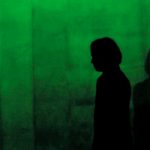
Many product development teams use a contract manufacturer (CM) to develop and manufacture their product. It’s the “develop” term that has limitations that may be unforeseen when engaging. Many companies use the CM to assist or even eventually entirely execute the product development. This can have great results or be problematic. But let’s talk about the arrangements that work well. Troublesome CM’s are a topic for a different time.
For a company heavily engaged with a CM in the design process an interest in improving reliability may be challenging. They may discover that they don’t have a lot of knowledge or control of the details of the design. What are the materials used? What is being controlled in manufacturing and how much? To improve reliability, or even start a program from scratch, it is important to be able to characterize many aspects of the product and the variabilities that exist. Reliability is the “study of product response to variability.” Variability to environment, variability to use, and variability in manufacturing.
The first step is to investigate how well the CM can be included in this initiative. By having them contribute to the design process they are an official part of the reliability team. Create the following check list of information to gather before starting the reliability initiative
- What is the reliability goal and what is driving it?
- Will there be any feature adds to the product in the improved reliability revision?
- Who controls the variabilities of design features and manufacturing controls? Are you sure?
- What studies have been completed on “use-cases” and “environment”?
The key is having these discussions with the CM so they can contribute as designers, researching what info exists and doing all of this up front.
-Adam
Leave a Reply