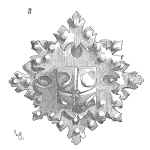
Between 1670 and 1700, the Royal Navy installed lead sheets over the hulls of some ships to help preserve them and reduce repairs. (See Failure Modes of Lead Hull Sheathing Explored by the Royal Navy.) Galvanic corrosion attacked the iron bolts holding the hull and rudder together, so the program had to be canceled.
The British reverted to their previous practice of installing thin wood sheathing on top of the main hull. The wood sheathing was sacrificial and had to be replaced every few years. When the sheathing was stripped for replacement, inspection and repair of the main hull was accomplished.
Replacing sheathing was frequent, tedious, and time consuming. The ship had to be beached or rolled on its side. Historian Peter Goodwin recorded the many steps required to properly sheathe a hull from letters written in 1727. The details include specific requirements for material types, dimensions, and accuracy in assembly. In a 1851 history of naval architecture, John Fincham related experiments to determine which compositions of tar and pitch were most effective on wood sheathing. A standard mix was selected by 1737.
In 1708, there was a proposal to sheathe Royal Navy ships with copper. It contained an explicit promise to prevent the maintenance and repair of wood sheathing.
‘‘…your petitioners have, with great industry and charge, invented a new method
of sheathing ships with British copper, which without hindrance to their sailing will
preserve them from worms and barnacles in voyages to the East and West Indies, and
prevent all occasion of careening and repairing them, which the common sheathing
frequently requires.” (Goodwin, Harris)
The navy rejected the idea because of the cost of maintaining the sheathing. Within a few years, internal proposals were being made to sheathe the gates of drydocks with copper to prevent shipworm damage.
The Royal Navy was not the first to use copper sheathing. The Dutch East India Company sporadically used copper sheathing, with the earliest evidence from a 1606 shipwreck. (Van Duivenvoorde) The first full-ship coverage occurred in 1620, but this was an abnormality, subject to the whim of an individual admiral. Examining multiple Dutch company and naval shipwrecks spanning 1606 to 1778 led van Duivenvoorde to conclude that the Dutch use of copper hull sheathing was not standard for the organization. Dutch copper sheathing was subject to regional custom and experimentation by individual shipbuilders. Limited use of lead or copper by the Dutch improved their maintenance burden somewhat, but it was not the result of a management system intentionally planning for an asset’s life cycle.
![The bow of an early 19th-Century copper clad vessel found in ultra-deep waters of the Gulf of Mexico during oil and gas surveys. [Wikimedia Commons, NOAA Okeanos Explorer Program]](https://s3-us-west-1.amazonaws.com/accendo-media/wp-media-folder-accendo-reliability/wp-content/uploads/2023/12/copper-2.jpg)
In 1747, the British navy captured a French ship that had a layer of copper nails in the keel. This led to experiments with copper on three British ships in the 1750s, then the complete coppering of HMS Alarm in 1761. (Goodwin, Harris) The Alarm was destined for the West Indies, where hull lives were as short as two years. Copper was adopted for the Alarm because “it might prove as effectual as any other method we can at present think of,” wrote the Admiralty to the Navy Board. (Harris) The copper sheathing of the Alarm was publicly reported in The Gentleman’s Magazine and The Public Ledger, the Alarm was a success, and copper sheathing was installed on more ships. The First Lord of the Admiralty, the Earl of Sandwich for whom the sandwich is name, inspected the coppered hull of Alarm when she returned from the Caribbean in 1763. (Rodger) Several more ships had copper sheathing installed, but a few were instead lined with copper nails. (Harris)
Degradation of iron bolts was observed in the Alarm, and efforts to insulate the iron from the copper began almost immediately. In 1765 and 1768, the Tartar and the Dolphin had their bolts severely damaged by electrolytic corrosion. The Dolphin had to be completely re-bolted. (Harris)
The special advantage of copper was that it prevented fouling of the hull by sea growth. Biological fouling increased drag, slowing the ship down over time. A fouled ship could be half as fast as when clean. With copper sheathing, British ships retained their top speed regardless of how long they had been at sea. The tactical advantage in maneuver warfare was invaluable, allowing captains to chase down slower enemies or outrun them when they did not wish to engage.
