources more effectively, resulting in a 10% reduction in maintenance costs.
The Impact of Maintenance Strategies on Quality
Product quality is a critical determinant of customer satisfaction and market competitiveness. The maintenance strategy plays a vital role in ensuring consistent quality:
- Corrective Maintenance: Frequent equipment failures can lead to variations in product quality, as equipment performance may deteriorate over time.
- Preventive Maintenance: Regular inspections and maintenance can help maintain equipment performance and reduce the likelihood of quality issues.
- Predictive and Condition-Based Maintenance: By preventing failures and addressing potential issues before they impact production, these strategies can significantly improve product quality.
Integrating Maintenance Strategies for Optimal Results
In many cases, a combination of maintenance strategies can provide the most effective approach. For example, a company might use preventive maintenance for routine tasks while employing predictive maintenance for critical equipment. This integrated approach can help balance the benefits of proactive maintenance with the cost-effectiveness of reactive maintenance.
Emerging Trends in Maintenance
The field of maintenance is rapidly evolving, driven by technological advancements and changing business requirements. Some emerging trends include:
- Industry 4.0: The integration of digital technologies, such as IoT and artificial intelligence, is transforming maintenance practices. Predictive analytics, condition monitoring, and remote diagnostics are becoming increasingly prevalent.
- Reliability-Centered Maintenance (RCM): RCM focuses on identifying the critical functions of equipment and determining the most effective maintenance tasks to ensure those functions are performed reliably.
- Total Productive Maintenance (TPM): TPM involves a collaborative approach that engages all employees in improving equipment reliability and reducing waste.
Conclusion
The choice of maintenance strategy has a profound impact on the efficiency and quality of the production system. While corrective maintenance can be cost-effective in the short term, proactive strategies such as preventive, predictive, and condition-based maintenance offer greater potential for long-term benefits. By carefully considering the specific needs of their operations, manufacturers can select or combine maintenance strategies to optimize efficiency, quality, and overall competitiveness.
Leave a Reply