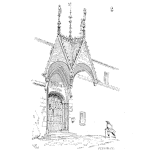
Every product and process has built into it elements that impact the safety, quality and reliability performance.
These features will always be present whether deliberately crafted or not.
For example, a shoddy chainsaw made with weak materials and poorly constructed according to the design may be a hazard to operate and fortunately not operate very long.
On the other hand, a well-designed chainsaw using the best materials and meticulous assembly processes may be a joy to operate and fortunately will operate a very long time.
In both cases the role of management concerning these three elements sets the tone for the design and assembly which results in the product. The management team may focus on performance, or time to market, yet has to set a minimum threshold for safety, quality and reliability. The levels do not have to be best in class, yet should be explicit.
Interrelated Concepts
Safety: “the condition of being safe from undergoing or causing hurt, injury, or loss” (Merriam-Webster.com)
Quality: “a degree of excellence” (Merriam-Webster.com) also defined as “those features of products which meet customer needs and thereby provide customer satisfaction.” Or, “means freedom from deficiencies” (Juran’s Quality Handbook, 5th ed. Joseph M. Juran and A. Blanton Godfrey. P 2.1-2.
Reliability: “The probability that an item will perform a required function without failure under stated conditions for a stated period of time.” (Practical Reliability Engineering, 5th ed. Patrick D. T. O’Connor and Andre Kleyner)
The three definitions appear independent. Let’s look a little closer at the relationships between the three concepts.
Safety and Quality
There are products that are very safe to use and of high quality. As well as products that are unsafe and high quality and every other combination. With a little thought you can list products across the spectrum of combinations.
In general, the safety features of a product work best when of high quality. A table saw blade guard of poor quality may reduce safe operation by jamming or fracturing. A well designed and constructed guard would provide the saw operator protection while enhancing the cutting operation.
A product that uses poor materials or highly variable assembly processes increases the number of defects present. A product that does not operate as expected may increase the safety hazards. And vise versa.
Safety and Reliability
As with quality, at first glance these two concepts are independent. Yet, if the safety features wear out, degrade, or fail during operation, that may create a unsafe conditions, when initially the system operated safely.
Also, if a product fails, in some cases it causes an unsafe condition. For example, if an fuel pump for an aircraft engine fails, the aircraft may lose the ability to continue flying safely. The fuel pump may be of high quality and designed to operate safely, yet due to wear or another failure mechanism, fail, it changes that systems ability to safely operate.
It is a balance though.
One way to improve the reliability of a fuel pump and engine system is to increase the weight, complexity such as redundancy or increases component robustness. With the improvement of system reliability the system safety also improves, yet the increased complexity may decrease the system’s ability to function as expected (quality).
Quality and Reliability
As a reliability engineer, I like to say reliability is quality over time.
Quality professions tend to consider reliability one of many quality aspects of a product. In general a poor quality product tends to be unreliable and likewise, a well designed and crafted product tends to be highly reliable too.
A product that experiences failures, especially partial system failures or specific component failures may lose the ability for specific functions. The system quality is degraded. In some cases a single failure mechanism of one component shuts down the operation of at the product (I.e. Loss of a power supply prevents the use of a desktop).
Some teams argue if a specific failure is related to quality or reliability issues, yet for the customer it really doesn’t matter, they lose the ability to use the product. This is where reliability and quality overlap as the traditional aspects of quality (design features, process control, etc.) when not performed well, leads to product failures, which reliability engineers may work to prevent or minimize.
All three concepts are interrelated.
The ability of an organization to create quality products that are safe and reliable often relies on the management team establishing clear intent with consistent follow though. Every product has these three aspects, whether deliberate or not. Understanding the relationships between the concepts can help you maintain or improve the overall performance of you product.
Leave a Reply