Britain had extensive national copper resources and their opponents did not. France would have to dock or careen her ships every few weeks to keep a clean hull, or import copper. Copper sheathing would increase the British navy’s operational availability. After the moonlight Battle of Cape St. Vincent in 1780, the navy thought that copper had given the British enough speed for a critical tactical advantage. Testimonials from successful ship captains led the government to protect copper as a national military resource and outlaw its export. (Harris)
The maintenance benefits of copper were important, because it stopped ship worm and biological growth. Lead or wood sheathing could also stop shipworm. Lead sheathing allowed the growth of other molluscs and plants. Lead sheathing was soft, easily damaged in heavy weather, by running aground, or when cleaning biological growth by scraping. Wood sheathing had to be cleaned frequently and replaced every few years. Copper sheathing essentially eliminated the frequent maintenance requirements of both the lead and wood sheathing systems.
Similar to the situation with lead, after a few years galvanic corrosion of iron components became obvious. A ship of the line had thousands of large iron bolts below the waterline, pinning it all together. Corroded iron bolts allowed additional flexure of hull, which loosened the seams, admitting enough seawater to make foundering a real risk. Another weak point was the rudder and its support structure. Failure of the rudder meant the ship could not steer to sail into the wind, so navigation was not possible.
In spite of the problem of iron corrosion, the benefits of copper were too great to be abandoned. The field of electrochemistry was still a few years away, so the cause was still not understood. However, experience showed that when iron and copper were physically separated, the corrosion was stopped.
Experiments in 1769 focused on how the heads of iron bolts could be physically separated by using tar, pitch, canvas, or paper. Research on alloying copper began, resulting in stronger copper fasteners with less tendency to corrode. This effort eventually resulted in alloys known as Keir’s composition and Muntz metal.
In the meantime, on small ships, iron bolts were replaced with copper bolts. The stress on the bolts in larger ships was thought to be high enough to require iron bolts.
The performance of coppered 5th and 6th rate ships improved. By 1778, there was a proposal to copper larger ships, ships of the line. Cautious experimentation won out, and two 50-gun ships were coppered. 1778 saw orders to install copper sheathing on 32-gun ships, then on 44-gun ships. In early 1779, the first two 74-gun ships of the line were coppered. Constant improvements were made in copper sheathing methods over several years by modifying plate thickness and nailing methods, changing suppliers of the insulating paper, and coating copper with white lead. By 1782, over 300 ships had been sheathed in copper resulting in a “real increase in efficiency at sea” and “lightened the burden of refitting on the yards.” (Knight)
Doubts and Bolts
With a layer of copper tacked onto the entire hull, the heads of iron bolts could not be inspected. Hasty installation of a new system sometimes left wood exposed and still vulnerable to shipworm. Dockings were less frequent, so in some cases the structural condition of the hull was worse (Knight cites HMS Barfleur) even though the exterior of the hull was cleaner. This was dangerous and caused much alarm. Debate continued about whether copper sheathing was a net advantage or a risk. Knight concluded that the innovation was good, the initial deployment was cautious, but followup to resolve secondary corrosion problems was slow and bureaucratic.
In 1783 Captain James Ferguson wrote to a Dr. Joseph Black about the state of copper bolts during a docking of HMS Victory, Nelson’s eventual flagship at Trafalgar. Capitalization is from the original letter:
Some time ago I stepped into a dry dock, Where a Ship was under repair, which had
been Copper’d, and observed the whole Bolts and Iron Work in the Bottom, between 4
and 5 Inches from the outside corroded and nothing but rusty dust, and having
mentioned this in different Companies, I found myself laughed at. But on the Victory
being lately carried into Dock, it is found, That all the Bolts for 4 to 5 Inches inwards
from the Copper, is sound and all the rest inwards to the Hold, nothing but rust and it is
the general opinion of the Officers and Carpenters, who have inspected her, that had
she touched the Ground ever so slightly she must have gone to pieces. And on further
Inquiry, I find the whole Ships which have been Copper ‘d to two years are in the same
condition, and even My Old Ship Venus, which I got Copper’d in Antigua, and as I
attended closely myself to this Operation.
I shall relate the Steps, I caused take to prevent the Copper from eating or corroding
the Iron. After the Sheathing was riped (sic) off, 1. A strong Fire was put under
her, all the Pitch burnt entire, and every little Nail taken out. 2. Two Strong Coats of
White Lead and Oil put on. 3. Over the head of every Bolt, a Strong Coat of Pitch with
Oakum and brown Paper. 4. Over that Canvas and a Plate of Lead drove on with
Copper Nails. 5. Then the Copper Plates put over all & nailed down with Copper Nails
about two Inches long. And it seems now to be the general opinion of all the officers I
have met with, That our great losses by Ships foundering at Sea, have been occasioned,
by the Iron Work giving way as they were all Coppered.
