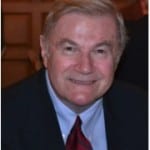
Guest Post by John Ayers (first posted on CERM ® RISK INSIGHTS – reposted here with permission)
Today with robotic development, digital transformation, Artificial Intelligence, and other projects t will involve a multi-discipline team with many interfaces. To keep budget and schedule on these types of projects, inputs and outputs from all disciplines must be accurate, complete and timely. If not, your project will be risk.
All tasks (Work Packages) have a manager. Inputs from another task manager to start your task is your supplier. Output from your task goes to another task manager. In this case you become a customer. Every task manager is a supplier and a customer.
Based on my experience, the majority of project managers do not think in terms of internal suppliers and customers. They are very familiar with external suppliers but until you draw their attention to internal suppliers, they are obvious to it. This paper focuses on a task supplier but also applies to a task customer.
Poor performance from an internal supplier can result in high risk for the task and ultimately the project. The four major risk areas are:
- Productivity
- Schedule
- Budget
- Morale and trust
This paper discusses the risks and suggests a couple of corrective actions to consider to mitigate the risk.
Productivity
To be successful with a task and project, it is essential that the input from your internal supplier be delivered on time, is incomplete, good poor quality, and does not have to be redone several times before acceptable.
In many (if not the majority) of cases, input requirements by internal customers are not clear, have an unrealistic time line, and must be done over. –’I didn’t want that. I wanted this. Re-do it.’-approach. This is unacceptable and is a risk to the project.
Schedule
Late input from the internal supplier most likely will cause a delay in the task completion. Late input will cause time longer to complete a design, generate a specification, Statement of Work (SOW), or meet a milestone because -’I didn’t receive inputs from Mechanical Engineering (ME), Electrical Engineering (EE)’ or another internal supplier. This situation usually results in late tasks and potential impact to your project.
Budget
Task budgets are based on timely, complete, and quality inputs? How does a task meet a budget if the input from the internal supplier is incomplete, late, and poor quality? If this happens, the choice is to slip the task schedule or use more resources than planned to maintain the task budget both actions will potentially impact the project budget and schedule. Typically, if the schedule slips the costs increase impacting the budget. As a result, the risk of budget growth above the project plan will be high.
Moral and trust
As an example, to explain this risk, you can never get inputs from Bill and when you do it is poor quality. You end up calling his boss to get it done making you look like the bad guy. Bill gets recognition for meeting his goals but he is impacting your task making you look bad. No one seems to realize Bill is a poor supplier and is hurting the project. Sound familiar?
Risk Mitigation Suggestions
- Develop an Internal Supplier Performance Measurement System
The system would involve the creation of an electronic discrete, user friendly quantitative measurement system for internal suppliers (and customers). It will provide to the Project Manager, Engineering Managers, Department Managers and other managers a data base for rewards and recognition for outstanding supplier performance for task managers. Once implemented, the system should result in improved productivity, budget, and schedule performance for your project. Team morale and trust should increase measurably due to high expectations by internal suppliers and customers that their needs will be met on time, with high quality, and the first time around.
Example of a Supplier Measurement System
The following example came from an external customer but the approach used can be the frame work for developing and internal supplier system.
A large defense company implemented a quantitative measurement system for their supplier base which worked well for them They set up measurement parameters some of which are listed below:
- Input delivery schedule
- Completeness
- Accuracy
- Number of times sent back for corrections
Each parameter was rated with a number (say 1-10). The rating for each supplier was calculated from the parameter values using an algorithm that weighted the importance of one to the other. Minimum accepted thresholds were established. If a supplier fell below the thresholds, they would receive notification automatically notifying them they could not deliver any more product until an approved recovery action plan was in place. Face-face meetings with the suppliers were held to work with them in getting the rating up above the threshold. Suppliers with ratings above the threshold were recognized for excellence performance. Maintenance and operation of the system took minimal time but it did motivate their suppliers to pay attention to quality deliveries.
- Work Breakdown Structure (WBS) Dictionary
A WBS dictionary defines each Work Package (WP) or task. It is essential to good project performance. The reason being, it includes the items listed below which includes all of the information that is needed to manage the WP.
A WBS dictionary WP definition includes the following items:
- Proposal WP number.
