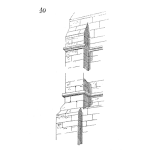
Anyone who knows me may also know about my father, Charles Latino, and his lifelong contribution to the field of reliability. My father was one of the pioneers of reliability in the 1950’s when nobody even knew what reliability really was. He pioneered and championed technologies like vibration analysis, infrared thermography and many others working for a Fortune 100 chemical company. Later he focused his attention on the cultural aspects of reliability and how organizations need to behave to make it all work.
He was also a mentor for me and my four brothers and sisters who remain in this field. One thing he always preached was: Priority, Proaction and Focus. I heard the words but never really internalized their true meaning until I started working with many different industries as a consultant and later working as a practitioner at a very large industrial facility.
Focus – This is the one that has really made an impression on me over the years. As human beings, we think we have the capacity to do more than is really practically possible. We say YES to everything and find that there is not enough time and resources to effectively do all that we commit to. We try to be good soldiers, but we end up not being very effective. There are simply too many issues, failures, initiatives and projects that come up every day in a large industrial facility. It is so easy to lose focus and get caught up in the priority of the day. As manager’s, it is our job to keep people focused on key priorities and not asking our people to perform non-value added activities that limit their focus.
Priority – Leaders must define the key priorities and communicate those to everyone in the organization. This is not a poster on the wall in a conference room but very actionable priorities for the facility. Once this is in place, leaders need to ensure that they are not asking their employees to work on tasks that are not in alignment with these priorities. Priorities do change from time to time and that is expected. But it should be the exception and not the rule. Leaders should look for any opportunity to reinforce priorities and to make sure progress is being made towards those goals.
Proaction – Reaction is the order of the day in most industrial facilities. The failure of the day, the latest request from corporate, the
customer compliant that needs immediate attention, etc. It is easy to fall into the trap of reaction. However, we must continue to devote the time and resources to do the proactive activities that drive continuous improvement. If we continually allocate all of our resources to the issue of the day, it will drive the facility into a slow and painful deterioration of performance. We can get away with it for awhile but the accumulation of reactive work will take its toll and takes a lot longer to get out of it then it took to get into it.
As most of us can relate, its easy to put on those few extra pounds by not focusing on healthy eating for a while. It does not appear right away but you wake up one morning and wonder, how did this happen? It takes a lot more work to take it off then it did to put it on, that’s for sure!
It is the same at a large industrial facility. Once you are in the ditch, it takes tremendous effort and resources to get out. The larger the facility the harder it is to get out.
So remember these three principles, Priority, Proaction and Focus. Every great organization employs these principles everyday. I think of the story of Apple when Steve Jobs returned in the late 1990’s. He got rid of every new project and product and said we are going to develop 4 products. He drew a 2×2 matrix and wrote consumer/professional on one side and laptop and desktop on the other. We are only going to FOCUS on these 4 products. He went onto say that he is was as proud of what Apple decided NOT to do as he was for what they actually did.
Leaders own and drive the culture and behaviors of their employees. It is up to us to drive focus and priorities and insisting that resources are always dedicated to proaction and continuous improvement even when it does not seem prudent or popular.
So what are your thoughts on how well your organization is able to apply these principles?
Leave a Reply