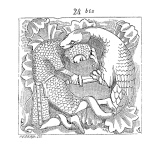
Successful Wind Turbine Reliability Strategy Requires Proactive Removal of the Causes of Failure
The reliability assessment of wind turbine models is critical when making investment in wind technology. Issues to address include: corrosion, metallurgy, structural integrity, reliability, pressure vessel construction, electrical circuits, communication networks, and more.
Develop a life cycle wind turbine reliability strategy that minimizes operationg costs by maximizing component reliability.
Wind turbines with gearbox drives are renown for their poor reliability. Their mechanical complexity explains why failures and mechanical problems arise in such machines.
Meeting 20% of America’s electric power needs may require 100,000 or more individual wind turbines. Each turbine is a complex electromechanical system with a nominal design life of 20 years. In reality, however:
- actual operating life is generally less than 10 years,
- owners and manufacturers are hesitant to share reliability performance data,
- Operating and maintenance (O&M) costs are both site and model specific,
- a given model turbine may have 100 or more combinations of blades, generators, gear boxes and yaw systems from different manufacturers that produces confusion and complexity, and
- few reliability statistics are available on these individual components let alone the overall wind turbine system.
Wind energy will not become a mature power generation industry without an understanding of both component and system reliability and the relationship between reliability and O&M costs. Reliability studies must be conducted to:
- make meaningful predictions about post warranty O&M costs,
- determine the value of existing wind farms for acquisition investors, and
- establish the long term viability of wind energy for the American power grid
As part of any wind energy project investment you ought to develop a wind turbine reliability strategy that reduces the wind energy project financial risk from operational problems like wind turbine failure. They use an proprietary operational risk reduction methodology — like our proprietary Plant Wellness Way — to analyse operational risks, identify their causes, and develop preventive measures that protect your wind farm project investment. You get drastically improved wind turbine reliability when wind turbine reliability solutions are developed proactively. Using operational risk abatement methodology like the the Plant Wellness Way generates more future profits.
Strategies for Greatly Improving Wind Turbine Reliability
Wind turbine failures are primarily of mechanical assemblies. The inverter, PLC and overall wind turbine electrical system are fairly sophisticated and reliable. Steps to improve wind turbine reliability through implementing Plant and Equipment Wellness operational asset management would include the following items:
- Determine the ‘Structural Importance’ of each mechanical component. This measures the importance of the position of the component. It is independent of the reliability value of the component under consideration and also independent of the reliability of every other component. High reliability components should be allocated to positions with high structural importance.
- Assess the feasibility of increasing the reliability of the most unreliable components.
- Create redundancy for components having the highest structural importance and/or lowest reliability. Redundancy is most effective when applied at the lowest level in a hierarchical system. Component redundancy is always more effective than subsystem redundancy.
- Build accessibility for quick maintenance into the wind turbine design. The Mean Time To Repair (MTTR) is significant for many mechanical components resulting in low wind turbine availability due to long maintenance outage times.
- Seek to minimize construction defects. Wind turbines are usually erected by a contractor hired by the developer and not by the turbine Original Equipment Manufacturer (OEM).
- Seek to minimize the number of different vendor sources for a given component and remove fabrication variation and errors.
A specialist wind turbine reliability strategy targets your platform-specific system reliability. They look at how best to maximise your wind turbine service life by using component life data, system block diagrams and fault tree analysis of your turbine model.
We can provide you technical assessments of engineering specifications with regard to codes, standards and best practices, for the technology areas impacting wind turnine reliability. The technology areas to investigate include: corrosion, metallurgy, structural integrity, reliability, pressure vessel construction, electrical circuits, communication networks, and several others that are equally important.
All the best to you,
Mike Sondalini
Director
Lifetime Reliability Solutions HQ
Leave a Reply