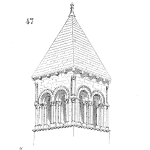
Reinforcing bar is forged steel used in concrete to give the otherwise weak concrete structural tension strength. Reinforcing bar manufacturing is done in a factory using computerised machines to straighten, cut and bend the steel. It is a highly automated process once the bar is loaded onto the manufacturing machinery. These machines are computer controlled and form the bar to the shape and dimensions instructed. The bar specification and dimensions are identified from the engineering drawings by the Scheduler who enters the details into a scheduling software program. The program converts the reo-bar size requirements into computer controlled manufacturing instructions for the machines and a delivery schedule for the production shop.
Our assignment was to identify opportunities to improve the business and streamline the operation from production through to delivery.
A Lean improvement investigation of this nature starts by drawing the process maps for each stage of the operation. Beginning with the acceptance of an order through to its delivery at the construction site, the entire business was process mapped one phase at a time—order acceptance, quantities take-off, scheduling, raw materials supply, manufacture, despatch, and delivery.
In order to draw the process maps correctly and reflect current state practices our Lean Consultant interviewed Supervisors from each department in the operation. The Supervisors explained in detail the activities and tasks done in each process phase as an order progressed through the business. From their detailed descriptions the process maps for each department were developed. Each task was given an individual name and a short description of the activity performed was written in or under the box for that task. The process map was reviewed by the Supervisor to confirm its accuracy and make any necessary changes to reflect the real current state map of the operation.
With the businesses processes well documented and flow charted our Lean Consultant began analysing each phase of the business by collecting data on the variations in performance of a process. Every business process has a natural distribution of performance outcomes. We wanted to view that performance distribution and needed factual data from running the process over a sufficiently long time. Some data could be collected off historical records. Some data was collected by observing and recording the activities as they were done.
We were interested in the ends of the distributions—below average performance and above average performance. We wanted to know why the same process could produce such a wide range of results. What were the costs and losses of poor performance when compared to the average performance? What were the time and waste savings from better than average performance? If we could understand what caused the good results we could then mimic those requirements by changing the process to make those great outcomes became business-as-usual practice.
This is how you improve a business process without spending additional capital. The business could have brought new, faster machines. It could have brought new scheduling software and software that better integrated information flow throughout the business. But that would not improve the business process performance. A few steps in the process might be done quicker but the variation would still exist, and probably become even worse.
Now that we understood the process variations and their causes we could draw the future state maps with confidence that truly profitable Lean process improvements could be simply and quickly made in the operation. Had we suggested a future state map too early, for example after drawing the current state maps, it would have been guess work because there would have been no real evidence to support those recommendations. But by collecting and analysing the true process performances we had hard facts and clear financial justification for every one of our recommendations.
We recommended that scheduling be changed from push production to pull production where Despatch set the production schedule and trucks could be fully loaded. We recommended that finished bars not be stored in intermediate storage racks awaiting delivery to again be lifted a second or third time, but instead transportable racks that stacked the orders be made which fitted safely on truck trays. Each stacking rack would start on the shop floor and be loaded directly from the last manufacturing step and be filled with all the loads for a delivery. Once full the entire rack would be lifted onto the truck at once. A low cost handling improvement that saved hours in loading each truck one delivery at a time.
This is our speciality—making Lean work in your company by recovering the hidden-factory you have, and turning what was waste into new, handsome profits for your business. Contact Us now and start working on your great and successful Lean future today.
My best regards to you,
Mike Sondalini
Managing Director
Lifetime Reliability Solutions HQ
Leave a Reply