The manner I see our Ships Coppered in our Yards at home is 1st. A Strong Fire to burn
off all the Stuff from off the Bottom. 2. A thick Coal (coat?) of Gluey Pitch. 3rd. A Strong Covering of pasteboard. 4. Then the Sheets of Copper put on. As this is the
Subject of much Conversation How the Bolts, for 4 to 5 Inches next the Copper are
sound, and all the rest nothing but dross I beg my Com[pliments] to my Worthy friend Doctor Black, state the Case and let me know what he takes to be the cause of this.
I am told, that in the place of Iron Work, a mix’d kind of Brassy Metal is to be used
for Bolts &c. But I greatly suspect it will be brittle, and want answer, for it is out of the
power of man to build Ships so strong but by a heavy gale, they will twist and become
elastic….I am &c. (from Goodwin)
Cleaning the hull was a restorative task. Coppering the hull was a design change meant to reduce the need for preventive maintenance, because it prevented fouling and resisted shipworm better than wood sheathing. The steps taken to layer pitch, lead, canvas, or paper over the bolt heads were also a preventive action intended to prevent corrosion of the bolts. Captain Ferguson compared two different installation methods for a maintenance intervention, trying to identify which better protected the bolts from a specific corrosion attack. The captain was very aware of the hull condition and had personal experience with installation methods. Ferguson also anticipated that a proposed material change would introduce a new failure mode. Ferguson engaged a technical authority, Dr. Black, to interpret the exact failure mechanism.
Dr. Joseph Black
Dr. Joseph Black was a major figure in the history of chemistry. At the time, he was the professor of chemistry at the University of Edinburgh. He invented the analytical balance. He was the first person to describe latent heat and specific heat. He influenced James Watt’s early work on steam engines, as he introduced the concept of latent heat to Watt. Black was the first person to isolate carbon dioxide and associate it with animal respiration. (Muirhead p. 78)
Goodwin quoted the response from Dr. Black, who laid out several logical possibilities for the rapid decay of iron in the presence of copper. Black wrote:
What then will you say, could be the occasion of the rotten state of the Bolts. The
Suppositions that appear to me………….but they are merely Suppositions are these –
-One Consequence of the Coppering is that the Ships require careening & inspection of
their Bottoms less frequently than formerly as their bottoms remain clean & fit for
sailing – but it may have been forgot that the Bolts are liable to decay & they may have
been allowed to remain long without being renewed.
2ndly – All the world knows that we have been under necessity of fitting out our men of War with the greatest possible dispatch during the greater part of the War, I can imagine that in some cases when Coppered Ships were docked, upon examining their bottoms the outer end of the Bolts being found good and sound which formerly was the first thought that decayed it was concluded that the whole Bolt was sound & it was therefore allowed to remain although the inner end of it without being suspected was totally changed into rust –
3rdly- Perhaps the Iron which had been used in the Navy for some time past may have been of a different quality from that which was used formerly, & more liable to Rust………
You mention your having heard of an Intention or proposal to substitute Brass Bolts in
place of Iron ones but you suspect that Brass will not be sufficiently tough and strong to
serve this Purpose – I am persuaded however that a proper Composition of Brass may
be found which will be as strong & even stronger than Iron & which will last incomparably longer…….
Black first considered causes related to maintenance frequency and quality. The copper hull system allowed extending the time between the hull cleanings, but also extended the time between inspection of associated equipment. Wartime production pressure in shipyards could have reduced the effectiveness of inspections or lowered quality standards. Lack of quality control of the iron could not be ruled out. Perhaps because of his academic position outside the navy establishment, Dr. Black could nominate maintenance management as a cause of this particular kind of corrosion.
Morriss commented that “triennial trimming,” or docking every 3 years, was standard practice up to the American Revolution. After most of the fleet was coppered, cleaning and replacement of sheathing was less frequent. Some frigates were kept at sea until their condition impeded their performance, so corroded bolts were not noticed. The elimination of a frequent preventive maintenance intervention to clean and replace sacrificial wood sheathing had inadvertently eliminated other important inspection and restorative tasks. Dr. Black and others recognized this at the time.
