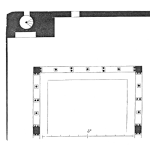
It is a mockery to use business performance indicators to manage a company or department. Using the information that shows up on the management dashboards on your screen can wreck your company. Measuring a process does not put you in control of it. A process is totally self-controlled. You always get what the process gives you. Organizational processes work well or do not because of their design.1 A business process that cannot achieve its aims is the wrong design for its purpose.
Keywords: key performance indicators, KPIs, business process measurement
Financial performance and productivity results are interesting for a business to know, but they are point-in-time samples of what your processes were producing at that moment. The data in weekly, monthly, and annual performance charts are the results your processes let you have. When you take another sample in the following period, you will get a different result. If a performance chart contains only natural outcomes, then that is the best the process can give, and there is nothing more you can do about it. If you don’t like it, the only choice is to design and build a better process.
Plotting the frequency of process results taken over a long time gives you a distribution curve of process performance. It may look like the bell curve shown in Figure 1, or it may take some other shape. Every time you measure a process variable, the value will be somewhere on the distribution curve. When you take a sample and show its measure in a monthly report, it is a result from some point on the curve. One month you get one value for the indicator. The next month the sample comes from elsewhere on the distribution, and you get another result. Wait a while, and the result will change again.
Variation in results is how a process works. You get fluctuating values over a period of time—some good, some bad, and many in between. If you expect great performance results every month, you are expecting the impossible because a process produces outcomes anywhere along the curve.
You would get far more management value from a monthly report if it also showed the frequency distribution of the performance measure alongside its trend plot and where on the distribution the point was located.
Once you have a lousy process design, you will get lousy results until you get a better design—nothing else you do will bring process management success except having the right process design in the first place. You might think that collecting management indicators will aid in correct decision making. But if the process is already stable, every change made to it can worsen performance. Once managers and people get a result that is not ideal, they will tinker and make adjustments to the process. But it is no good to make changes unless a process is out of control.
First it is necessary to check whether the process is running stably, and if it is, then leave it alone. Any tweaking will only ruin it. To be of any use for process management, your performance indicators need to measure the extent of the deviation from the ideal process outcome, its target “bulls-eye”, and see whether the distribution is steady. Indicators are useful when they help people make the right decisions to improve process designs or help them find out-of-control process effects and remove them. If they are used for other purposes, they will cause you to ruin your business performance.
Monitoring a Process and Its Process Steps
Key Performance Indicators are the measures used to monitor process outcomes—they show the total effect of all influences on the process. Performance Indicators (PIs), on the other hand, are used in the process steps—they tell you about a step’s variability.
How do you monitor and measure a process such as production, maintenance, or a continuous improvement process so that you can make it world class? What about a job—how do you monitor and measure work and use the information to make it highly successful? What about the tasks in the job—how can you make them more efficient and effective? In the Plant Wellness Way, every one of these questions is answered the same way: by monitoring the trend and stability of step inputs and outputs, as well as checking the trend and stability of the whole process to see cumulative effects.
Once you have the process design captured in process maps and procedures, you have everything you need to properly monitor, measure, and improve the process. On the process map, important inputs and outputs from each step are identified. In Accuracy Controlled Enterprise 3T procedures, all variables in the process step are identified and quality standards are set for them. The ideal results and tolerances are defined using measurable performance terms with values that can be charted. The process map and supporting documents contain all the performance measures you need to monitor the whole process and its steps’ performance. Useful statistical charts and graphs can be developed with the results and used to observe and compare process and step behavior.
Figure 2 is a process map of a purchasing process. The process is used to buy what is needed in as simple and straightforward a manner as possible. What you want from the buying process are the things you asked for. A measure of total process success is whether you received the items brought. A second measure of overall success is if you got your order on time. A third is whether the order was in perfect condition. A fourth is whether the invoiced amount matched the price in the offer.
These purchasing requirements are what the process should always deliver with 100% certainty. Less than 100% conformity on all measures means the process design failed. Somewhere, a process step, or more, went wrong. If you monitor step outputs you will know which ones failed.
A process fails when a process step fails. If a result from the complete process is not acceptable, you need to find and correct the steps in the process that control the result. To do that, you need indicators of each step’s success. The measures you use are the required step outputs noted on the process map.
The beauty of using the measures written in the process map is they are what the process design is meant to deliver. They directly result from the behavior of the step and reflect the activities done in a step by those running the process. The performance values are available because the procedure asks for them to be generated as the work is done. If it is necessary to understand why and how a step failed internally, you observe and measure the variables in the step, even going as far as statistically charting them to look for the tell-tale signs caused by the presence of defects. When you report on the process and talk to people about its performance, it will be with facts and answers specific to the process.
All the best to you,
Mike Sondalini
Leave a Reply