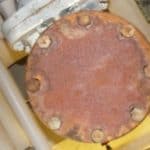
In the previous article I discussed sources of stressors that can cause degradation of the materials in components and joints. In this article I’ll discuss the basics of metal corrosion – the electrochemical cell, seven common forms of corrosion, and examples of metals engineering and mechanical design approaches to control corrosion.
Corrosion
Corrosion is an electrochemical reaction that involves changes in both the metal and the environment in contact with the metal. During the reaction, metal atoms lose electrons – oxidizes – and the environment gains electrons – reduces. As a result of the oxidation the atom becomes a positively charged ion and detaches from the metal.
The reaction occurs when an electrochemical cell is established. An electrochemical cell consists of an anode, cathode, electrolyte, and electrical contact between the anode and cathode. When an electrochemical cell is established, the anode oxidizes – corrodes – and the cathode gains electrons. Various reactions can occur at the cathode. In many cases, the cathode reaction results in the formation of hydrogen gas.
There are different ways an electrochemical cell can be established, resulting in different forms of corrosion. Seven common forms of metal corrosion are:
- Uniform corrosion
- Galvanic corrosion
- Crevice corrosion
- Pitting
- Intergranular corrosion
- Stress corrosion cracking (SCC)
- Dealloying
The electrochemical reaction mechanism is the same for the different forms of corrosion. But, various metallurgical and mechanical design factors will lead to different forms of corrosion.
Forms of corrosion
Uniform corrosion occurs over the entire exposed surface of a metal. Rust on a steel structure or the green patina on a copper roof are examples of uniform corrosion. The corrosion occurs uniformly over the surface of the exposed metal.

The driving force for uniform corrosion is the electrochemical activity of the metal in the environment to which the metal is exposed. The electrochemical activity is determined by measuring the electrode potential of a metal exposed to the aqueous solution of interest. Metals with positive electrode potential have low electrochemical activity and are called noble, with increasing corrosion resistance as the potential increases. Metals with negative electrode potential have higher electrochemical activity and are called active, with decreasing corrosion resistance as the potential becomes more negative.
For example, in saltwater carbon steel is active and gold is noble.
Galvanic corrosion occurs near the junction between two dissimilar metals that are in electrical contact. The driving force for the corrosion is the difference in electrode potentials between the two metals, with the more active metal corroding. For example, if carbon steel is in contact with copper and exposed to rain, the steel will corrode. The larger the potential difference between the metals, the faster the corrosion will occur.

Crevice corrosion occurs in crevices between components and under polymer coatings and adhesives. When the liquid in contact gets into the crevice it stagnates over time, resulting in reduced dissolved ions or oxygen compared to the liquid outside the crevice. As a result, an electrochemical cell is established, with the metal in the crevice becoming the anode and the metal outside becoming the cathode. In many cases, the driving force for the corrosion is the difference between the oxygen concentration inside the crevice and outside the crevice.
Pitting occurs in metals that are normally passive, such as aluminum and stainless steel. Passive metals have a very thin oxide surface layer that protects the underlying metal from the environment. Pitting occurs when the oxide layer breaks down due to attack by the environment. Pitting is a problem if it leads to weakening or perforation of the metal. Also, pitting is a problem for applications where appearance is important since there will be signs of corrosion, such as rust spots on stainless steel.

Interganular corrosion involves corrosion along the grain boundaries of the affected metal. As a result, the metal grains fall away and the metal is weakened. Austenitic stainless steels such as 304 and 316 are examples of metals that can suffer from intergranular corrosion. These alloys are made susceptible to intergranular corrosion when exposed to temperatures in the range of 800 to 1600 F. This happens during welding and other processes. The susceptibility to intergranular attack is a result of changes to the microstructure that result in areas of grains adjacent to grain boundaries having reduced corrosion resistance.

Stress corrosion cracking involves the combined action of stress and exposure to a corrosive environment. In most cases, the stress or environment by themselves are insufficient to cause degradation of the metal. That is, the stress is below the metal’s yield strength and the metal would not corrode in the specific environment in the absence of stress. Together, the stress and corrosive environment case the metal to crack. There are cases where residual stress was sufficient to cause stress corrosion cracking to occur.
Dealloying is the selective leaching of one element from an alloy. This results in the formation of a porous structure that is not strong enough to support the applied mechanical loads. One common example is dezincification of brass alloys used for plumbing, where the zinc is leached out of the alloy.
Factors that influence corrosion rate and form of corrosion
The rate of corrosion of a metal and the specific corrosion mechanism that occurs depend on several factors including metal composition, metal microstructure, environment, component geometry, stress on the component, contact between metals, and the way components are joined together.
Controlling corrosion
From a metals engineering perspective, the following approaches are examples of ways to prevent and control corrosion:
- Select metals that have low corrosion rate in the expected environment.
- Using barrier, galvanic, or anodic coatings over metals
- Proper selection and control of component fabrication and joining processes in order to get the proper metal microstructure.
- When metals will be in contact, select metals that have similar electrode potentials in the intended environment.
- Select metals that have low or no susceptibility to stress corrosion cracking in the intended environment.
From a mechanical design perspective, the following approaches are examples of ways to prevent and control corrosion:
- Eliminate crevices between components by using polymer filler materials.
- When two dissimilar metals are in contact, make sure the more active metal has a larger surface area than the more noble metal.
- Reduce tensile stresses by increasing component cross-section area and/or reducing applied loads.
Corrosion testing
In the next article I’ll discuss corrosion testing, including materials level testing. Materials level reliability testing is a powerful approach for assessing several materials and component and joint designs at once. It takes time and effort to set up the testing, but the cost and time benefits when products pass validation and verification testing the first time are impressive.
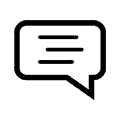
Leave a Reply