The corrosion of iron bolts was a serious matter. The navy blamed the complete loss at sea of two French ships and at least one British ship on corrosion of iron bolts (Goodwin cited HMS Centaur, but Knight also included HMS Ramillies). Opponents of copper had a good case: two metal sheathing systems had been tried at great expense. Both systems attacked iron structural components, endangering life, property, and national security. The most prudent solution would have been to remove copper sheathing from the entire fleet and return to proven wood sheathing.
Reductions of Maintenance Labor and Workforce
The solution lay in better copper alloys for bolts. By 1785, hardened copper alloys were patented and approved by the navy. To convert a ship from iron to copper bolts, the ship had to be docked, sheathing stripped off, the iron bolts driven out one by one, and replaced with alloy bolts. The navy had to fund the expensive conversion work, ordering conversion for all ships “as fast as the docks can be spared” in 1786. (Knight)
In an 1806 history of the navy, Derrick noted the decline in the number of shipwrights listed in the dockyards between 1702 and 1793 relative to the larger size of the navy. His footnote credited copper sheathing and improved shipyard productivity:
“by the great saving of labour arising from the introduction of coppering and copper-bolting of Ships, as they do not now require docking near so often as formerly, in order to have their bottoms cleaned, nor ever to have their Bolts replaced, as the copper bolts do not decay ; whereas the iron bolts decayed very fast.”
Knight summarized the reduction in maintenance requirement: “Coppering had a dramatic effect on the number of refits, cutting their number in 1782 to half that of the peacetime figure.”
In the revision of the 1806 navy regulations, a requirement was added to prevent damage to copper sheathing during anchoring. Another required the captain’s attention to any repairs of the copper sheathing.
Copper in the United States
In 1798, the American Secretary of the Navy wrote to the naval agents in Rhode Island about the importance of copper bolts for ships sheathed with copper:
It is of importance that the Bolts to be used shoud [sic] be of Copper, for it is found that a vessel bolted with Iron & then coppered will not last more than three years, as the copper corrodes, and soon destroys the Iron — I shall therefore take measures for sending on the copper, the nails and the Bolts and should Iron Bolts be made use of before these arrive, they must be extracted and the others substituted…
(Letter to Agents, Naval Documents Related to the Quasi-war…)
The small American navy was paying attention to Britain’s improvements. In the quote above, a senior government official knows how a material selection that was common would allow failure mechanism that limited the useful life of a national asset…and he was demanding this be avoided.
However, special the copper alloys were not available…today, they would be on an export control list of some kind.
Paul Revere was trying to figure out how to make copper alloys for bolts for the U.S. Navy’s original American frigates including the USS CONSTITUTION:
I determined if possible to gain the Secret. I have the satisfaction to say, that after a great many trials and very considerable expense, I have so far obtained my wishes, that I did supply the Constitution for dove tails, Staples, Nails &c &c to the amount of 1000 Weight drawn from Copper of my Melting…
(Paul Revere letter to congressman, McCarthy)
In the early 19th century, coppering was still rare but becoming more widely adopted. Coppering made economic sense for ships anticipating long journeys in warm water when speed was important, so slave ships were often coppered. In 1807, the China merchant Rapid was built near Boston with a copper bottom. This ship sailed from Boston to the far east in 1810, but was wrecked on the coast of western Australia in 1812. An archaeological investigation of the sheathing concluded that there was substantial similarity with the methods used to sheathe HMS Victory, which was coppered in 1780. (Staniforth) Within 27 years, British coppering methods had spread to the American navy and American commercial shipping.
![Cmdr. Sean Kearns, 73rd commanding officer of USS Constitution, and Anne Grimes Rand, USS Constitution Museum president, display the first sheet of copper removed from Old Ironsides as the ship begins a multi-year restoration period. [US Navy photo, Wikimedia Commons]](https://s3-us-west-1.amazonaws.com/accendo-media/wp-media-folder-accendo-reliability/wp-content/uploads/2023/12/copper-3.jpg)
![Petty Officer 3rd Class Jorge Ortiz, assigned to USS Constitution, hammers a copper nail into the new copper sheets which line the hull of the ship. [US Navy photo, Wikimedia Commons]](https://s3-us-west-1.amazonaws.com/accendo-media/wp-media-folder-accendo-reliability/wp-content/uploads/2023/12/copper-4.jpg)
Effect on Dockyard Management
Even under Samuel Pepys in the 1680s, there was a desire for efficient dockyards. In 1682, Pepys sent a draftsman and master carpenter, Edward Dummer, on a tour of the Mediterranean. Dummer recorded the details of foreign dockyards, naval arsenals, and constructions and repair facilities. This was a combination of mapping, industrial espionage, benchmarking, and intelligence collection. Covered construction and storage facilities aroused some interest. Pepys advocated for covered facilities, but they were not adopted in Britain for more than a century.
