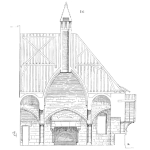
The Physics of Failure Factors Analysis for selecting maintenance strategy is a one-person exercise that identifies all ways a component can physically fail. Equally important to its simplicity is its ability to select the most effective life cycle strategies for maximising reliability. Another powerful business advantage is the failure-addressing solutions arrived at are universal solutions that apply to every other identical component, whatever equipment it is in. Do a Physics of Failure Factors Analysis for one part and you do it for all identical parts for the life of your operation. It is a highly accurate and cost-effective maintenance strategy selection methodology.
Keywords: failure prevention strategy, Physics of Failure, operating risk reduction, maintenance strategy selection, life cycle asset management strategy
Current Maintenance Strategy Selection Methods Do Not Prevent Failure
Top-down maintenance strategy selection methodologies such as Planned Maintenance Optimisation (PMO) select equipment maintenance strategy based on historic failure modes. Maintenance history is reviewed to identify the locations and ways in which a item of plant can fail and appropriate maintenance strategy to prevent equipment failure is selected. If it is not possible to prevent a failure, then condition monitoring means are selected to investigate and identify if there is a problem and when to repair or renew a component.
The alternative method for maintenance strategy selection is to use a bottom-up approach such as Failure Mode and Effects Analysis (FMEA) to select appropriate strategies and practices to maximise equipment reliability. In this case a team of subject matter specialists looks at the equipment and identifies how its assemblies can fail and how each failure is prevented. Where failure cannot be prevented, condition monitoring is used to identify initiation of failure. When the evidence of an impending failure is detected, the item is scheduled for replacement.
The better maintenance strategy selection practices to also include cost analysis of a failure and use the financial impact to make sound business decisions about the best mix of life cycle management practices to implement that maximise operating profit.
Current maintenance strategy selection techniques like those described above do not prevent failures. They are designed to look for disastrous problems to fix—they are failure-focused. They permit defects to become serious problems before you act to prevent a breakdown. If you only look at your machines for problems to fix, then problems is what you will always have.
As useful as these methods can be for improving equipment reliability in reactive organisations, they cannot maximise reliability because they allow failure, and cannot minimise maintenance costs because they generate maintenance. They are also expensive to do, and companies balk at the cost, only apply them to the fewest items of plant possible. Because of the manpower and time commitment needed for analysis, and the drain on resources and costs to implement recommendations, these failure-focused methods are mostly used on mission critical plant and equipment. This means there are still many machines and equipment items in every company where preventable failures continue to happen.
Physics of Failure Factors Analysis for Lasting Plant Health and Wellness
If you want outstandingly reliable plant and equipment, you cannot go around maintaining and repairing them. You need equipment and machines that do not fail. That requires machines and operating practices where failure is not initiated. It is a different reliability paradigm to that used in failure-focused maintenance strategy which finds and fixes problems. Figure 1 highlights the difference between a failure-focused perspective and a machine health-focused view. In failure-focused maintenance you fix machinery problems as you find them. In wellness-focused maintenance you create machine health, so no problems arise. If you want healthy machines, you must provide the conditions that cause their health and wellness.
Identifying health-focused reliability strategies requires different maintenance strategy selection methods than those used in the past. You need to get away from failure-spotting techniques like PMO and FMEA to health-creating techniques focused on defect elimination and failure prevention. The Physics of Failure Factors Analysis is such a tool.
The Physics of Failure Factors Analysis (POFFA) identifies the ways the atomic structure of a machine component can fail and what to do to prevent failure situations arising. If the causes of microstructure failure in every part of an equipment are prevented, then lasting machine health and outstanding reliability will naturally result. POFFA shows you which life cycle strategies and practices to use to stop parts’ microstructure damage and thus produce maximum reliability throughout the entire operating life.
Unlike FMEA, it is not necessary to first know all the failure modes of a component. In POFFA you don’t need to know any failure modes at all. Because you are seeking how to provide a lifetime of health to every part’s atomic structure and microstructure you do not care how many ways it can be failed. You only care about what you need to do to keep the materials of construction of each part in perfect health and condition.
