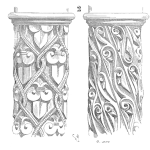
“His Majesty Will Have A Fleet Upon The Durability Of Which There May Be Some Dependence.”
Balancing Fleet Size with Workforce Size
In 1763, the Seven Years’ War ended and the Royal Navy demobilized. The Earl of Sandwich left the office of the First Lord of the Admiralty for the second time. At the end of the war, Britain had 149 ships of the line. Scrapping, retirement, and storage reduced the fleet size and maintenance requirements. The navy was trying to manage a shrinking fleet with a shrinking budget.
In 1763, the Admiralty requested a report of the total value of all ships and their stores, and an analysis of the “annual cost of replacing them in cycles between twelve and sixteen years,” according to historian N. A. M. Rodger. The Admiralty also asked for an estimate for annual repair and maintenance at task work rates if they expanded the number of shipwrights to 3000. (Shipwrights were the carpenters in dockyards who built and repaired ships.)
By 1765, only 47 of the 140 ships were in good condition. The Navy Board made a plan to increase the number of ships in good condition to from 47 to 63, but the plan required three years and an extra £2,000,000. Once restored to good condition, the plan assumed that the existing shipwright workforce could maintain a fleet of 90 ships. This approach would only work if the shipwrights were allowed to maximize overtime all summer, for every summer to come…the workforce and labor budget were at maximum capacity. To actually maintain 140 ships in good condition, the shipwright workforce would have to be expanded from 3,150 to 4,200. The government did not want to expand its civilian industrial labor base at a time when it expected a peace dividend.
A few years later in 1770, the First Lord of the Admiralty Sir Edward Hawke wrote that the navy’s budget could not keep 80 ships in good repair, especially given their annual budget challenges. An international crisis with France and Spain (the Falklands Crisis of 1770) required a sudden naval mobilization. The mobilization revealed the poor condition of the reserve ships and the inadequacy of the existing dockyard structure.
In 1771, the Earl of Sandwich took over the Admiralty for the third time. The dockyard infrastructure that could only support a small fleet effectively. Facilities were optimized for the past Anglo-Dutch wars, so were mostly on the east coast. A large repair backlog existed for the reserve fleet, and there was no political consensus of increased naval spending. Rodger summarized, “[the fleet] could only be kept up by allowing ships to decay before the notional end of their useful lives, and building more ships to replace them.” Rodger quoted Sandwich’s own analysis:
“…when ships are laid up in Ordinary they are divided into three Classes (exclusive of those in good condition) namely such as require small, middling, & great Repair. – Those that are nearest being brought into condition for service must naturally be taken first in hand, & while they are in the Dock the others grow worse & worse, & before there is any room for them many of them successively become past Repair, & must be broken up or sold; whereas were their docks sufficient, more of them would be taken in at them same time, & many valuable ships saved from destruction which would in process of time fully repay the Expense of the additional Docks & other Requisites.” (Lord Sandwich, from PRO/ADM 7/659 f. 59, quoted by Rodger)
The basic problem was that the ships wore out faster than the repair rate, which was limited by the number of docks and the size of the workforce.
One solution was commercial construction of new ships. Commercial construction was thought to be of lower quality than government construction. Low quality construction only worsened the repair backlog in the long run.
Another solution was to improve productivity. Some people theorized that shipwrights would be more productive if their pay was based on individual productivity, called task work, instead of a flat daily rate.
Make the Ships More Durable
A third solution to the difference between the wear and repair rates was prevention. If the ships wore out more slowly, it would reduce the burden on the dockyards. In 1771 Lord Sandwich wrote:
“As the decay of the Fleet, has been infinitely more rapid of late years, it has been my principal study how to remedy that Inconvenience…In a Fleet thus circumstanced, the Decay will always outrun the Repairs, nor is it practicable to keep a large Fleet in good Condition unless some means are found to make the ships more durable.” (NMM/SAN V/6, Rogers p. 137)
To solve the problem of dockyard productivity, Sandwich restarted annual visits to the yards. In the 20 years since he had last conducted site visits, three First Lords had passed through the office without conducting formal site inspections. This time, Sandwich included members of both the Admiralty and Navy Board. The inspections were very detailed and covered many subjects. On a normal Sunday in 1772, he visited thirty-four ships. (Rogers p. 139) He personally visited the reserve fleet at every yard, and also included ships under construction in commercial dockyards.
Sandwich also paid attention to each yard’s inventions, many of which related to preservation or prevention. He inspected the results of a trial of anti-fouling compounds at Sheerness. At Plymouth, he viewed the invention of a tidewheel to work ventilation machines. This pioneering application of mechanical ventilation was meant to slow rot inside ships.