By 1694, Dummer was an assistant surveyor of the navy. He had intentionally incorporated a scientific approach to dock design and dockyard layout, striving for efficiencies using some lean principles. Dummer’s yard design had several lean goals: to minimize movement, especially crossing of cart paths, by channel traffic; more efficient handling of material; more efficient supervision and and management oversight. (Fox)
These efficiencies became important during the reign of dry-rot, when dockyard repair capacity determined the size of the British fleet. In the 1790s to 1830s, when the dockyards were concerned with rot and copper sheathing, they would again have to use science and technology to change dockyard infrastructure to be able to deliver the technical services needed to maintain a large and busy fleet.
The Navy Board wrote standing orders to the yards to direct their organization and work practices. The orders dated back to 1658, and contained instructions that were contradictory, obsolete, disorganized, and difficult to navigate. The result was bureaucratic confusion and slow decisions. Samuel Pepys had revised the standing orders for dockyards in 1640, they were re-issued in 1662, but still in place in 1770s. Meanwhile, the instructions for sailing officers were on the eleventh revision. (Knight)
Revisions to dockyard standing orders were attempted in 1764, 1786, and 1798. Between 1779 and 1783, the Navy Board issued 82 standing orders to the dockyards regarding copper sheathing. In 1806, a reform commission finally delivered a single set of organizational regulations for the management of government dockyards. Morris argued that implementing centralized management standards emphasizing individual responsibility was fundamental to the rise of the British Empire.
In the late 18th century, Royal dockyards were some of the largest industrial facilities in Britain. After copper sheathing was adopted, the navy consumed 20% of the nation’s copper. A single mine owner supplied three of the six dockyards, threatening the copper supply. The navy established a metal reprocessing plant in 1805 to recycle waste copper and reduce dependence on contractors. The internal production allowed the navy to control quality specifications internally for better, longer lasting copper plates. The “metal mill” cut the government’s cost from 42 to 8 pounds sterling per ton of copper. The engineering supervisor was Samuel Bentham, who is better known for inventing or exploiting one of the first systems of mass production to make rope blocks in the Portsmouth Dock Yard’s block mill. (Morriss) Dockyards adopted cutting-edge methods of manufacturing to improve efficiency and avoid the maintenance burden imposed by a fleet that was too large and too busy be be kept in repair with a traditional approach.
Humphrey Davy and Michael Faraday
Copper sheathing had a mysteriously variable service life. In 1823, the Admiralty asked the Royal Society of London to recommend “the best mode of manufacturing copper sheathing, or of preserving it whilst in use from the corrosive effects of oxidation.” (Hay, 1863 address to Institution of Naval Architects)
In his biography of Michael Faraday, Frank A. J. L. James noted that the “naval budget had been reduced by 71.4% since the end of the war in 1815, and hence the Navy Board was seeking to lower expenditure. If the frequency with which ships needed to be dry docked to replace their corroded copper could be reduced, then significant savings would be made.” The research into copper corrosion was intended to lengthen the service life and reduce the lifecycle cost of the copper sheathing system.
In 1824, Humphrey Davy presented the results to the Royal Society of London, saying,
…there seems every reason to expect…that small quantities of zinc, or which is much cheaper, of malleable or cast iron, placed in contact with the copper sheeting of ships, which is all in electrical connection, will entirely prevent its corrosion….
…there is considerable ground for hoping that the same application will keep the bottoms of ships clean, a circumstance of great importance both in trade and naval war. It will be unnecessary for me to dwell upon the economical results of this discovery, should it be successful in actual practice, or to point out its uses in this great maritime and commercial country. (Philoshopical Transactions of the Royal Society)
Davy had invented a method of preventing corrosion called cathodic protection. However, it was not immediately useful to the navy – cathodic protection worked, but with an unwanted side effect. Reducing corrosion limited the release of copper ions into the water, which allowed biological growth to attach to the copper. The problem of corrosion was solved, but the problem of hull fouling returned. The navy did not actually adopt the use of cathodic protection for copper sheathing, making a conscious choice to accept long-term thinning corrosion to keep clean hulls and fast ships.