The atomic bonds and microstructure of materials can be destroyed in only a few ways. The POFFA identifies all causes of atomic structure and microstructure failure a part can suffer and guides you to select and use those practices that create machine parts’ health. You do not try to prevent failure; you instead make sure the conditions needed for wellness are always present.
The Physics of Failure Factors listed in the first column of Table 1 are the known scientific causes of atomic bond and microstructure failures. There are not many ways in which atomic bonds can be broken. The list is extended as more causes of atomic structure failure are identified.
The remaining columns list the life cycle situations and the physics-of-failure mechanisms that can lead to atomic bond failure and breakage. To ensure materials-of-construction do not fail we need only ensure that the situations and mechanism that can cause atomic structures to failure do not arise. This is the single most powerful concept in Plant and Equipment Wellness that no other asset management strategy has—identify, deliver, and sustain the conditions for lasting reliability. Where other asset management strategies focus on failure identification and removal and so allow unending failures, Plant Wellness focuses on lasting health and so produces the conditions needed for lasting and outstanding reliability.
The column headed ‘Component Life Cycle Situations’ is used to identify where during the life cycle human error can contribute to component failure. It is also used in later decision-making to select health-creating strategies during the life cycle. Notice that the Physics of Failure Factors Table does not contain many issues that destroy our equipment.
Confirming Business Benefits
Many maintenance activities only add cost to a business and do not actually make the business money, nor do they make the equipment reliable. If doing a maintenance activity does not surely protect your business more than not doing the activity, then doing the maintenance task is a waste of time and resources with no business benefit whatsoever. A maintenance activity must reduce the cost of failure, or it must definitely reduce the frequency of failure, and preferably both.
