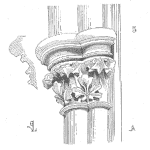
There are three things that can happen when a non-conforming part appears on the production line.
(1) The part is immediately rejected and never makes it into an assembly.
That’s good, but the additional handling of the part is a waste of time and resources.
(2) The part is added to an assembly, but the assembly fails an inspection or tests further down the line. This adds more cost for rework and re-testing.
(3) The part is added to the assembly, isn’t caught by downstream testing and the product ships to a customer. Now it’s a bigger problem, depending on what characteristic of the part doesn’t meet requirements.
This could be a latent problem that will eventually cause the product to fail, leading to a return and an unhappy customer.
Prevent having bad parts
Regardless of whether they’re caught or not, bad parts add cost and reduce productivity, and it should be a high priority at any factory to prevent bad parts from making it to the line.
Unfortunately, many quality teams put too much emphasis on incoming inspection instead of supplier management. You’ve heard this before: you don’t get quality from testing (or inspection).
Shifting the burden to the supplier by insisting on outgoing inspection on their side is a step in the right direction, but the idea is not just to prevent bad parts from entering the factory; the idea is to prevent bad parts from being built in the first place.
Easier said than done?
It seems to me there are two general ways to achieve that goal.
You can take an adversarial position with the supplier, starting by complaining about poor quality. You can make future business contingent on demonstrated improvement.
I’ve always advocated for financial penalties to suppliers, at least compensating for the additional inspection and rework in the factory.
Regardless, this is basically saying to the supplier: “Quality is your problem. Figure out how to fix it, or there will be consequences.”
Or, you can say: “Quality is our shared problem. How can we fix this together?”
Help your supplier
The supplier may have a limited understanding of how to manage their internal processes in order to ensure conformance, and they may need your help to analyze the situation.
When a product’s critical performance parameters are in-spec, that’s ultimately the result of effective control of critical process parameters.
Has the supplier demonstrated process capability? Should the spec limits be relaxed because they’re too difficult to maintain? Are process outputs measured, and are they within control limits?
Does the supplier know what process inputs and parameters must be managed to produce consistent output?
All of these questions should be part of a supplier audit program.
If the supplier isn’t capable or is otherwise unwilling to participate in defect prevention strategies, it’s time to think about changing suppliers.
Related:
What to Specify with Suppliers to Achieve Reliability Goals (article)
How to Assess Your Reliability Program (article)
Reliability Questions to Ask Your Suppliers (article)
Leave a Reply