A great deal of attention was paid to stores, especially the condition of timber. Sandwich wrote:
“Unless we can find means by a sufficient seasoning to make our ships last longer, our strength at sea must in a few years be reduced to a state, that carries with it very alarming Reflections.” (PRO/ADM 7/659, Roger p. 139)
The Admiralty sponsored a “continuous if unsystematic program of research going on to test the efficacy of different methods of preserving timber.” (Rodger p. 140)
Sandwich read century-old letters from Samuel Pepys. Pepys said that ships could last 30 years and Sandwich was convinced this was possible to achieve again. Sandwich ordered entire ships built with alternate materials, foreign oak and winter-felled oak, to determine which was superior. With a better stock of seasoned English timber waiting in the government yards, plus a possibility of qualifying foreign oak for construction, there could be more assurance that replacement ships would last without major repairs.
In 1773, the navy changed its standard contract for commercial construction to improve the seasoning of the timber and the durability of the ship. The new contracts doubled the time a ship frame was to age during construction from 6 to 12 months.
Constructing replacement ships with pre-aged timber, and then requiring the new frame to age further during construction, were intentional investments into the initial quality of a new ship. The intent was to reduce the eventual repair burden on the dockyards, allowing the existing dockyards to maintain a larger fleet. Rodger quoted Sandwich:
I have no doubt that many of the ships that now stand upon the Servicable List are far advanced in their decay; some years hence, when they have been worn out, and their place supplied with ships built upon the new plan, his Majesty will have a fleet upon the durability of which there may be some dependence. (PRO/ADM 7/651 ff. 75-76, Rodger p 144.)
Rodger concluded that this was the first time a First Sea Lord had really set up a program to solve a problem instead of treating its symptoms. Sandwich had identified the physical root cause of an unreliable system, and instituted organizational reforms to prevent an unwanted maintenance burden. Full implementation of Sandwich’s solutions would have taken 15 years of peace, stable government policy, and stable budgets. Of course, this would not happen.
Incentivizing Worker Productivity
By 1774, Sandwich’s policies (using timber seasoned for 3 years, requiring the assembled frame to stand and season another year), combined with the existing dock capacity, meant that the government dockyards could build five ships of the line a year. In reality, the yards averaged 5.6 new construction completions per year. Considering the actual hull life at the time, Rodger estimated that the government could only produce and sustain about 60 ships of the line every year.
Sandwich’s needed more shipyard capacity. The navy already supplemented the government dockyard efforts by placing contracts for construction in commercial shipyards. Proposals were made to build new government dockyards, but were so expensive that the idea was abandoned. At the time, the government was forcing the navy to reduce shipwright headcount to control costs.
For 20 years, Sandwich had thought that shipyard workers could be more productive given the right incentives. Workers were paid a daily rate, regardless of how much or little they produced. Sandwich’s new scheme, called task work, would pay workers based on how much work they actually accomplished. Task work was already used in the commercial shipbuilding world, where it yielded better efficiency and better take-home pay. Navy traditionalists thought that commercial quality was lower because of the profit motive. Navy administrations had resisted adopting task work for 80 years. Sandwich saw no evidence of the rumored low quality. In the recent war, commercially-built ships had performed well. Nevertheless, he intended to implement a system of quality oversight. (Haas)
To be effective, fair rates for each task had to be established and a system of supervision had to be in place. Sandwich knew the program would not save money, but instead complete more work on a short schedule. This would free dockyard capacity, and like Lean programs, allow the navy to maintain a larger fleet with the existing organization and infrastructure. Sandwich called task work:
“A matter very little known in the world, but the only material improvement…which will enable us to build and repair a much larger number of ships.” (Lord Sandwich, quoted by Haas)
To prepare for this new plan, the navy’s surveyor spent a year planning and pricing all the tasks steps required to build a 74-gun ship of the line. Task work was not a success initially. The organizational management of change was poor, so the rollout of the program was rocky. The immediate result was a series of strikes and wage negotiations, during which the yards lost capacity after suspending strikers and ringleaders. Capacity suffered for about 3 years, until 1778. After some adjustments, the program was slowly and voluntarily adopted by individual work centers. Ten years later, task work was in general use in English government dockyards.
Storeroom management affects repair and replacement
In the second half of the 18th century, there were improvements in the management of naval stores. Naval stores included timber for both construction and repair, sailcloth, spars, rope, tar, clothing, bedding, hammocks, etc. The tendency to bureaucratic centralized control resulted in the Navy Board becoming more active in managing dockyard stores. Repair and refit schedules could be derailed by a supply chain problem. Good MRO practices were equally important to good maintenance management in the 18th century as the 21st century.
Historian R. J. B. Knight detailed some of the reasons for inaccurate storekeeping in this era. Receipt of goods from contractors required acceptance of the material, then approval for payment by a dockyard officer. The busy officers normally delegated this duty to their clerks. Since this was really outside the clerks’ responsibilities, the officer asked the contractor to pay for the clerks’ time. The clerk’s fee was normally a percent of the total price of the delivery. The result was a significant amount of delay and bribery to simply receive supplies. Worse, there was no independent check of the quantity or quality of goods delivered. The clerks had an incentive to inflate their inspection fees for receipt of material, and many clerks got most of their income through this system. After several attempts at reform, the fees were finally banned in 1801. At that point, the navy required contractors to commit to a price reduction as they no longer had to recover the cost of bribes.
