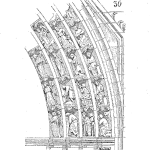
Upon my son’s return from studying abroad for a semester, I asked him what he learned. He said there are a lot of smart people in the world.
I concur.
My son is just starting to explore the world and begin his working career.
I envy his journey as the discovery of the myriad of wonderful people and places are now expected, and comfortable for me.
Recently, in an interview, I was asked about what I have learned from the many projects around the world.
Beyond the different and delicious foods, variations on comfortable hotels, I have learned about the importance of people in the design and maintenance processes.
Specifically the importance of ownership and caring about the reliable performance of the equipment.
Travel does have some challenges and interesting twists. From armed escorts when traveling in Nigeria, to walking through deep snow to find the hotel in Norway, to searching for a cup of coffee Sunday morning in Shanghai, the many adventures have all been educational.
What is common though is the people I’ve met and worked with along the way.
The passion for improving reliability performance is worldwide.
The industries and cultures may differ, yet the desire to maintain and operate equipment with high availability is not.
A trip to Paris
Once I was asked to work with a plant in Paris (later learned in was in a small town in Texas, not France) on an FMEA for a new piece of equipment.
It was a bottling plant and the FMEA study included participants from the equipment manufacturer, manufacturing engineering, maintenance team, and equipment operators.
Everyone had a unique view of the equipment and how it operated. Everyone had a voice and contributed to each other’s understanding of the equipment and how it could fail.
The implementation of the action items from the study significantly improved the equipment uptime and created a working team across the organization that continued to make improvements.
Norway in January
An oil exploration company based in Europe struggled to understand their field failure data.
They knew it contained clues that could help them improve the reliability of their system.
The classes and discussions ranged from basic plotting techniques, which prompted questions.
It then included statistical modeling that lead to insights as the team teased the information out of the datasets.
Playing with trains
Once working with a light rail transit organization found that the well-maintained equipment occurred when the maintenance technician had a sense of ownership for the equipment.
This experience has been mirrored in different factories and organization around the world, including Oman, Nigeria, and England.
The extra expense of assigning teams to specific equipment is offset by the improvement in availability and reduction in maintenance costs.
Consumer product built in China
A chance encounter with a financial analyst at a client’s lunch room led to a brief discussion of what types of problems I was working to solve.
At the moment I was looking for previous production test data to form a baseline for upcoming new product testing.
She not only knew the right person in China to contact, our work together lead to savings of hundreds of thousands of dollars by simply reviewing the data, eliminating unnecessary testing, and focusing on making improvements based on the data.
The cleanest factory
An electronics factory in Mexico included about 30 minutes of cleaning and maintenance at the end of every shift.
Everyone in the plant, everyone – not just operators and maintenance – swept, cleaned, polished, aligned, inspected, and organized their work areas and surrounding equipment.
When someone finished their assigned tasks they would move to an area that needed some assistance. Besides being clean, the plant ran with exceptionally high availability.
They spotted and dealt with the issue while they were still small and quick to address.
Design for maintainability
In Spain, a design team working on an industrial printer was unfamiliar with creating maintainable equipment.
A design challenge was the variability of the paper stock leading to jams that could seriously damage the print heads (most expensive part of the equipment).
While it was possible to replace the print heads they wanted to avoid expensive repairs to keep the cost of ownership down.
With the application of a few basic maintainability principles, they moved the paper alignment process to an area when a jam would not cause damage to the print head and was quick and easy to clear.
The food and people
My travels enjoyed the seafood dished on the southern tip of Korea, small banquets in China, a small bottle of wine with lunch in a French factory cafeteria, and plenty of jalapenos with lunch in a Mexican factory.
Oh, and waiting till after 10 pm for Barcelona restaurants to open.
I’ve enjoyed the hospitality of gracious hosts that shared their pride of their homeland, culture, and work.
It is the people that have taught me so much about reliability and maintenance. They have shared their best practices and challenges with me.
There is excellence in design & maintenance practices all over the world.
A mix of understanding the value to the organization along with a culture that cares about the equipment makes a huge difference.
My work with organization often focused on the tools and techniques of reliability engineering.
On occasion, the work includes shifting the culture to one that cares about reliable equipment.
What has been your experience? What have you learned during your travels?
Related:
Networked and Positive as a Reliability Engineer (article)
5 Steps to Building a Reliability Culture (article)
Successful Reliability Engineers Add Value (article)
Leave a Reply