To ensure beneficial business decisions are made in a Physics of Failure Factors Analysis a calibrated risk matrix like that of Figure 2 is used to test a mitigation’s value. The risk matrix is used to prove if a selected activity is good for your company because it shows if the risk to the business will be reduced by the activity. On the matrix you show the current business-wide risk should the part being analysed fail and the extent of the risk after your selected Physics of Failure mitigations are in place and being properly done. By using the risk matrix, you can readily prove that the mitigations you chose will deliver financial benefits to the business. Below the Low-Risk line (green) you do nothing to prevent a failure event from happening except to ensure the event is a low or lesser risk. Above the Low-Risk line, you select those mitigations across the life cycle that produce lasting atomic structure health.
Follow the recommendations of recognised international risk management standards (such as ISO 31000 Risk Management Guidelines) when you develop and calibrate your business risk matrix.
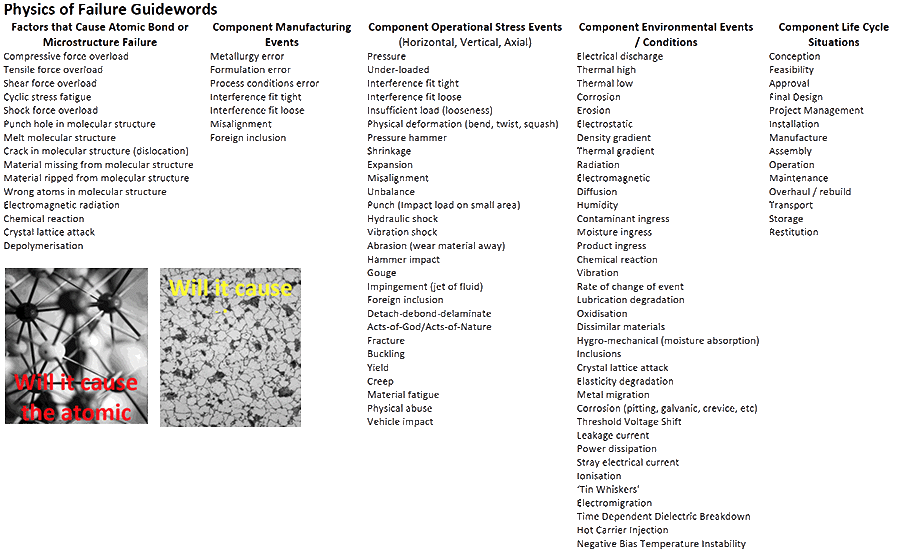
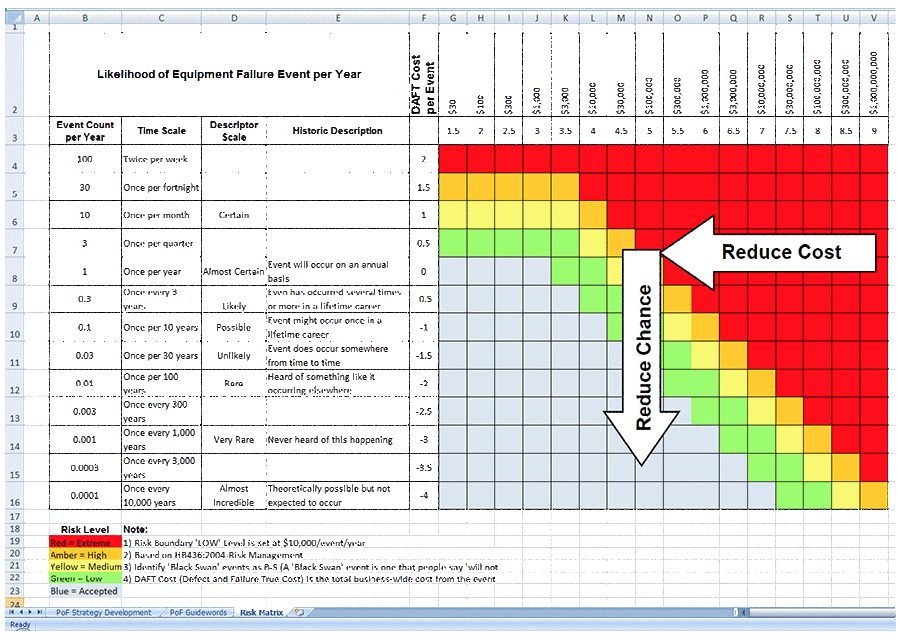
Doing a Physics-of-Failure Factors Analysis
The Physics-of-Failure Factors Analysis is performed in a spreadsheet by a person competent in the design and use of the equipment. An experienced discipline Maintenance Engineer, Process Engineer or long-serving Maintenance Supervisor are the type of functions with the level of engineering and equipment knowledge needed to do the analysis.
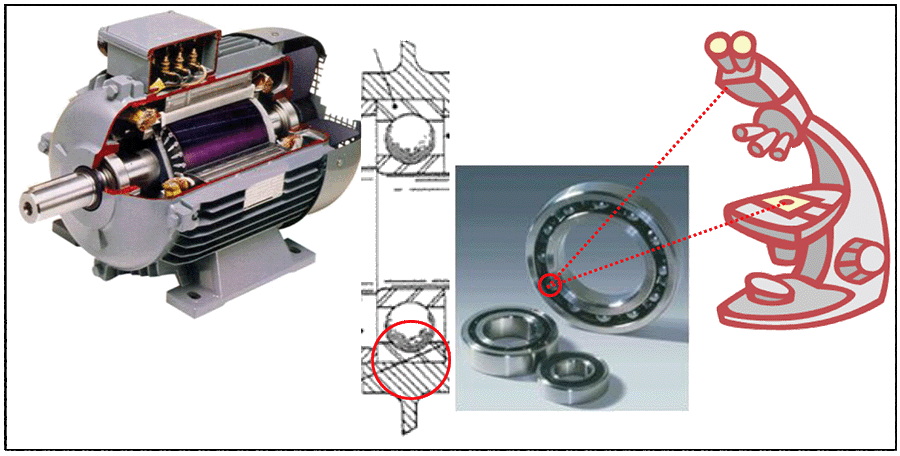
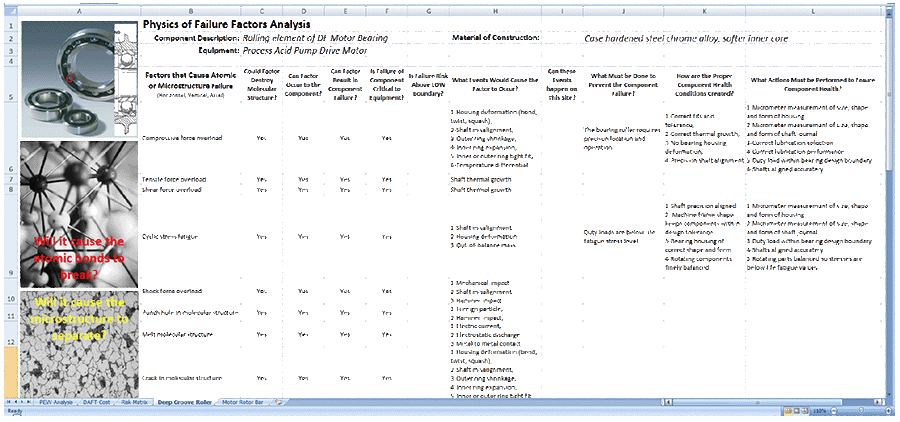
Once the analysis is completed by the appointed person a second competent person reviews the findings for accuracy and completeness. Because it takes just one person to do the majority of a Physics-of-Failure Factors Analysis it is a financially viable alternative to current methods for identifying good operating, maintenance, and life cycle risk mitigations.