Davy was already famous, the first man made a baronet for a scientific discovery. He was President of the prestigious Royal Society. Davy’s investigation of copper sheathing was covered by several London journals: the Annals of Philosophy, The Chemist, Mechanic’s Magazine, and in America in the Boston Journal of Philosophy and the Arts. When an older patent for sheathing using copper coated with tin was discovered, and a newspaper claimed that Davy had not made a discovery. This debate played out in the pages of The Times in 1824, with sparring editorials by secondaries and Davy eventually writing a response letter to the editor. (Rushton)
Cathodic protection would benefit the navy when iron hulls were introduced. By 1906, periodic checks of sacrificial zinc anodes were required by navy regulations. Today, cathodic protection is routinely used on iron or steel structures exposed to seawater, but modern anti-fouling paints are much superior to those available in 1824. Two hundred years later, most steel ship hulls use a combination of sacrificial zinc anodes and a more advanced active system that Davy speculated “could hardly be applicable in practice.” In this system, an electrical current source balances the potential difference to stop the corrosion. The modern term is impressed current cathodic protection, or ICCP.
Several articles in this series have referred to Royal Navy surveyor John Knowles and his 1821 book An Inquiry Into The Means Which Have Been Taken To Preserve The British Navy, From The Earliest Period To The Present Time, Particularly From That Species Of Decay, Now Denominated Dry-Rot, which earned him membership to the Royal Society. Knowles had researched the Royal Navy’s battle with dry rot since the time of Samuel Pepys in 1690. Sir Humphery Davy’s first biographer, John Paris, interviewed John Knowles about the history of sheathing and methods to prevent shipworm. This is more evidence that Knowles’ work on preventive maintenance and dry rot was widely known, and that a learning organization existed in the navy’s establishment.
Davy’s assistant, Michael Faraday, actually conducted many of the experiments. Faraday knew that a complete circuit path was required for corrosion. After Davy’s death, Faraday returned to corrosion and established a quantitative relationship between electrical current and corrosion rate. In 1831, he discovered electromagnetic induction and coined the terms electrode, electrolyte, anode, cathode, and ion. The unit of measurement for electrical capacitance, the Farad, is named for him. Faraday’s development of many fundamental electrical principles was seeded by the navy’s need to preserve the copper sheathing on warships to reduce maintenance requirements.
Conclusion
Like lead and wood sheathing, copper prevented the hull system’s structure from damage from shipworm. The English navy had a program to install lead sheathing starting in 1670, but by 1700 abandoned the effort due to galvanic corrosion of iron components.
Copper sheathing significantly improved the performance of the hull system while reducing maintenance requirements. The navy experimented with copper sheathing beginning in 1761 and extended the improvements to their most important naval assets by 1782. The Royal Navy saw improvements in their maintenance workload, workforce requirements, and operational availability. At the larger scale, copper sheating affected the entire copper industry, British naval and commercial power, and influenced shipbuilding in Britain and America.
Preventing corrosion of iron and copper involved government programs, scientific research, patents, and leading scientists like Black, Davy, and Faraday. Copper sheathing changed shipyard drydocking maintenance requirements, the British mining economy, and employment levels in government yards. Technical improvements continued as more metals were introduced to hull systems over the next century.
Besides reducing maintenance, the introduction of copper improved the Royal Navy’s management of change, the industrial supply chain, dockyard industrialization, and brought more lean and efficiency programs to the dockyards.
In Foundations of British Maritime Ascendency, Morriss concluded that the bureaucracy that developed to run dockyards and provide naval logistics in this period was a major factor in the British Empire’s dominance in the 19th century.