- BOE reference.
- The proposal SOW paragraph.
- WP charge number.
- WPM name.
- WP name
- WP task description to include:
- Task input.
- Task definition.
- EV technique.
- Task output.
The figure below shows an example of a WBS dictionary for the Design WP which is part of the Gas Turbine/Generator System. I want to focus on the task input and output.
The input required to start the task is the concept, design requirements, budget, and schedule. If the Work Package manager (WPM) does not receive these items on time, is complete and inaccurate, then the task will start late and possibly become a risk to the project.
The output required to complete the task (and WP) comprises release of all final documentation to configuration Management (CM). If the input is late, then the output will be late and impact the user of the final documentation. In this case, the users may be manufacturing or subcontracts management because they will need final documentation to perform their tasks.
The other point to make is the WBS dictionaries are accessible to all team members. So, there should be no excuses as to what and where the required input for the task input comes from.
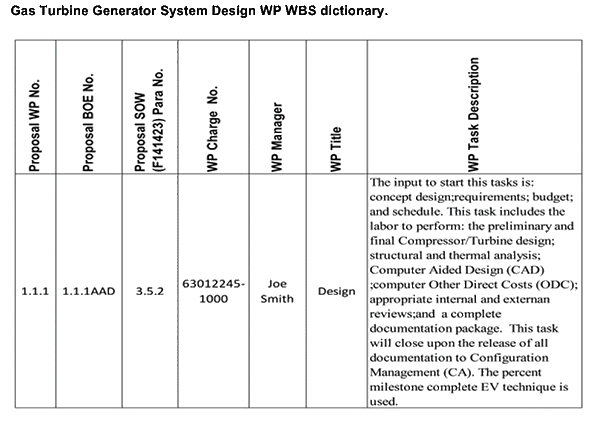
Summary
Internal supplier performance can make or break your project. Poor performance from them is a high risk to the success of the project. The suppliers are in-house assets. This means the project manager, Department Mangers, Engineering Managers and other management levels in the company have total control over the internal suppliers. There is no excuse for accepting poor performance except acknowledging the problem and putting into place new systems or procedures to measure the supplier performance, correct their poor performance as it becomes apparent, and giving credit to the excellent suppliers.
To mitigate the poor performing internal suppliers’ serious consideration should be to using a WBS Dictionary for every task. Ensure the inputs and out puts are well defined. Meet with the team to review the WBS Dictionaries to ensure they understand who and where input is coming from for their task. Also review the outputs with the team and emphasize the importance of providing the output as complete, accurate, and on schedule.
The key to success on a project is how well you manage the tasks (WPs). If they are managed well in terms of delivering accurate, complete and on schedule output, the project will do very well. Conversely, if they are managed poorly the project most likely will not do well
Bio:
Currently John Ayers is an author, writer, and consultant. He authored a book entitled Project Risk Management. It went on sale on Amazon in August 2019. He authored a second book entitled How to Get a Project Management Job: Future of Work. It is on sale on Amazon. The first is a text book that includes all of the technical information you will need to become a Project Manager (PM). The second book shows you how to get a PM job. Between the two, you have the secret sauce to succeed. There are links to both books on his website. https://projectriskmanagement.info/He has presented numerous Webinars on project risk management to PMI. He writes columns on project risk management for CERM (certified enterprise risk management). John also writes blogs for Association for Project Management (APM) in the UK. He has conducted a podcast on project risk management. John has published numerous papers on project risk management and project management on LinkedIn. John also hosts the Project Manager Coach club on clubhouse.com.
John earned a BS in Mechanical Engineering and MS in Engineering Management from Northeastern University. He has extensive experience with commercial and U.S. DOD companies. He is a member of the Project Management Institute (PMI. John has managed numerous large high technical development programs worth in excessive of $100M. He has extensive subcontract management experience domestically and foreign. John has held a number of positions over his career including: Director of Programs; Director of Operations; Program Manager; Project Engineer; Engineering Manager; and Design Engineer. He has experience with: design; manufacturing; test; integration; subcontract management; contracts; project management; risk management; and quality control. John is a certified six sigma specialist, and certified to level 2 Earned Value Management (EVM).
Go to his website above to find links to his books on Amazon and dozens of articles he has written on project and project risk management.
Leave a Reply