Examples of a Physics of Failure Factors Analysis were done for two AC induction electric motor components. One mechanical part and one electrical part was analysed with the method. The mechanical part was the spherical roller of the drive end deep groove roller bearing shown in Figure 3, and the partial analysis is shown in Figure 4. The electrical part was the rotor bar in Figure 5 at the point it leaves the laminations of the rotor, with the analysis shown in Figure 6.
Physics of Failure Factors Analysis is a particularly effective means to scrutinize any part in detail. You can use it like an ‘intellectual microscope’ to examine a component at every location throughout its structure. You ‘point’ the ‘microscope’ at any part of the structure and interrogate that location for all the ways it can fail. In Figure 3 the ‘intellectual microscope’ is focused on the rolling element of the bearing. It could have been pointed at other parts of the bearing—the inner ring, outer ring, retaining cage, and even the lubricant between the surfaces. The same technique can analyse every part of a physical structure down to its atomic level.
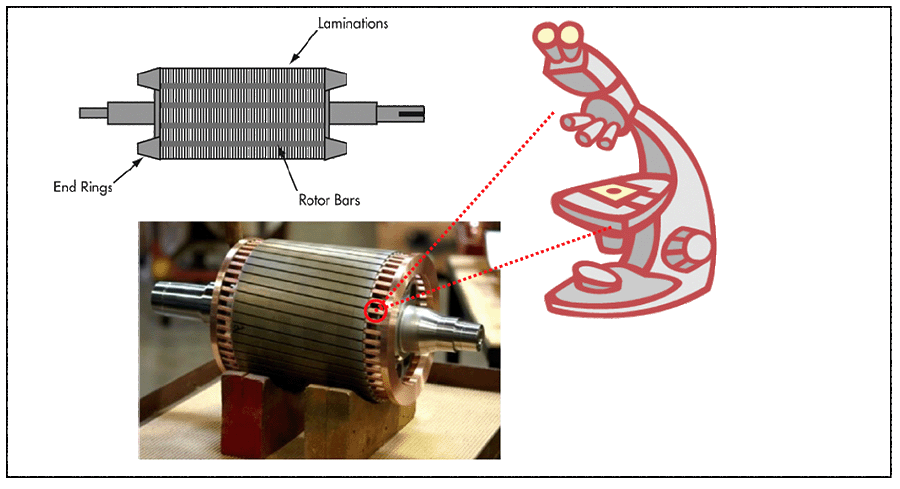
A Physics of Failure Factors Analysis starts with the Factors that Cause Atomic, or Microstructure Failure guidewords listed down the page where they are used to trigger answers to the questions in the columns across the page. The photographs are there to remind you what you are looking to identify. The Event and Condition guidewords are used to identify the causes of atomic and microstructure failures. If a guideword factor can destroy the physical structure of your equipment you want to know about it! Whether you will do anything about the factor depends on the size of the risk to the business by its occurrence.