References
van Duivenvoorde, Wendy The Use of Copper and Lead Sheathing in VOC Shipbuilding
The International Journal of Nautical Archaeology (2015) 00.00: 1–13
Goodwin, Peter The Influence Of Industrial Technology And Material Procurement On The Design, Construction And Development Of H.M.S. Victory, Ph.D. thesis, University of St. Andrews, 1998
http://hdl.handle.net/10023/15112
Fincham, John A History of Naval Architecture: to Which Is Prefixed, an Introduction Dissertation On the Application of Mathematical Science to the Art of Naval Construction. London: Whittaker and Co., 1851. https://hdl.handle.net/2027/hvd.32044044835676
Maurer, Maurer Coppered Bottoms for the Royal Navy: A Factor in the Maritime War of 1778-1783 Military Affairs, Vol. 14, No. 2 (Summer, 1950), pp. 57-61
Maurer, Maurer, Coppered Bottoms For The United States Navy, 1794-1803 Proceedings Vol. 71/6/508, US Naval Institute, Annapolis, June 1945
Harris, J. R. “Copper and Shipping in the Eighteenth Century.” The Economic History Review, vol. 19, no. 3, 1966, pp. 550–68. JSTOR, https://doi.org/10.2307/2593163.
Rodger, N. A. M. The Insatiable Earl: A Life of John Montagu, 4th Earl of Sandwich 1718-1792, London: W.W. Norton & Company, 1993
Knight, R. J. B. “The introduction of copper sheathing into the Royal Navy, 1779–1786” (PDF). rogerknight.org. Retrieved 28 December 2017. http://www.rogerknight.org/pdf/The%20Introduction%20of%20Copper%20Sheathing.pdf
Knight, R. J. B. “The Royal Dockyards in England at the time of the American War of Independence”, (unpublished University of London Ph. D. thesis), 1972
Mccarthy, Michael, and McCarthy, Mike. Ships’ Fastenings: From Sewn Boat to Steamship. United States, Texas A&M University Press, 2005.
Muirhead, James Patrick. The Life of James Watt: With Selections from His Correspondence. United Kingdom, D. Appleton & Company, 1859. https://books.google.com/books?id=MeJUAAAAcAAJ&pg=PA78
Morriss, Roger, The Foundations of British Maritime Ascendancy: Resources, Logistics and the State, 1755–1815, 2010
Morriss, Roger, Science, Utility and British Naval Technology, 1793–1815: Samuel Bentham and the Royal Dockyards, 2020
Derrick, Charles Memoir of Rise and Progress of the Royal Navy, London: H. Teape, 1806
https://hdl.handle.net/2027/nyp.33433009405386?urlappend=%3Bseq=256
United States. Office of Naval Records and Library. Naval Documents Related to the Quasi-war Between the United States And France: Naval Operations … February 1797-December 1801. Washington: U.S. Govt. Print. Off., 1935.
https://hdl.handle.net/2027/uva.x001921001
Staniforth, Mark, The Introduction and Use of Copper Sheathing – A History, Bulletin of the Australian Institute of Maritime Archaeology, 1985
https://www.academia.edu/358814/The_Introduction_and_Use_of_Copper_Sheathing_-_A_History
Fox, Celina (2007). “The Ingenious Mr Dummer: Rationalizing the Royal Navy in Late Seventeenth-Century England” (PDF). Electronic British Library Journal. http://www.bl.uk/eblj/2007articles/pdf/ebljarticle102007.pdf
Hay, W. J. “ON COPPER AND OTHER SHEATHING FOR THE NAVY” Royal Institution of Naval Architects. Transactions of the Royal Institution of Naval Architects. Vol 4. London, 1863
https://hdl.handle.net/2027/njp.32101050824687?urlappend=%3Bseq=107
Frank A. J. L. James Michael Faraday: A Very Short Introduction, Oxford University Press, 2010
Rushton, Sharon Humphry Davy: Analogy, Priority, and the “true philosopher” Ambix, Vol. 66 Nos. 2–3, May–August 2019, 121–139
https://www.tandfonline.com/doi/pdf/10.1080/00026980.2019.1616947
Paris, John Ayrton, 1785-1856. The Life of Sir Humphry Davy, Bart., LL.D.: Late President of the Royal Society, Foreign Associate of the Royal Institute of France, &c &c. &c.. London: Henry Colburn and Richard Bentley, 1831.
https://hdl.handle.net/2027/hvd.32044011223112
Humphery, Davy. “On the corrosion of copper sheeting by sea water, and on methods of preventing this effect; and on their application to ships of war and other ships.” Philosophical Transactions of the Royal Society of London for the Year for the Year MDCCCXXIV. Part 1. London: The Royal Society. p. 158
Leave a Reply