After material was received by the government, there were more problems. Transfer of material within each yard used an internal system of debit and credit that was not standardized. External audits did not exist. Periodic physical inventory counts were not required. Complete inventories were normally only conducted when storekeepers died or resigned. A few occasional inventories were conducted and showed very inflated quantities on the books.
In one example that Knight gave from 1778, the Deptford yard had 4,649 seaman’s beds on their books but could only find 670. In 1777, Plymouth’s book quantity of hemp was 110 tons greater than the physical inventory. Timber inventory was also affected by these problems. The distribution of new stores to the six dockyards was based on quarterly inventory reports. Bad inventories led to poor distribution decisions, even when the timber supply was sufficient. (p. 221)
During the 1780s, the Comptroller of the Navy, Charles Middleton, increased pressure on the dockyards for more frequent inventories. He demanded better agreement between the book value and physical count of stores. Middleton was frustrated, but he improved material management in the dockyards and wrote:
“by obstinate perseverance in the teeth of the irregularity, ignorance, and negligence of the yard officers, which were provoking beyond description…[were] brought into better than tolerable order and now fully reward the trouble that I had in establishing them.” (Knight thesis p. 231-256)
Middleton was later on the Board of Admiralty, then served as First Naval Lord and First Lord of the Admiralty during the upcoming timber crisis in the early 19th century.
Dockyard facilities in the early 1770s were decrepit and too small for the size of operations. Building maintenance had been neglected, preventing proper storage especially of sails, which needed to be aired to prevent rot. Most dockyards could only store a year of timber. The Navy Board reinvested in the facilities over several years. (p. 306-308)
Sandwich expanded the inventory of timber, intending to have a 3-year supply for the entire navy (p 214.) This level was never reached, but improvements were made. Knight gave an example of Chatham using new seasoning sheds and doubling the on-hand timber stock between 1771 and 1773.
One reason a three-year supply was not attainable was that the navy did not entirely understand how much timber it consumed in three years. Poor reporting and bad estimating gave misleading pictures of timber consumption.
The failure mechanism of dry rot was outpacing the production, seasoning, and distribution of repair material. Sandwich realized this would reduce the fleet’s availability. Sandwich commented on his realization just before the American Revolution. Britain’s ability to prosecute a new war in remote North America would be damaged by the lack of timber.
Middleton’s improvements in the reporting of naval stores was an important step in management oversight. Modern historian RBG Knight summarized wrote that Middleton’s reform of naval stores was the most succuessful management reform in the Royal Navy in this period. (Knight p. 256)
Middleton’s accomplishments were recognized even at the time. In an 1806 history of the Royal Navy, Charles Derrick wrote:
“[The Regulation for the Establishment of Stores] was truly an original and great plan, no idea of the kind having probably been ever entertained at any former period….The quantities of those species of stores which are not of a perishable nature and of those which cannot be readily obtained in a time of emergency are calculated to last for a considerable period even in time of war; and they are kept up by means of the annual or occasional contracts. The almost necessary result of this plan has been the preventing of unnecessary or improper accumulations of any stores in the Magazines for so long a time as to occasion their receiving injury by lying too long in them which is a matter of great consequence in such extensive concerns. Many other lasting good effects have also been produced by the measure in question which it is not necessary here to notice; neither could some of them be explained so as to be generally comprehended .” (Derrick p 179-180)
The Navy had also formalized some procurement strategies and recognized the problem of overstocking. They recognized the need to account for lead time and shelf life to determine the stocking strategy for critical spares.
Logistics Reform for Reliability, Availability, and Maintainability (RAM)
During their tenures as First Lord of the Admiralty and Controller, Sandwhich and Middleton succeeded in many system-level reforms. These reforms sought to integrate multiple parts of the logistics supply chain (procurement, construction methods, material distribution, accounting, workforce sizing, and maintenance sustainment) all with the goal of improving the reliability, availability, and maintainability of the the Royal Navy.
References
Rodger, N. A. M. The Insatiable Earl: A Life of John Montagu, 4th Earl of Sandwich 1718-1792, London: W.W. Norton & Company, 1993
Knight, R. J. B. “The Royal Dockyards in England at the time of the American War of Independence”, University of London Ph. D. thesis, 1972
Sandwich, Haas, J. M, “The Introduction of Task Work into the Royal Dockyards, 1775” Journal of British Studies Vol. 8, No. 2 (May, 1969), pp. 44-68, https://www.jstor.org/stable/175216
The Oeconomy of His Majesty’s Navy-Office United Kingdom, Jonas Browne, at the Black Swan and Bible without Temple-Bar, and Richard Mount on Tower-Hill, 1717. https://hdl.handle.net/2027/nyp.33433009302484
Derrick, Charles Memoir of Rise and Progress of the Royal Navy, London: H. Teape, 1806, pg 234
https://hdl.handle.net/2027/nyp.33433009405386?urlappend=%3Bseq=256
Leave a Reply