For each factor that can cause atomic structure failure a series of questions about the factor’s impact on the component microstructure are asked. Note that the answers are restricted to ‘Yes’ or ‘No’. The analysis process identifies the risk. It does not ask you to decide if a scenario carries risk or not.
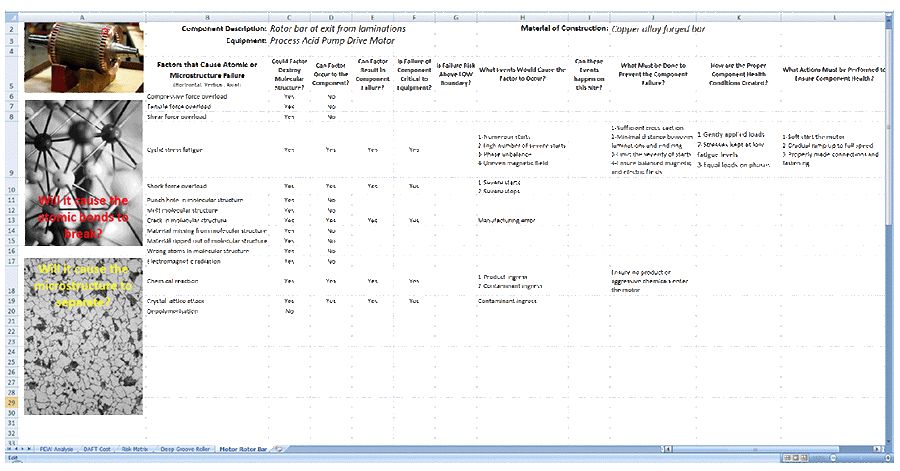
When the answer to a question is ‘No’ the factor is no longer considered. When an answer to a question is ‘Yes’ the factor remains valid, and the next question is asked. If the factor is a real issue and it will adversely impact the business the applicable Physics of Failure mechanisms are identified and the appropriate mitigations for the operating site acknowledged for action.
The lists of stress events and environmental conditions that can cause microstructure failure are reviewed to identify the Physics of Failure situations and occurrences that could cause a material-of-construction failure in the part being considered. All failure-causing events and conditions are recorded for the Physics of Failure Factor, and none are excluded. Those events and conditions that can happen at your site are identified and for each one mitigation are selected. Defect elimination and failure prevention controls are applied at all suitable stages in the life cycle.
Each mitigation decision is reviewed on the risk matrix to test its worth and value for the business. Provided that an improvement substantially reduces an event’s frequency and/or substantially reduces its consequent cost it will show on the risk matrix to be a real business benefit. Once a mitigation proposal is proven financially sound it gives you strong reason and justification to make the necessary changes in your business processes and practices
Conclusion and Comments
When you have a new physical asset management methodology called Plant and Equipment Wellness, the word ‘Wellness’ in its title means that you have to look at your machines in a totally different light. If you must maintain and repair your equipment, then in terms of Plant Wellness your business process to deliver equipment health and well-being has failed. Your machines are not at all well if you must service and fix them.
Plant Wellness is not possible if you are failure-focused on your maintenance, which is the case with Preventive, Predictive and Run-to-Failure maintenance strategies. To achieve ‘wellness’ you must be machinery health focused. The Physics of Failure Factors Analysis is a tool to make you think through what you must do to make your plant and equipment healthy and keep them that way.
The great power of the Physics of Failure Factors Analysis is its simple approach—one methodology to create exceptional equipment reliability that works for every operation. The same process is used everywhere and adapts to each operation’s circumstances. The successful maintenance and reliability practices that cause your equipment to be healthy are designed into your business processes and practices. World class reliability performance is locked into place in your business habits and culture forever.
The Plant Wellness Way methodology and its new analytical tools lets you introduce and sustain the proper business-wide discipline you need to quickly improve your plant and equipment maintenance performance, lower your maintenance costs, lift your plant uptime and create new operational profits because your equipment always performs reliably. Use the Plant Wellness Way POFFA technique to identify exactly what to do to make your equipment healthy. You can now improve your asset maintenance and plant operating processes and practices so that you always get the world-class operational asset performance that drives operational excellence.
My best regards to you,
Mike Sondalini
Leave a Reply